Table of Contents
- Causes of tunnel leaks
- Features of tunnel waterproofing
- Materials, methods, and technologies for tunnel waterproofing
- Restoration of waterproofing in tunnels
- The cost of tunnel waterproofing services
Underground structures and tunnels are being built to meet the growing need for infrastructure, as well as other utilities. For most underground structures, the flow of water from groundwater should be limited, although the level of restriction of its flow to different structures may be different. Waterproofing of underground structures, including tunnels, is often a key problem, and various solutions have been tried to ensure it.
Causes of tunnel leaks
The failure of the waterproofing system may be due to several reasons:
- Design error – when designing the waterproofing system, an unsuitable material was chosen for this.
- Construction error – The waterproofing material was applied with a violation of technology, which eventually led to leaks.
The consequences of these errors may not be visible immediately, but after some time, for example, during the operation and maintenance of structures. It is well known that the reliability of a structure strongly depends on the quality of its construction and the specific variables of the project. In the absence of high-quality waterproofing, leaks, cracks, and other adverse and dangerous phenomena may form in tunnels.
Important: if there are water leaks in the tunnels, it means that the waterproofing from the outside has become unusable and requires repair. If it is impossible to perform repairs from the outside, it can be performed from the inside using an injection system.
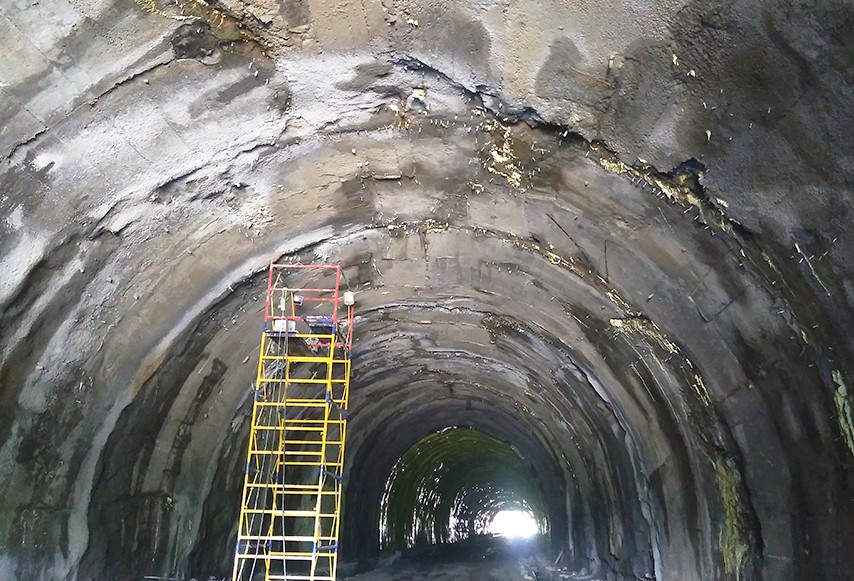
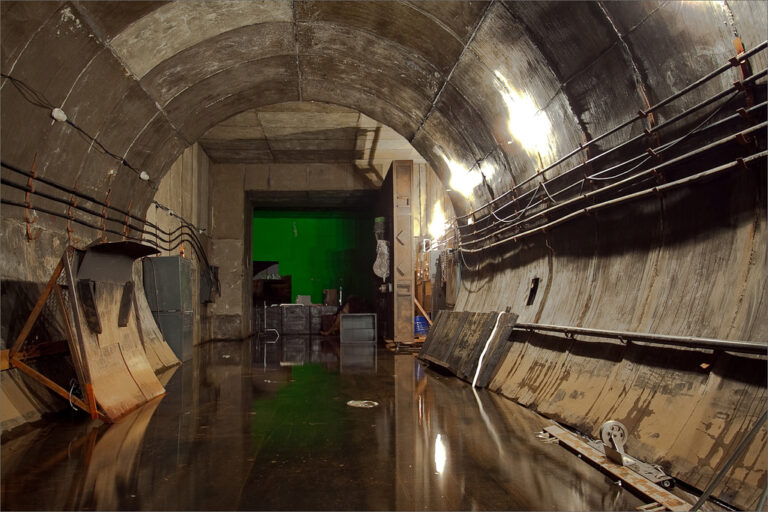
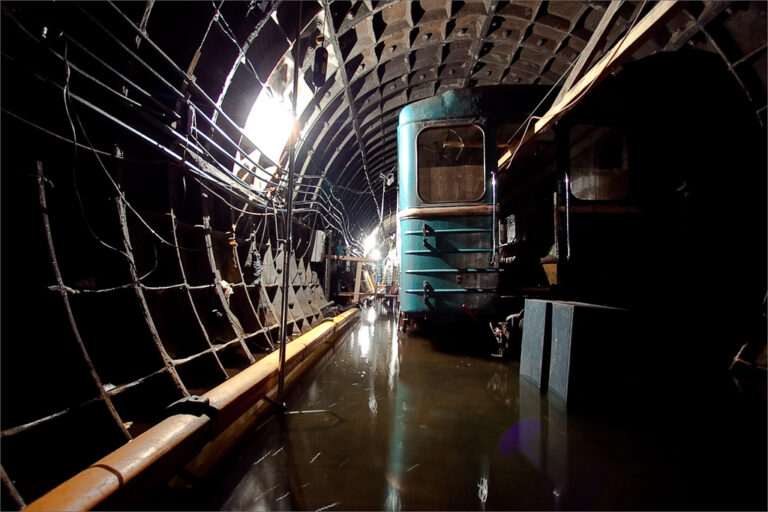
Features of tunnel waterproofing
The conditions for waterproofing in tunnels are similar to the same requirements as for waterproofing underground structures and parts of buildings. Accordingly, when performing waterproofing works in tunnels, it is necessary to take into account the following points:
