Table of Contents
- Why the waterproofing of the building structures is necessary?
- Types of materials used for waterproofing
- Plastering
- Waterproofing arrangement of building structures: what building structures need waterproofing, and what materials are best used for them
- Waterproofing of concrete structures
- Waterproofing of reinforced concrete structures
- Waterproofing of stone structures
- Waterproofing of wooden structures
- Waterproofing of metal and steel structures
- Prices for the arrangement of various types of waterproofing
Why the waterproofing of the building structures is necessary?
Waterproofing of building structures is performed to protect them from water penetration, as well as to prevent the destruction of structures from the action of moisture and an aggressive environment. Properly selected and correctly applied waterproofing guarantees the long-term service of both building structures individually and the entire building as a whole. Most materials such as concrete, brick, FBS blocks, and other similar materials have a porous structure that easily absorbs moisture and water, which negatively affect these materials for 3 main reasons:
- Seasonal temperature difference – water is absorbed into the porous structure of materials such as concrete, freezes there in winter, and thaws in spring, resulting in microcracks and destruction.
- Salts and minerals in the water. As a rule, there are salts and minerals in the groundwater, which over time negatively affect materials such as concrete, brick, and other compounds, leading to their destruction.
- Some materials themselves are afraid of water and with prolonged contact with it can gradually collapse.
Important: Without high-quality waterproofing, structures that are constantly in contact with water will be exposed to it and destroyed as a result.
Types of materials used for waterproofing
Depending on the type of structure, and its location in a building or structure, various waterproofing materials are used to protect against moisture.
Coating:
Coating waterproofing is made, as a rule, on the basis of bitumen. There are the following types of such materials:
- bitumen-polymer;
- bitumen-rubber;
- bitumen-resin elastic;
- bitumen-rubber;
- bitumen-emulsion;
- polymer;
- polyurethane.
Coating waterproofing – is the most common type of material. Various additives in various base compositions, such as bitumen, ensure the elasticity of the material, high-quality operation in heat and cold, as well as ease of application during construction and installation work. Such compositions are applied using brushes or rollers.
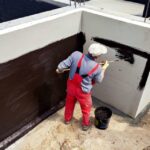
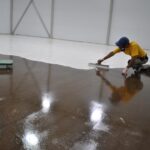
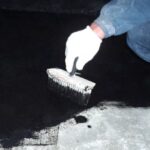
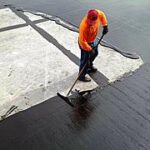
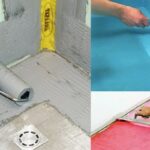
According to the method of application, the following materials are distinguished:
- cold mastics;
- hot mastics.
It follows from the name that cold mastics do not require preliminary preparation before application, while hot ones should be heated to allow the uniform application to the protected surface.
Advantages:
- Low cost (mainly for low-quality bitumen compounds).
- Some mastics, such as bitumen, do not require certain skills in the production of works.
- Good elasticity indicators of the material.
Disadvantages:
- Some compositions are flammable.
- Cheap materials have a relatively short service life.
- Low strength.
Roll surfaced and pasting materials:
This type of waterproofing is a roll of materials made on the basis of polymers. This simplest type of such material- is a roofing material having a paper base. Modern waterproofing is made using PVC, polyester, fiberglass, and glass mesh.
Depending on the type of installation, roll materials are:
- surfaced;
- pasting;
- mounted.
You can read more about the roll waterproofing system in the article – “Roll waterproofing arrangement with detailed installation instructions“.
