Table of Contents
- Types of tanks
- Why is waterproofing of water tanks necessary?
- Waterproofing materials that should be used to protect water tank from leaking
- How to make waterproofing of concrete water tank properly – Guideline:
- Waterproofing technology
- The cost of waterproofing concrete tanks – Price per 1m2
Types of tanks
All tanks are divided into several main types, each type is designed to perform a specific function and task. The main types of tanks are as follows:
- Aboveground –located on the ground and have minimal contact with the ground. They can be both metal and concrete. The insulation of this type of tank is carried out mainly from the inside. The choice of waterproofing material depends on the liquid with which it is filled and its chemical properties.
- Underground – located underground and exposed to groundwater and underground aggressive environment. For underground tanks, it is necessary to provide waterproofing from the inside and outside.
- Firefighters – Designed to store process water to extinguish possible fires. Fire tanks and reservoirs are usually built underground near shopping malls and other significant facilities.
- Potable – These containers are designed to store drinking water. They can be both underground and installed above ground. To isolate them, it is necessary to choose materials that meet the standards and are suitable for contact with drinking water.
- Technical – Technical liquids of different chemical compositions or technical water are mainly stored in this type of containers. In most cases, they are located on the territory of various industries and factories. Technical tanks can be made of metal, concrete, or steel. It is recommended to choose a waterproofing material for such structures based on the technical characteristics of the liquid stored in it.
Depending on the type of tank, it can be made of the following materials:
- Concrete – concrete tanks for liquid storage
- Metal – metal or still containers
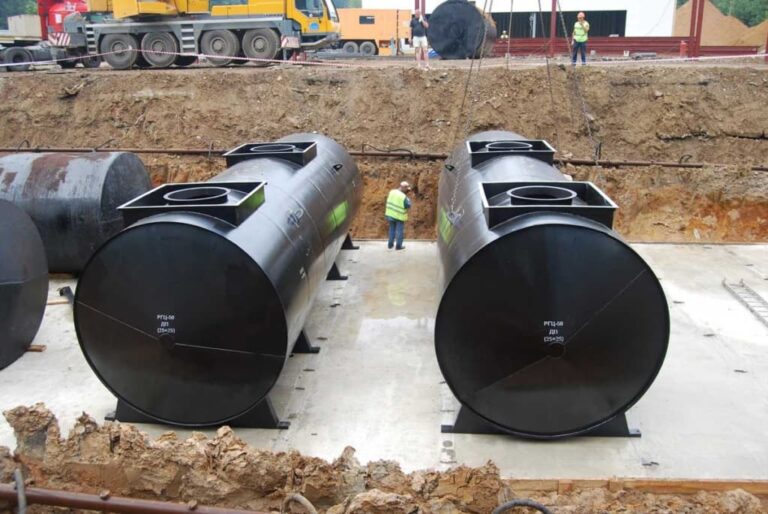
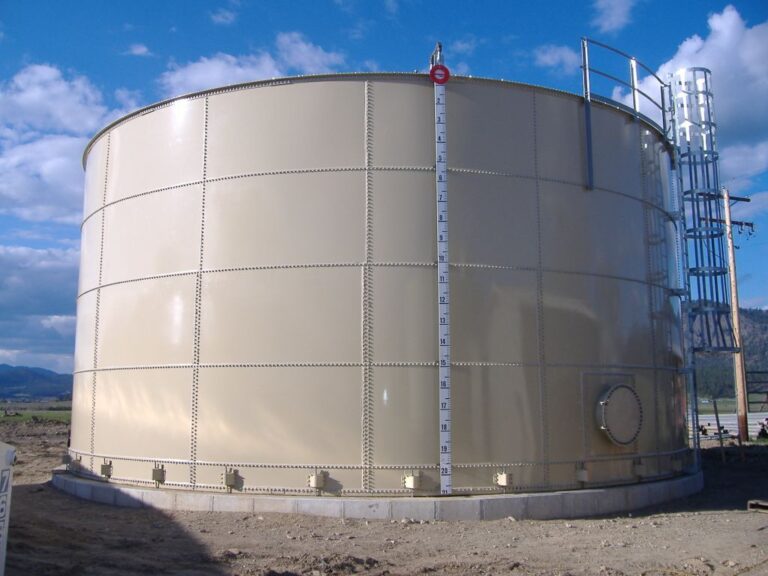
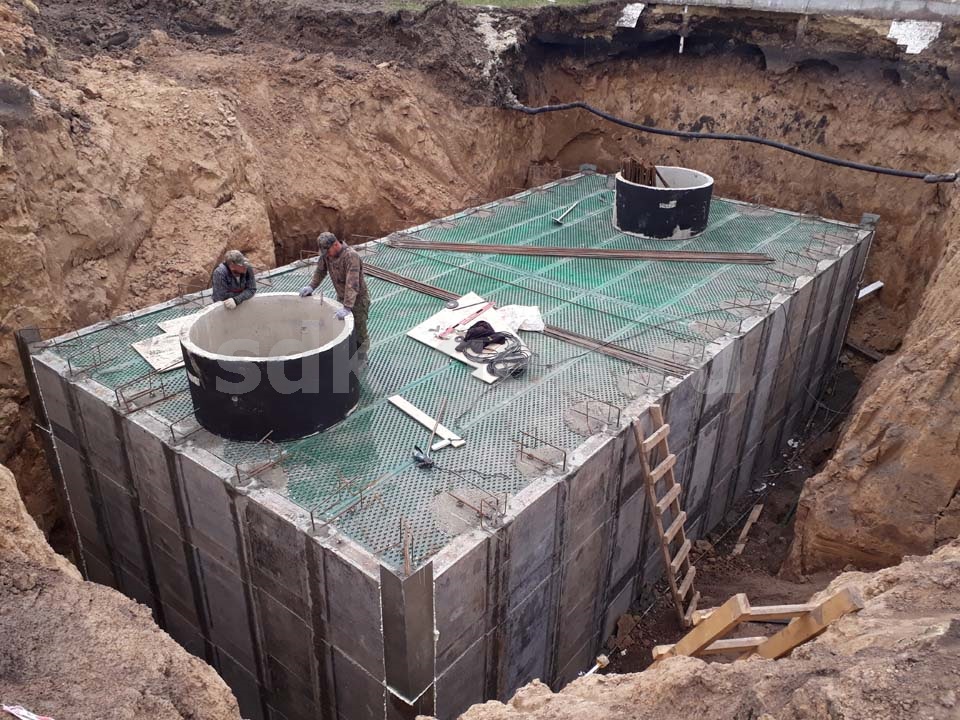
Why is waterproofing of water tanks necessary?
Waterproofing is necessary to protect the container from 2 things:
- Leakage of the liquid stored in it to the outside is relevant for underground and surface reservoirs. As a rule, a large amount of water or chemical liquid is stored in containers. This volume of water or chemicals presses on the walls of the tank and, in the absence of proper protection, can destroy the concrete base and leak out.