- Selection of high-quality and reliable material – Reliability has certain parameters that the material should meet, including The warranty period of the material, resistance to aggressive environment and chemical elements;
- Surface preparation – the quality of the surface preparation (cleaning of dust and dirt, removal of sharp corners, etc.) depends on the quality of the waterproofing application;
- Compliance with design standards and installation technology of waterproofing coating – The service life of waterproofing and the absence of leaks within the warranty period directly depends on compliance with the technology.
Types of tunnels
Currently, tunnels are widespread in almost every city. Tunnels can be built in an open or closed way (with or without opening the surface).
Tunnels can be classified according to their purpose:
- The communication routes – this type includes subway tunnels, tunnels for highways, and pedestrian tunnels.
- Hydrotechnical – their purpose in supplying water to settlements, hydroelectric power plants, and other structures.
- Utility– refers to tunnels intended for the municipal services of a city or enterprise. For example, sewage, water supply, collectors, tunnels where telephone and electrical networks pass, etc.
- Mining – designed for enterprises that exact minerals.
- Special tunnels – Designed for defense structures, underground power plants, and garages.
Tunnels can be classified by location:
- Mountain
- Underwater
- Plain – Basically, we are talking about tunnels built in cities. For example, tunnels for metro, for vehicles, underground pedestrian crossings, underground garages, etc.
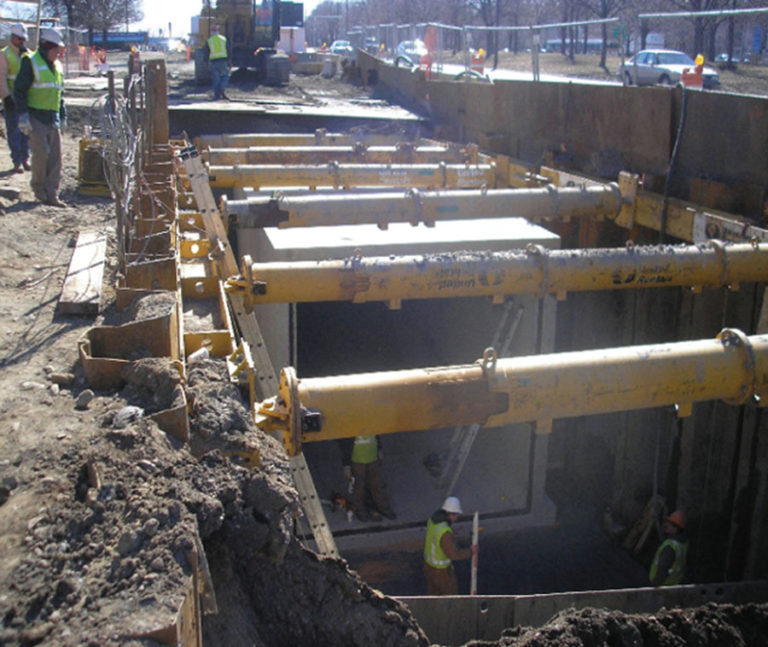
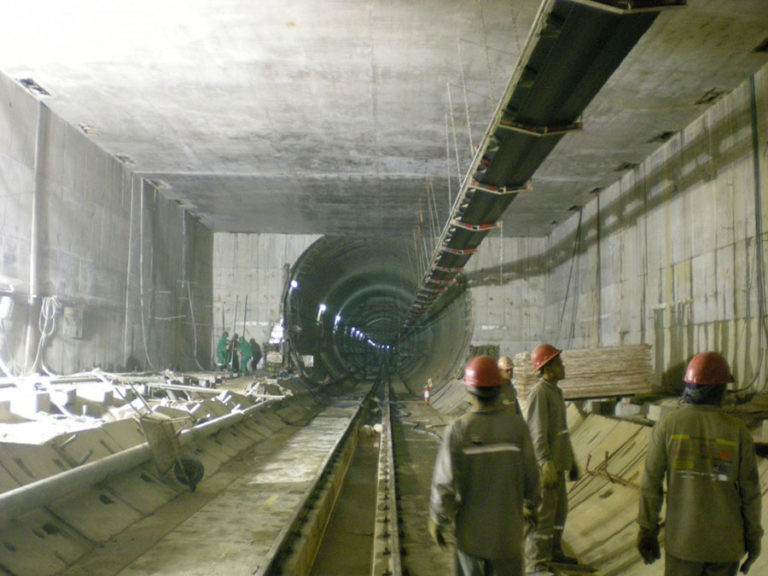
Materials, methods, and technologies for tunnel waterproofing