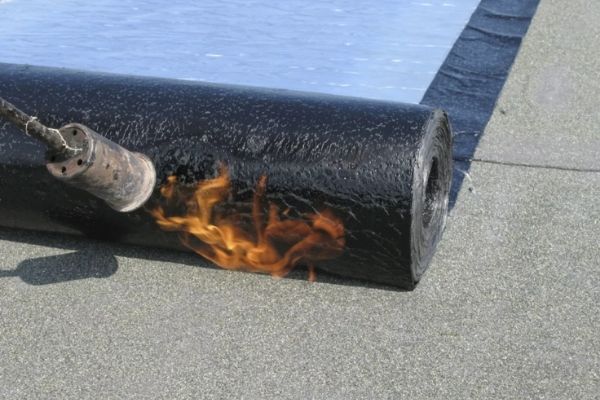
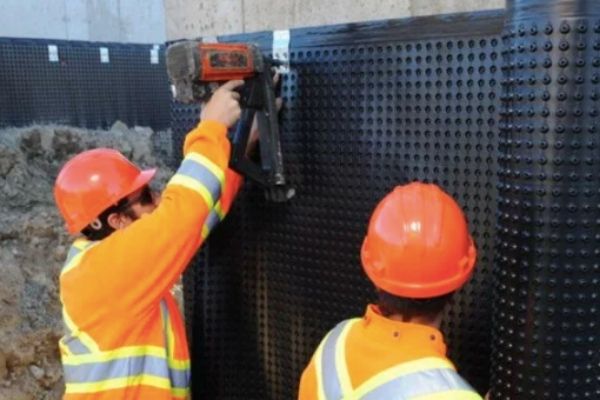
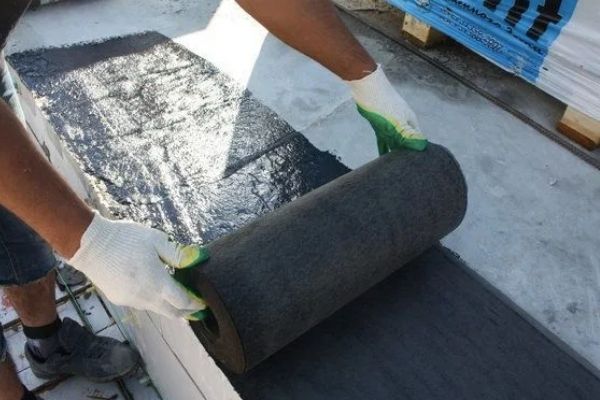
Surfaced:
The inner surface of the deposited roll is covered with a layer of modified bitumen and a protective film. Under the influence of the high temperature of the gas burner, the film melts, and bitumen provides reliable fastening of the material to the surface.
Pasting:
The pasting materials are two layers of bitumen-polymer composition separated by polymer additives. Glue or mastic is used for installation. One of the limitations in the installation of waterproofing materials is the need to carry out work in dry weather.
Mounted:
The mounted roll waterproofing is fixed to the surface using self-tapping screws or special slats, and the seams between the rolls are stitched together with hot air. You can read more about the installed waterproofing system in the article – “Membrane waterproofing: Types of materials and methods of their installation”
Advantages:
- Reasonable cost.
- Possibility of fixation to vertical, horizontal, and included surfaces.
- The technology of work does not require special expensive equipment.
- Some materials can be mounted in winter.
Disadvantages:
- Seams in the insulation arrangement can lead to a violation of the tightness of the protective coating.
- Low maintainability.
- Limited service life.
- In direct contact with water, the service life of most roll materials is 5 years.
Membranes made of various polymers
One of the modern methods of waterproofing building structures is the use of membranes. Polymer membranes can be made on the basis of different compositions. The main types of membranes:
- PVC;
- TPO (Thermoplastic polyolefin);
- EPDM (Ethylene Propylene Dien Monomer).
More information about membrane waterproofing can be found in the article – “Membrane waterproofing: Types of materials and methods of their arrangement”
PVC membrane
PVC membrane is made on the basis of polyvinyl chloride, is an economical solution for waterproofing, and is widely used in construction and installation work. The double-layered structure of the PVC membrane consists of the following parts:
- Upper part – chalk, antipyrins, and plastisizers.
- The lower part – is directly PVC and dyers.
- PVC membranes are available in various thicknesses, for each design you can choose the most rational option.
The membrane is placed directly on the surface of the structure. With the help of a construction dryer under the influence of hot air, the tightness of the seams is ensured.
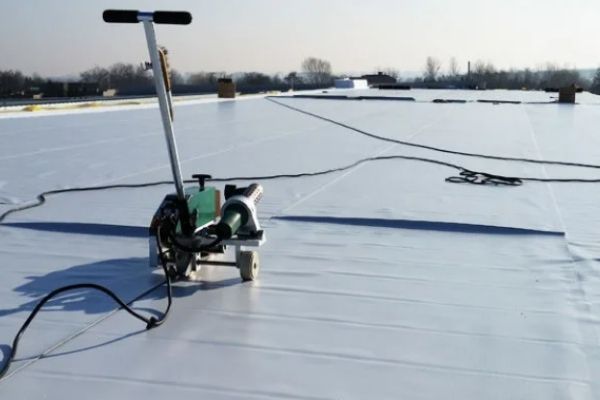
TPO
TPO membranes are made of a polymer mixture based on polypropylene or ethylene-propylene rubber. Also, the TPO membrane is called a rubber one. One of the main advantages of this type of membrane is -high elasticity due to the reinforcing layer of synthetic substances.