- Ingress of moisture or groundwater from the outside into the installed tank – relevant for underground tanks. Very often, after several months of operation, the concrete tank begins to leak due to the impact and pressure of groundwater. In the absence of good external waterproofing, moisture gets into the concrete, causes structural damage to the concrete, and destroys it. As a result, a crack may form in the tank, which will lead to leaks.
Waterproofing materials that should be used to protect water tank from leaking
One of the most important issues faced by builders during the construction of facilities such as reservoirs is their waterproofing. The requirements that must be met when installing a waterproofing coating vary depending on several factors:
- Purpose of the tank;
- The composition that will fill the container and its chemical properties;
- The material from which the tank is made – concrete, metal, steel, etc.…;
- Where the liquid container is located above or below ground.
Today, there are quite a large number of different materials for the insulation of concrete and steel tanks:
- PVC membranes – are mainly used for waterproofing tanks with drinking water. The main disadvantage of this material is the presence of seams (joints) and lack of adhesion (adhesion) to the surface.
- Polyurethane mastics – As a result of their application, a seamless coating with 100% adhesion to the base and a high coefficient of elasticity is obtained. They are used to protect the tank both from the outside and from the inside. These compositions can be applied by airless spraying or manually. There are different types of polyurethane compounds, including UV resistance and resistant to various chemical elements. These materials are perfect for waterproofing technical tanks.
- Bitumen mastics – They are applied both from the outside and from the inside. Most chemical elements do not withstand.
- Liquid rubber – Seamless coating with 100% adhesion to the base. Liquid rubber has a tensile coefficient of 600%, which allows it not to tear and crack by the shrinkage of the structure or its dynamics. This material is not suitable for protection against chemical liquids but is ideal for isolating an underground structure from the outside.