High-quality waterproofing of tunnels for various purposes, including for the needs of metro and pedestrians, can provide them with protection from water penetration for many years. At the same time, the lack of good and durable protection can lead to leaks and expensive repairs, especially if the structure is underground.
There are several proven methods and technologies for waterproofing:
- Waterproofing of tunnels with membranes. PVC and Low-Pressure Polyethylene membranes are used as waterproof membranes.
- Polyurethane waterproofing.
- Waterproofing with liquid rubber.
- Injection waterproofing.
Waterproofing of tunnels with membranes
When using PVC membranes as an insulating coating, sheet membranes are mechanically fixed to the bases, which are sewn together with a special hairdryer.
Disadvantages of this method:
- The presence of seams and joints – seams and joints are the weakest points in any waterproofing coating.
- Lack of adhesion to the base – the membrane lies like a carpet and has no adhesion to the surface. If the seam breaks somewhere and water passes through there, this water will begin to pass under the entire insulation and will be detected from the inside only in the weakest place, which will not make it possible to detect the source of water penetration under the membrane.
One of the most famous materials made of PVC is Sikaplan from Sika.
Detailed instructions on the use of this material in waterproofing and tunnel protection can be found in the following manual: Waterproofing of tunnels with Sikaplan membranes.
You can read more about membrane waterproofing in the article – “Membrane waterproofing: Types of materials and methods of their installation“.
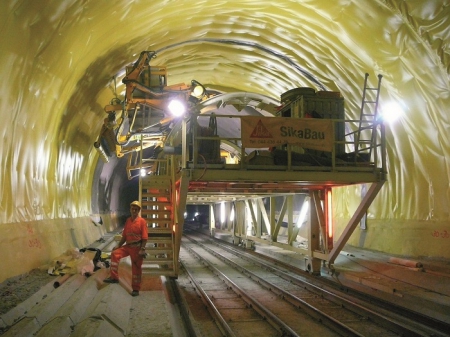
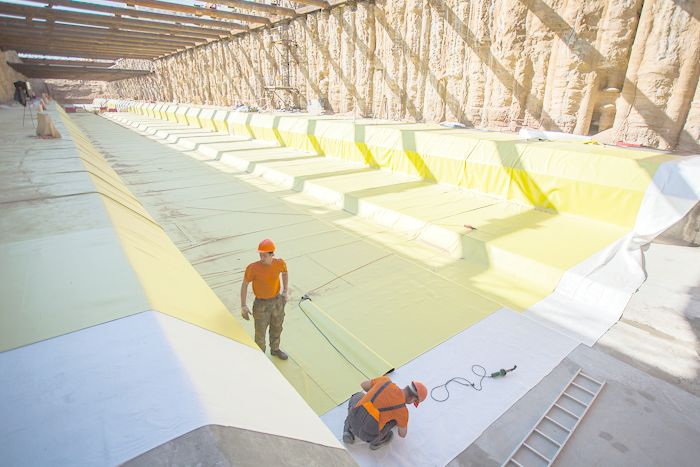
In recent years, an alternative to standard membranes has been introduced, and it has been successfully used in several practical tunnel projects, including for metro construction. This alternative is Polyurethane waterproofing and liquid rubber waterproofing.