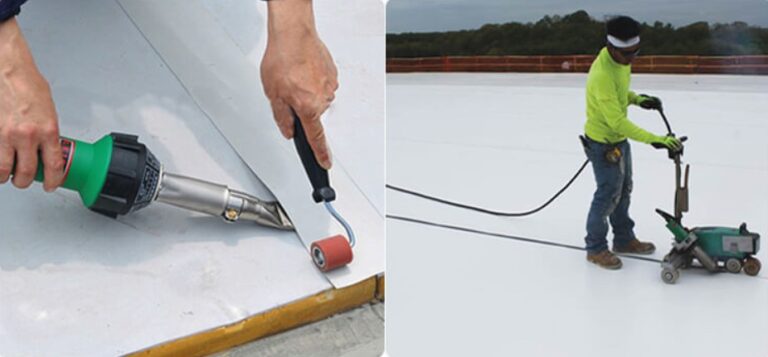
EPDM-membrane
It consists of rubber, soot, clay, vulcanizers, and technical oils. Composite materials can also be used as raw materials. To give strength between the layers of the membrane, a reinforcing mesh of polyester is laid.
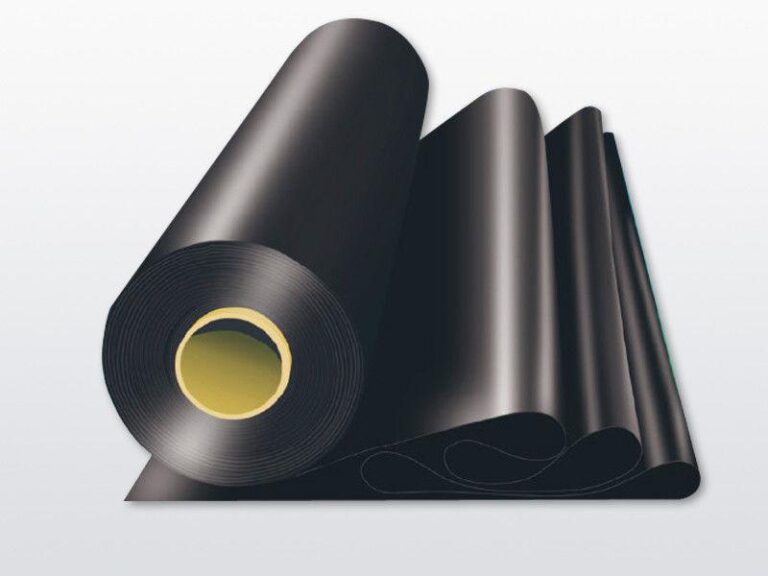
Advantages of most types of membranes:
- Possibility of laying in various weather conditions.
- Resistance to UV radiation.
- Resistance to mechanical damage.
Disadvantages of most types of membranes:
The presence of seams between the sheets, and seams — are the weakest point in any waterproofing coating.
Complete lack of adhesion to the base, the membrane lies on the surface of one carpet and if water enters under it through a weak joint, it will be able to move freely from one place to another, appearing as a wet spot or leak in the weakest point of the structure.
According to the method of laying PVC, TPO, and EPDM membranes, the following nuances can be distinguished:
- Membrane sheets can be mounted by welding, construction tape, or glue.
- Profiled membranes are laid using self-tapping screws, pressure strips, crossbars, and strips.
Liquid rubber
Liquid rubber – is a waterproofing material made on the basis of bitumen and latex. It has good elasticity and water resistance properties.
Liquid rubber can be applied in 2 ways:
- Manually by the method of coating;
- By spraying with the help of special spraying equipment;
Liquid rubber is made in the form of a one- or two-component composition. During construction and installation works, it does not emit harmful substances. With the help of liquid rubber, a seamless protective waterproofing coating of the surface can be performed.
Advantages:
- High-quality moisture protection due to the seamless surface and good technical characteristics.
100% adhesion to the base. - Maintainability. Gaps in the surface can be sealed with a new layer of liquid rubber.
- Durability.
Disadvantages:
- Cost of compositions.
You can read more about liquid rubber in the article – “Waterproofing with liquid rubber“.
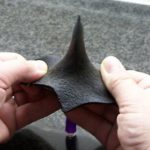
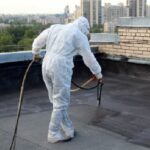
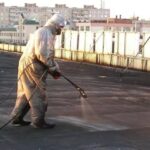
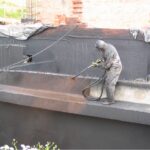
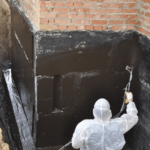
Polyurethane waterproofing
There are 2 types of polyurethane waterproofing:
- Single-component. The main substance in such a material – is a polyurethane resin. It can be used for waterproofing internal and external surfaces.
- Double-component. The composition of such mastic includes resins and binders. It has a wide range of applications for various building structures. Also, double-component mastic can be used for waterproofing tanks with drinking water due to its environmentally friendly composition.
The procedure for applying polyurethane waterproofing:
- The surface should be prepared.
- Concrete surfaces should be leveled and cleaned.
- Mastic is applied with a roller, or brush, or sprayed on the surface in several layers.