- Polymer-cement compositions – suitable for use both outside and inside the tank. Some of the polymer-cement materials, for example, HydroPaz from the German company HYDRO, withstand negative water pressure from the outside to the inside (in addition to positive pressure). This allows you to apply this material both from the inside and outside of the concrete container.
- Injection waterproofing – basically, we are talking about polyurethane resins of various viscosities. These resins are injected under pressure into the body of the concrete structure, filling potential voids and microcracks. This technology is used mainly when it is necessary to repair a concrete structure from the inside.
Important: for high-quality waterproofing of tanks, it is recommended to use seamless waterproofing coatings with 100% adhesion (adhesion) to the surface, according to the type of polyurethane compositions polyflex or analogues from Basf
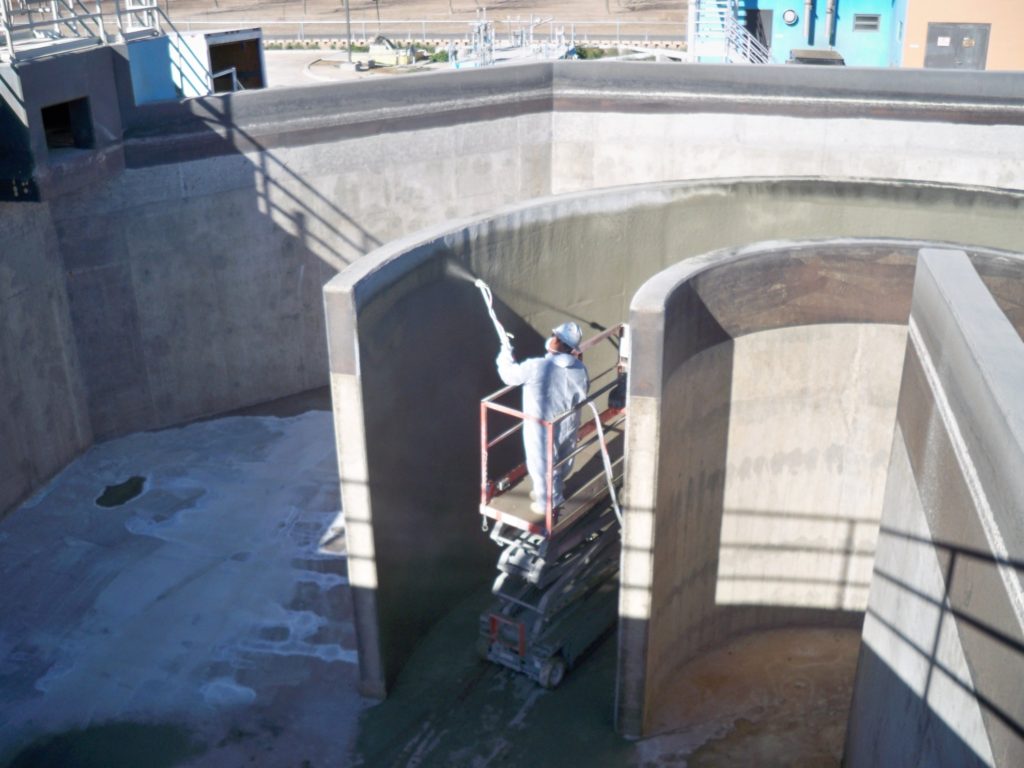
How to make waterproofing of concrete water tank properly – Guideline:
- Choose the right material – For reliable and durable waterproofing, the first step is to choose the right waterproofing and protective material. Its choice depends mainly on the purpose of the tank and on the composition from which it is made (concrete or metal). If the tank is designed to store chemical liquids, then the material with which you will perform waterproofing should have resistance to them, otherwise, it will simply collapse.
- Surface preparation – The most important thing when applying to waterproof is to properly prepare the surface. This work consists of the following measures:
- Thoroughly clean the surface of grease residues, degreasing agents, dust, loose components, etc…
- The base should be cleaned of flaking elements.
- All sharp and protruding elements should be removed.
- For concrete tanks in places where the floor intersects with vertical elements (walls, columns), a fillet should be made – a small plinth made of concrete or a special tape in order to remove 90-degree angles, since it is in such places that the waterproof coating can be broken in the first place.