Waterproofing with sprayed liquid rubber
Liquid rubber — is a double-component bitumen-latex emulsion with the addition of polymers. Sprayed compounds are – a new system for protecting tunnels from penetration and exposure to water and an aggressive environment. The conditions for using this system as a waterproofing are excellent in terms of deformation, dynamics, surface condition of the first layer of concrete, groundwater intake, and pressure on the coating itself. The results obtained show that the use of a sprayed waterproofing membrane in a tunnel will serve much longer.
For underground structures, subways, and tunnels, the advantages of sprayed liquid rubber are significant:
- Elasticity coefficient of 800% and higher – This means that with the dynamics, deformation, or mobility of the structure, the material will not disperse, tear or crack, but will stretch. When stretched, the material will not lose its characteristics and qualities.
- No seams – Liquid rubber is sprayed and turns into a single coating without seams and joints.
- 100% adhesion to the base – When using sprayed insulation as waterproofing, when a water stream enters, the source of the leakage is easily localized since there can be no water migration between the membrane and concrete substrate since the sprayed waterproofing membrane has 100% adhesion to the surface. This feature strongly distinguishes this method from a convenient composite cladding system, in which the water entry point may differ from the source of leakage behind the sheet membrane.
- Application rate – 600-900m2 of insulation can be applied per day by spraying.
One of the most famous compositions of liquid rubber is FlexLock from HYDRO. It is this composition that has been repeatedly used in the construction of metro facilities and other significant facilities.
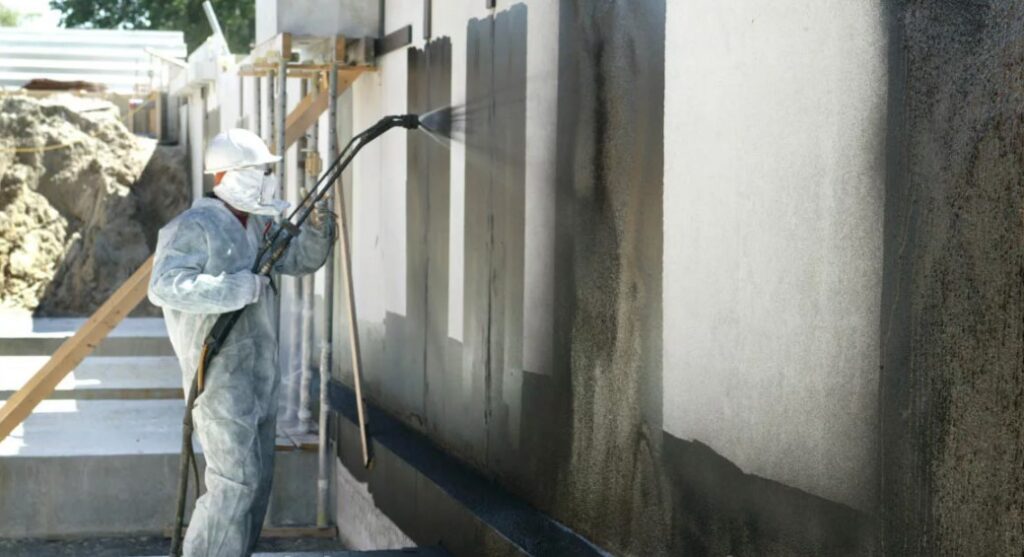
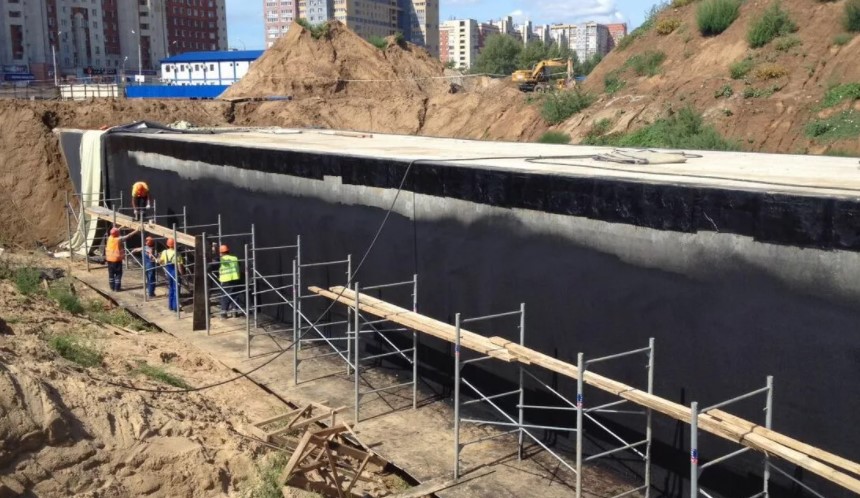
Conditions necessary for applying sprayed waterproofing for tunnels:
Read the terms
- It is necessary to clean the surface – A clean concrete surface without dust, dirt, and peeling elements accompanies a high-quality waterproofing application. Particles and dirt on the concrete surface can lead to the destruction of the bond between the liquid rubber and the base itself. Application on a clean surface, free of dust and sharp corners provides ideal conditions for the adhesion of waterproofing.