- Each layer should dry before applying the next one.
- When carrying out work, it is necessary to take into account the air temperature, which can be from +5°С to +35°С.
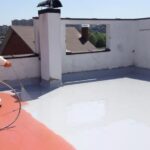
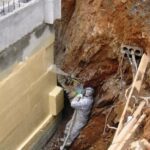
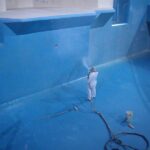
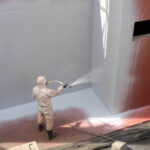
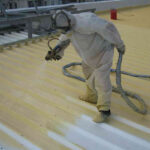
Advantages:
- Suitable for both new construction and renovation work.
- No seams;
- Full adhesion to the base;
- High quality and reliability;
- Environmental friendliness and safe composition.
Disadvantages:
- Careful preparation of the substrate surface is required before application.
You can read more about polyurethane waterproofing in the article – “Polyurethane waterproofing“.
Cement
Cement types of waterproofing materials consist, as a rule, of cement and various polymers that are added to it. Special emulsions are added to such mixtures, usually based on acrylic.
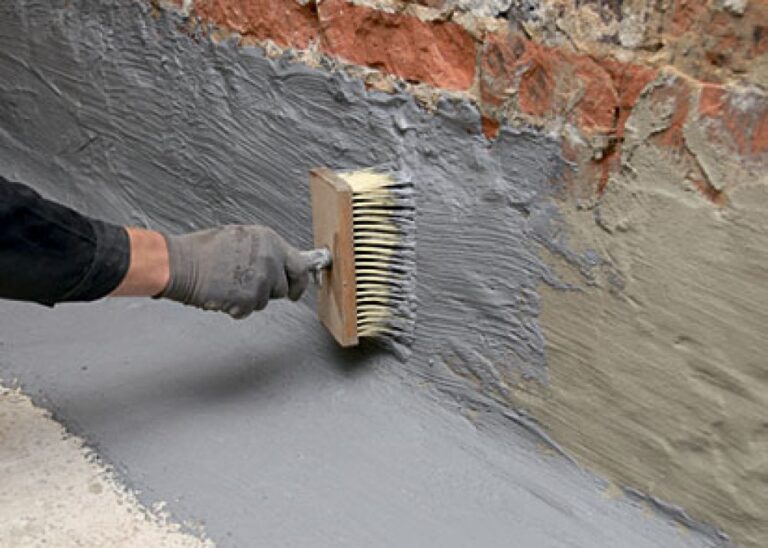
Advantages:
- Affordable price.
- Compositions can be used in structures directly in contact with water.
- Plasticizing additives allow for the achievement of good technical indicators of the mixture.
- Some compositions can withstand negative water pressure.
Disadvantages:
- Poor resistance to deformation, possible cracking.
- The long process of applying materials.
- Compositions without additives have a short service life.
You can read more about cement waterproofing in the article – “Cement-based waterproofing: Features, types, and methods of its application“.
Plastering waterproofing is made on the basis of binding materials that give the main characteristics of the composition, and auxiliary components that are used to impart certain additional properties to the mixture.
The following materials can be used as binders:
Plastering
- Organic: bitumen, tar, resin, thiocol, latex.
- Inorganic: liquid glass, cement.
- Additional components can be:
- Plastizers: dibutyl phosphate.
- Solvents: gasoline, kerosene, acetone.
- Fillers: mica, quartz, talc powders; asbestos fibers, or synthetic substances.
- Hardeners: various types of resins.
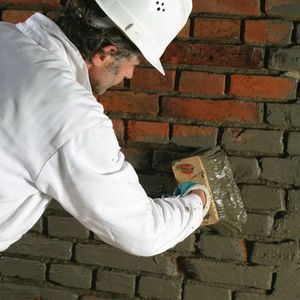
The main options for plaster waterproofing:
- Asphalt. Asphalt concrete or asphalt-based solutions and mastics are used for its manufacture. Such a mixture can be applied in hot and cold forms. Before applying, the surface is cleaned, and a reinforcing fabric or mesh is mounted at the joints, kinks, and corners.
- Cast asphalt waterproofing. The heated asphalt mixture is applied by pouring it onto the prepared surface, then it is evenly distributed. Such waterproofing is suitable for use on horizontal surfaces. Installation work can also be carried out at subzero temperatures. Additional protection from moisture is provided by applying an extra layer of asphalt mastic with the addition of asbestos.
- Cement-sand plaster waterproofing. This material contains Portland cement, waterproof non-shrinkable, or expanding cement. The composition also includes modifying additives in the form of sealing components and surfactants. The work is carried out at a temperature not lower than +5°С.
2 methods can be used for the plaster waterproofing arrangement:
- manually with a brush or a spatula;
- using a mechanical sprayer.