3. Pay special attention to cold seams and places where communications are entered. These are the weakest points in the design. If during the construction of the tank, the technology of protecting the cold joints of concreting was violated, then you should strengthen these places before applying an insulating coating.
4. Apply the waterproofing material, observing all the norms and technology of its application. Please note that before applying certain materials, the surface must first be primed – apply a primer to it.
Waterproofing technology
The waterproofing technology depends on the type of tank and the selected material. Some materials are applied manually, and some by airless spraying. Injection resins are injected into the concrete bases using a special injection pump. Next, we will look at various technologies for protecting tanks from potential leaks, depending on their purpose and design:
Waterproofing of concrete underground reservoirs
In case when it comes to underground structures made of concrete, a waterproofing layer can be applied both from the outside of the underground structure during its construction and from the inside. For the external waterproofing of concrete, it is recommended to use the following components:
- Liquid rubber by the type of FLexLock of HYDRO factory;
- Mineral waterproofing;
- Surfaced waterproofing technolust of Technonikol factory;
- PVC Membranes of various types, of Sika factory or Icopal;
- Polyurethane waterproofing PolyFlex of HYDRO.
Waterproofing of concrete tanks from the inside:
When it comes to underground concrete tanks the following materials are used for internal waterproofing works:
- Mineral waterproofing HydroPaz – this system works both on the pressure and on the negative pressure of water from the outside to the inside. The uniform, seamless and waterproof coating is characterized by high strength and strong adhesion to the substrate, which ultimately allows it to withstand negative pressure.;
- Polyurethane materials of PolyFlex of HYDRO factory.
When repairing concrete from the inside:
- Injection systems, with the help of which special compositions are injected under pressure through packers into holes drilled in concrete, thereby filling voids, pores, and cracks in concrete and making it waterproof.
- Mineral waterproofing HydroPaz is also applied as a repair compound, where there is no possibility of external repair of the base, as it is able to work on negative water pressure.
- Expanding and non-shrinking sealants – Sealants, as a rule, are used for sealing seams and sealing pipe inlets and underground utilities are also used.
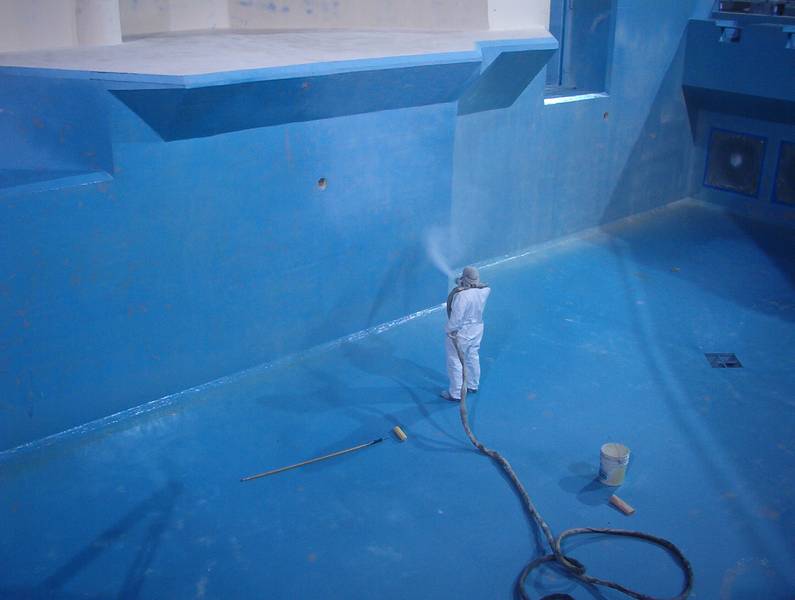
Waterproofing of concrete aboveground tanks
In the case of above-ground execution, the protective layer that should be applied to the concrete surface from the inside should have the following characteristics:
- Sufficient elasticity to withstand the expansion and compression of walls and floors, as they are exposed to temperature changes in the environment.
- High coefficient of water resistance.
An essential condition for successful protection against leaks is that the waterproofing coating applied to the base of the floor and walls of the tank must withstand severe hydrostatic pressure.