- Sharp stones and ships – should be removed, as they can subsequently harm the healing properties of the coating.
- Smooth surface – Test results and practical examples show that the roughness of concrete does not directly affect the mechanical properties of the waterproofing coating, such as the strength of adhesion to concrete. But the less smooth the concrete surface, the thicker and more material will be applied to ensure the desired water resistance.
- Dry base – Liquid rubber, can only be applied to a relatively dry surface.
Injection waterproofing for tunnels
Injection waterproofing is mainly used to stop leaks from inside a problematic structure. When using this method, polyurethane or helium resins of various viscosities are injected into the problem area of concrete to seal existing cracks, voids, and pores concrete. These resins fill the empty space, thereby preventing water from passing inside the structure and continuing the process of destruction.
The injection insulation method is also suitable for:
- Sealing joints
- Sealing of communication entry points
- It is used as veil waterproofing
One of the most famous injection materials is HydroInject from HYDRO. It is the composition that has been repeatedly used in the construction and repair of metro facilities, pedestrian tunnels, and other underground structures.
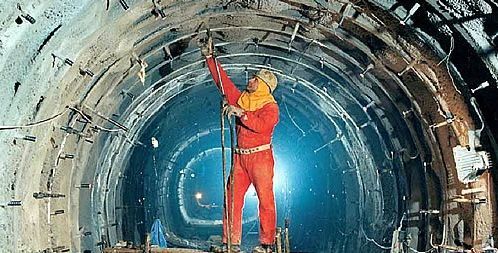
Restoration of waterproofing in tunnels
If leaks are found in the tunnels, this means that the waterproofing from the outside is broken or missing. In this case, it is necessary to take certain measures to restore it. Waterproofing restoration is best done from the outside, solving the root of the problem. If it is impossible to perform work from the outside, restoration can be done from the inside.
Outside:
- If it is possible to find damaged or weak areas of the waterproofing coating — then you can make local repairs to these areas, thereby restoring the integrity of the coating and solving the problem of leaks.
- If it is not possible to detect the exact place where the insulation is broken – When it comes to the membrane type of insulation, by the nature of leaks from the inside it is impossible to understand where the water flows from the outside since this material lies in the carpet and water enter through a weak seam in one place and move from place to place under the insulating carpet. In this case, you will have to dig out the structure completely (if it is underground) and most likely dismantle the old insulation completely, and then re-mount.
From inside:
Restoration and repair of waterproofing from the inside can be done in two ways:
- Veil waterproofing – Through holes are drilled in the walls of the tunnel, where injectors are inserted. Through these injectors, polyurethane resin is pumped behind the wall, forming a waterproofing screed between the ground and the wall.
- Injection waterproofing – Small holes are drilled in the walls, and packers are inserted there, through which polyurethane or helium resin is pumped into the body of concrete or brick. The composition injected under pressure fills the voids, pores, and microcracks in the base, thereby making these places waterproof.