Advantages:
- High strength.
- It protects all major building structures: monolithic, concrete, stone, and cement.
- Can be used for both external and internal waterproofing.
Disadvantages:
- Professionals should carry out the work.
- Low elasticity.
You can read more about plaster waterproofing in the article – “Plaster waterproofing: Types of materials, their characteristics and methods of application“.
Penetrating
The principle of operation of penetrating waterproofing is based on the fact that it penetrates into the depth of the building structure, forming insoluble crystals in all pores. Unlike all the above options for waterproofing materials, the penetrating one protects not only the surface of the building structure but also its inner part.
Such waterproofing, as a rule, consists of Portland cement, quartz sand, and special chemical ingredients. It is used directly during the installation of building structures. The composition can also be used for repair work.
The following substances are used for the manufacture of penetrating waterproofing compounds:
- siliconates;
- silicates;
- siloxanes;
- silanes;
- fluorine.
The most popular penetrating waterproofing materials are Penetron, Aquatron, Dehydrol, Lakhta, Kalmatron, and Crystallizol W12.
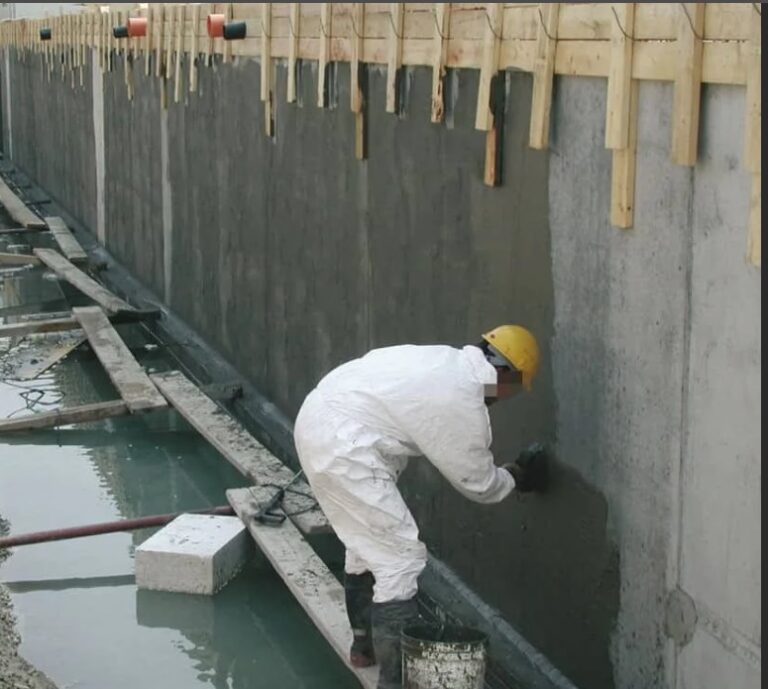
Advantages:
- Improve the properties of concrete. They provide air- and vapor permeability, and resistance to temperature changes.
- Have a non-toxic composition.
Disadvantages:
- All penetrating materials work only where good concrete is poured, in places where there are pores, capillaries, microcracks, and other voids in the concrete, penetrating materials will not work.
- Positive temperatures are required for the work.
- It is impossible to apply mixtures on surfaces not based on cement-sand. For example, it is not suitable for brick, aerated concrete, or foam concrete.
- Complex surface preparation.
- This type of mixture requires long-term care after application.
You can read more about penetrating waterproofing in the article – “Penetrating waterproofing: A detailed description of its work on concrete, types of materials and application technologies“.
How penetrating types of waterproofing work in the thickness of concrete: Interaction scheme
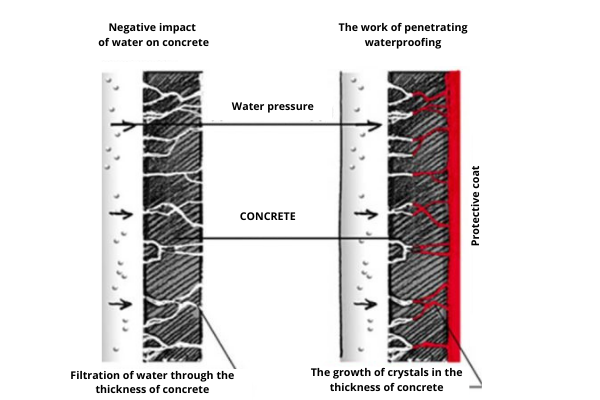
Injection
Injection waterproofing is used in cases, where it is not possible to perform another waterproofing option. In this way, structures are protected from the inside. In the case of injection waterproofing, materials are pumped into the structure under pressure. At the same time, they fill all the existing pores in the structure itself, squeeze out existing moisture and form a protective barrier.