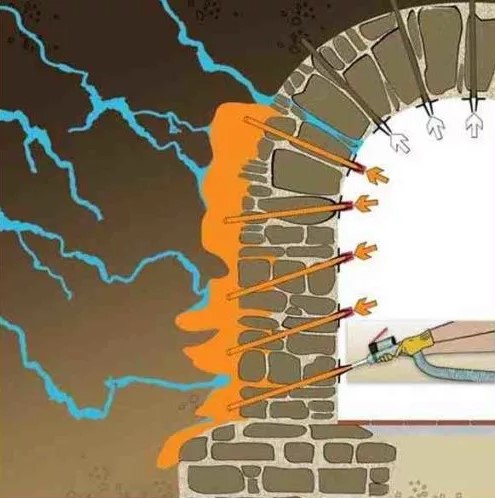
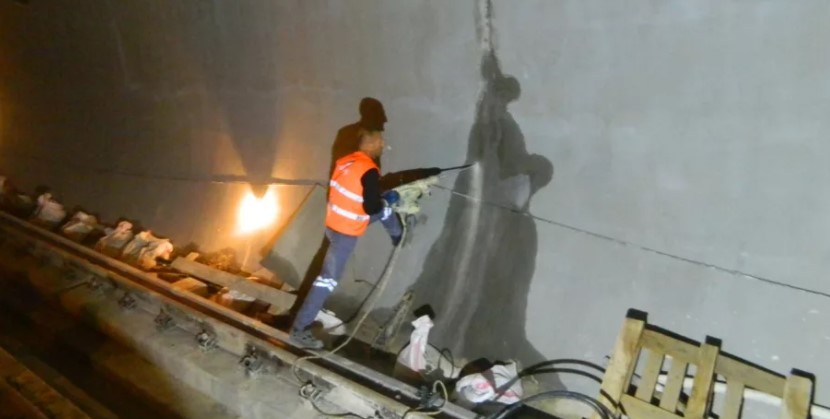
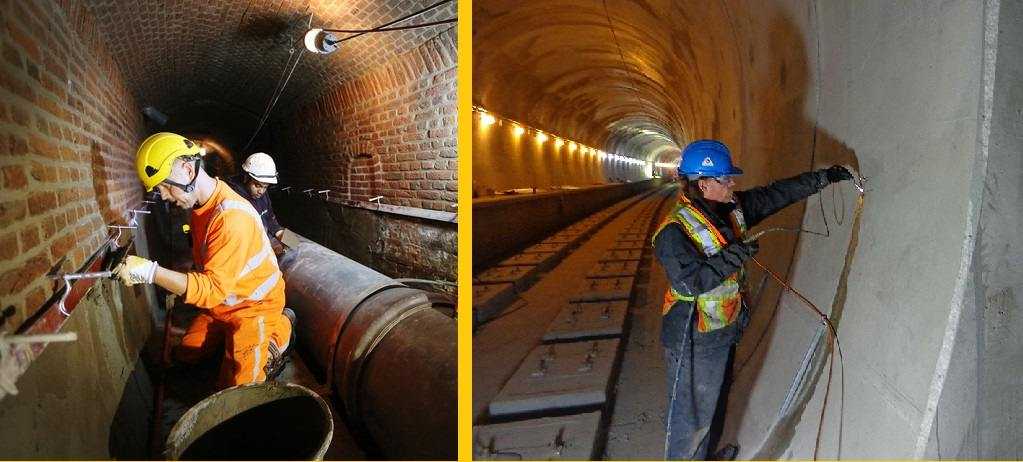
How is the waterproofing of pedestrian tunnels carried out
Underground pedestrian crossings occur mainly in places where cold and deformation seams are formed, as well as in paces where communications are entered. Sometimes wet spots or cracks with leaks are visible on the walls of the pedestrian zone. If we are talking about restoring insulation in an underground pedestrian crossing, then injection insulation of the following constructs is most often used here:
- Waterproofing of leaks and sealing of cracks
- Sealing and waterproofing of cold and deformation joints
- Sealing and waterproofing of communication inputs
- Injection into the body of concrete or brick
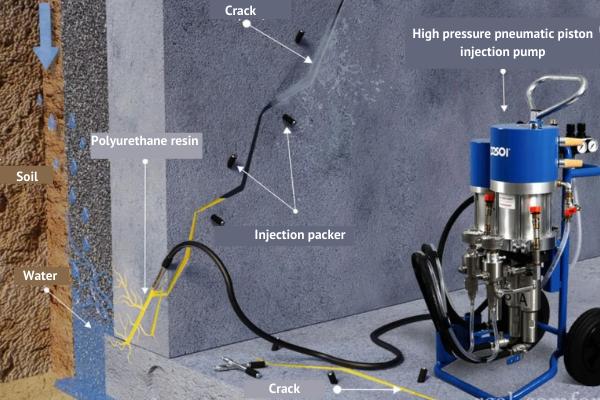

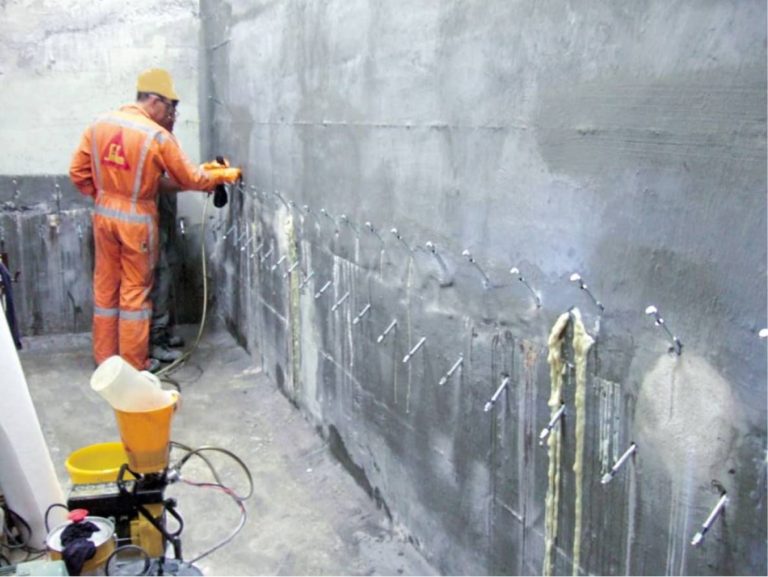
The cost of tunnel waterproofing services
The prices for the main works are indicated without taking into account the complexity of the work and other nuances that may affect the final prices. To obtain an accurate estimate and final cost, you can send your technical specification to our mail or call our engineer to inspect your facility and compile the necessary technical specifications for the estimate.
Description of work | Unit of measurement | Price in $ |
Work on the arrangement of surfaced waterproofing | m2 | 10 |
Work on the arrangement of PVC membrane | m2 | 18 |
Work on the arrangement of polyurea | m2 | 30 |
Work on the arrangement of mastic waterproofing | m2 | 8 |
Work on the arrangement of liquid rubber by spraying | m2 | 8 |
Work on the arrangement of liquid rubber manually | m2 | 10 |
Work on the arrangement of cement-mineral double-component waterproofing | m2 | 20 |
Work on the arrangement of polyurethane waterproofing | m2 | 20 |
Applying the primer | m2 | 8 |