The injection compositions are based on the following materials:
- polyurethane-based polymer gels;
- acrylate solutions;
- compositions of silicone compounds;
- epoxy resins;
- polyurethane.
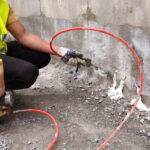
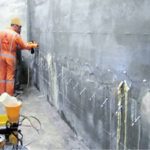
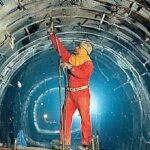
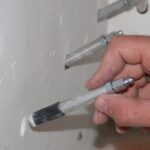
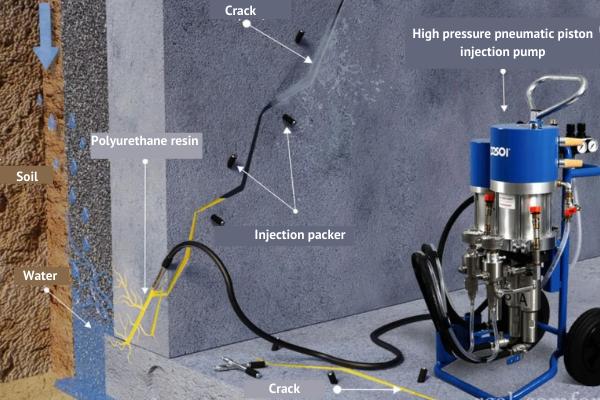
Advantages:
- It is not required to carry out excavation work outside.
- The possibility of using materials in conditions of high humidity.
- The high degree of protection when exposed to groundwater.
Disadvantages:
- High cost of materials and work performance.
- Special equipment should be used.
You can read more about the injection method of waterproofing in the following article – “Injection waterproofing“.
How the injection method of waterproofing works: Interaction scheme
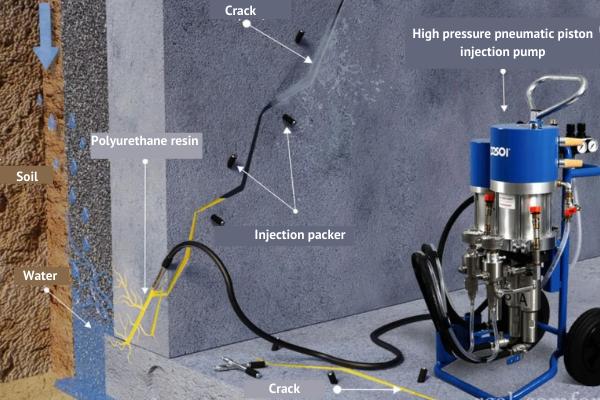

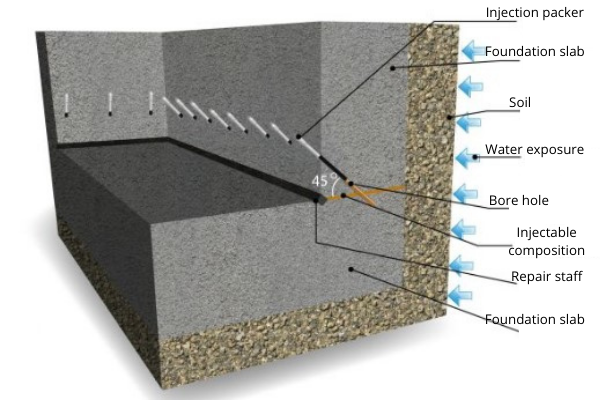
Waterproofing arrangement of building structures: what building structures need waterproofing, and what materials are best used for them
For each type of structure and for each material from which a particular structure is made, it is necessary to provide its own waterproofing technology and suitable waterproofing material for it.
What structures need to be protected from water and moisture:
It is obligatory at the design stage of buildings and structures to provide waterproofing protection for the following types of structures:
- foundations;
- foundation slabs;
- underground floors;
- socle floors;
- flat roof;
- pitched roofs;
- floor slabs;
- balconies;
- terraces;
- swimming pools;
- liquid storage tanks;
- all the elements of buildings and structures that are directly affected by water and moisture;
- pond and artificial reservoirs;
- roads;
- tunnels.
As a rule, when carrying out waterproofing works, special attention should be paid to such structural elements as:
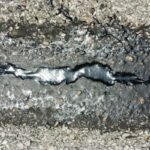

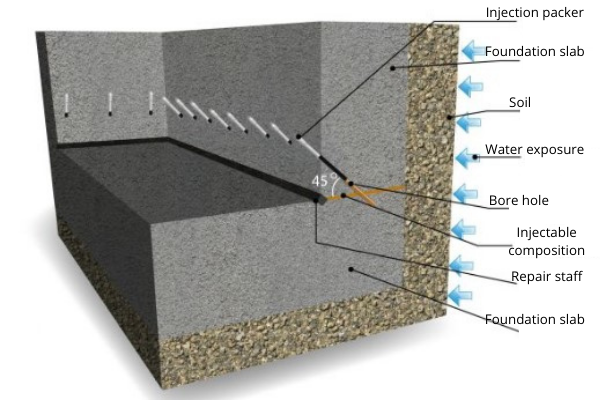
Structures made of what materials require protection from water exposure?
Concrete, reinforced concrete, stone, metal, and wooden structures are used for the construction of buildings and structures. Each variant of such a design needs protection from water and moisture if it is located in the area of influence of an aggressive external environment.
Concrete and reinforced concrete structures have very high strength, but since concrete is permeated by micropores in its structure, water and moisture from the environment can get into them (absorb). In reinforced concrete structures, the impact of water leads not only to the destruction of concrete but also to the corrosion of reinforcement. Such prolonged exposure leads to the destruction of the structure and the loss of the original strength characteristics.
Waterproofing of concrete structures
To protect concrete structures from water and moisture, the following types of waterproofing can be used:
- coating;
- pasted or surfaced;
- polymer membranes;
- liquid rubber;
- polyurethane waterproofing;
- cement;
- plastering;
- penetrating;
- injection.
The use of a specific waterproofing option is determined based on several indicators, in particular:
- Type of construction (wall, column, ceiling).
- Condition of concrete.
- Budget for waterproofing works.
- Characteristics of groundwater, technology.
- Climatic conditions in which the house or building is located.
- The possibility of using one or another type of waterproofing also depends on what type of structure needs protection. The foundation, the underground floors of a house or parking lot, a swimming pool, a balcony or reservoirs for storing drinking water, places for entering communications into a building, a roof — all these structures require different approaches to protection from water and moisture.
Important: Materials such as liquid rubber and polyurethane system have an undeniable advantage over other options when performing waterproofing of concrete structures from the outside. They are applied to any type of surface and provide 100% of adhesion to concrete.
You can read more about the waterproofing of concrete structures in the article – “Concrete waterproofing and how to do it: Types of materials and methods of arrangement“.
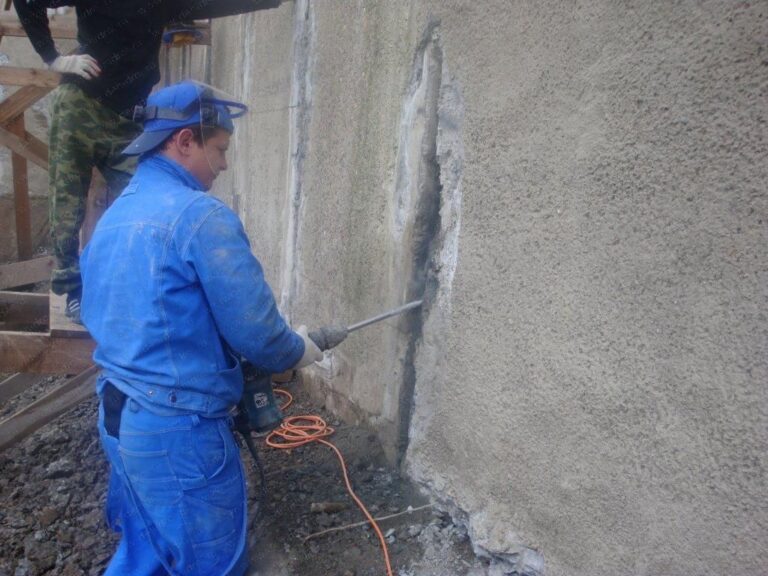
Waterproofing of reinforced concrete structures
For waterproofing reinforced concrete structures, all the above types of materials are used by analogy with concrete protection.
As for concrete, the most effective and reliable material of protection against moisture and water for reinforced concrete structures is liquid rubber or polyurethane.
Their use guarantees the reliability of the structure and increases the durability of the building as a whole. This effect is achieved due to good technical indicators, the absence of seams on the surface of reinforced concrete, and absolute adhesion to a vertical, horizontal, or inclined surface.
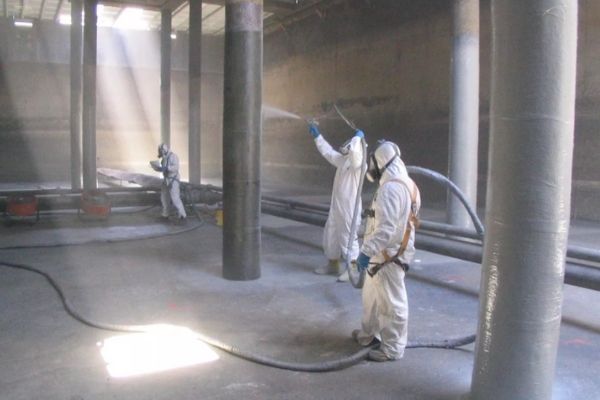
Waterproofing of stone structures
Seamless coating waterproofing, liquid rubber, and cement types of protection can be used to protect stone structures. It is performed for both horizontal and vertical surfaces. Masonry is characterized by the ability to absorb and pass water well, so the requirements for waterproofing for it are increased.