Work inside:
Description of work | Unit of measurement | Price in $ |
Waterproofing of cold joints: -Work on the installation of indenting -clearing the indenting -layer-by-layer sealing of non-shrinkable composition | running meter | 20 |
Waterproofing of interblock joints: -Work on the installation of indenting -clearing the indenting -layer-by-layer sealing of non-shrinkable composition | running meter | 15 |
Waterproofing of expansion joints: -Work on the installation of indenting -clearing the indenting -sealing of the elastic profile -layer-by-layer sealing of non-shrinkable composition -a complex works on injection | running meter | 180 |
Injection waterproofing of seams/cut-off waterproofing -Work on the installation of indenting -clearing the indenting -layer-by-layer sealing of non-shrinkable composition -Work on the installation of boreholes and installation of packers -a complex of works on injection -dismantling of packers and sealing of injection holes | running meter | 100 |
Injection waterproofing in the body of concrete -marking, Work on the installation of boreholes and assembly of packers -a complex of works on injection -dismantling of packers and sealing of injection holes | m2 | 120 |
Injection waterproofing into the brick body -marking, Work on the installation of boreholes and assembly of packers -a complex of works on injection -dismantling of packers and sealing of injection holes | m2 | 150 |
Cement-mineral waterproofing | m2 | 20 |
Penetrating waterproofing | m2 | 20 |
Waterproofing of places of communications entry: -Work on the installation of indenting -clearing the indenting -layer-by-layer sealing of non-shrinkable composition -Work on the installation of boreholes and installation of packers -a complex of works on injection -dismantling of packers and sealing of injection holes | piece | 250 |