The predominant types of waterproofing for such masonry are polymer cement solutions or liquid rubber. They provide reliable adhesion to the surface of stone structures, there are no seams when performing the waterproofing surface, due to which the guaranteed operation of the protective layer is ensured.
You can read more about brick and stone structures in the following articles:
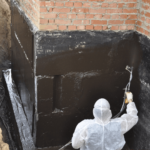
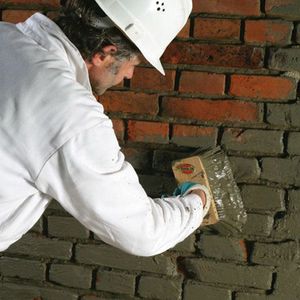
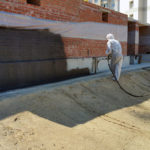
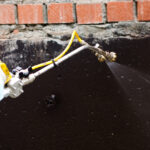
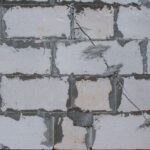
Waterproofing of wooden structures
Wooden structures are sensitive to humidity, and in addition to deformations from exposure to water, fungus and mold can be formed on their surface. The following options are used for waterproofing wooden structures:
- Coating waterproofing. Cold-applied mastics can be used for waterproofing wooden vertical and horizontal structures. The advantage of this method is the ability to perform work on surfaces of complex configurations.
- Paint waterproofing. It is applied after cleaning the surface of wooden walls or floors. Thanks to special additives, such mixtures can be used to insulate wooden surfaces.
- Cast waterproofing. A reliable type of protection for vertical, horizontal, and inclined structures. It has a high cost, but also the greatest reliability.
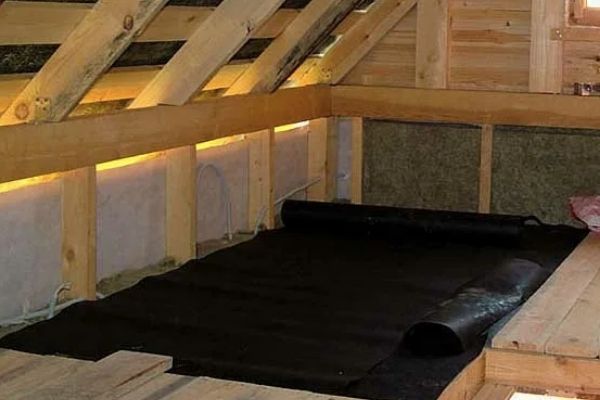
Waterproofing of metal and steel structures
Metal structures (pipes, tanks, steel parts), located in the ground or in the open air, directly in contact with water, are subject to corrosion.
For waterproofing of such elements, the following options can be used:
- painting;
- pasting;
- coating.
Polyurethane waterproofing has an advantage over other options for protecting metal products. Due to its properties, the material has a reliable adhesion to the metal surface. The absence of seams when performing work ensures greater reliability of work.
You can read more about the waterproofing of metal structures in the article – “Waterproofing of metal and metal structures “
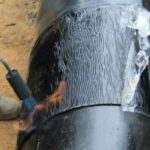
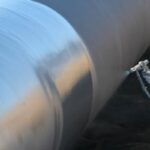
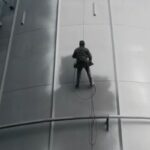
Prices for the arrangement of various types of waterproofing
All prices are preliminary and may vary depending on the complexity of the work and other features of a particular project.
Description of work | Unit of measurement | Price in $ |
The arrangement of surfaced waterproofing on the horizon | m2 | 36 |
The arrangement of surfaced waterproofing on the vertical | m2 | 49 |
Arrangement of a self-adhesive membrane on the horizon | m2 | 35 |
Arrangement of a self-adhesive membrane on a vertical | m2 | 48 |
Arrangement of PVC membrane on the horizon | m2 | 58 |
Arrangement of PVC membrane on the vertical | m2 | 68 |
Application of polyurea | m2 | 90 |
Application of mastic waterproofing | m2 | 20 |
Application of liquid rubber by spraying | m2 | 25 |
Application of liquid rubber manually | m2 | 33 |
Application of cement-mineral double-component waterproofing | m2 | 60 |
Polyurethane waterproofing arrangement | m2 | 60 |
Application of penetrating compounds | m2 | 60 |
Application the primer | m2 | 10 |