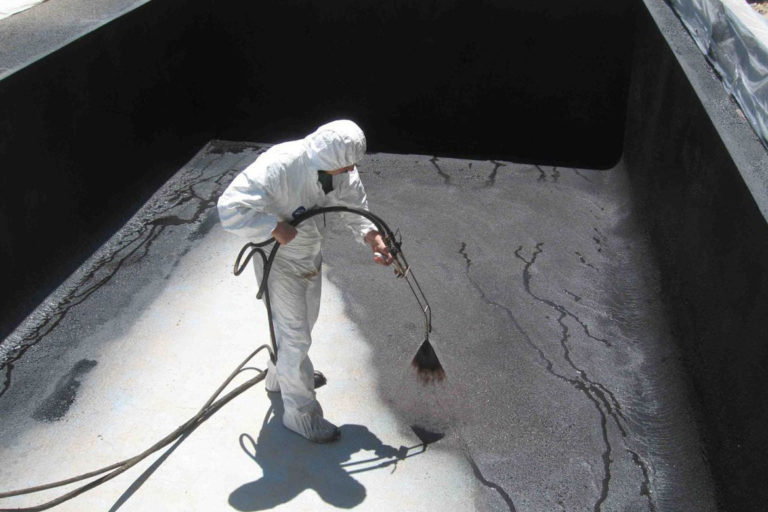
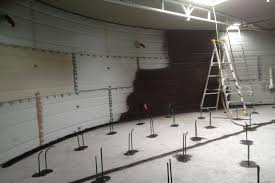
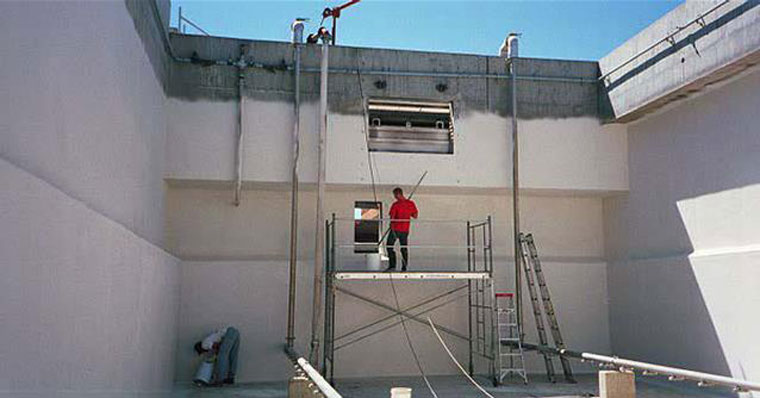
Waterproofing of fire tanks
Modern buildings require that the construction of an emergency fire system be located nearby since municipal supplies are not always available or coordinated. These fire containers usually have a concrete composition or are made of metal. Traditional methods of waterproofing fire tanks made of concrete, such as surfaced and membrane insulation, in most cases do not cope with the task.
One of the recommended methods of insulation and protection of underground fire tanks is Liquid rubber, for example, FlexLock (of HYDRO manufacturer). It is the liquid rubber that provides the fire structure with the necessary water resistance. Liquid rubber has no seams and has a tensile coefficient of 600%. This is a cost-effective and long-term solution for waterproofing underground structures and fire structures made of concrete.
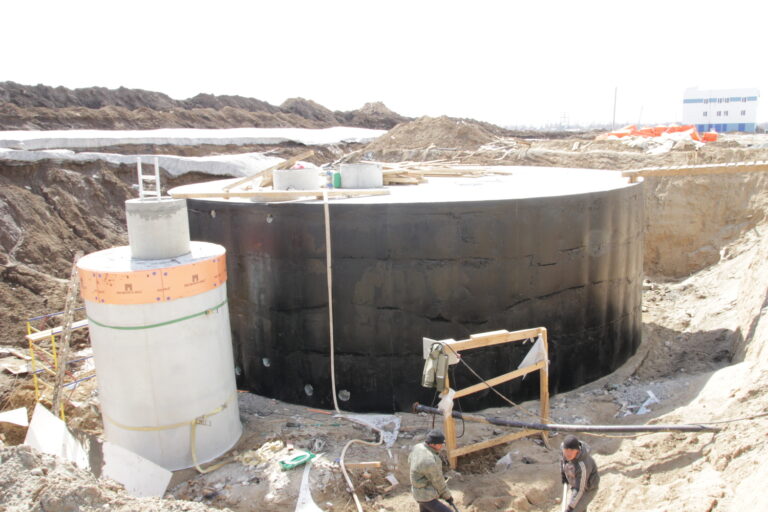
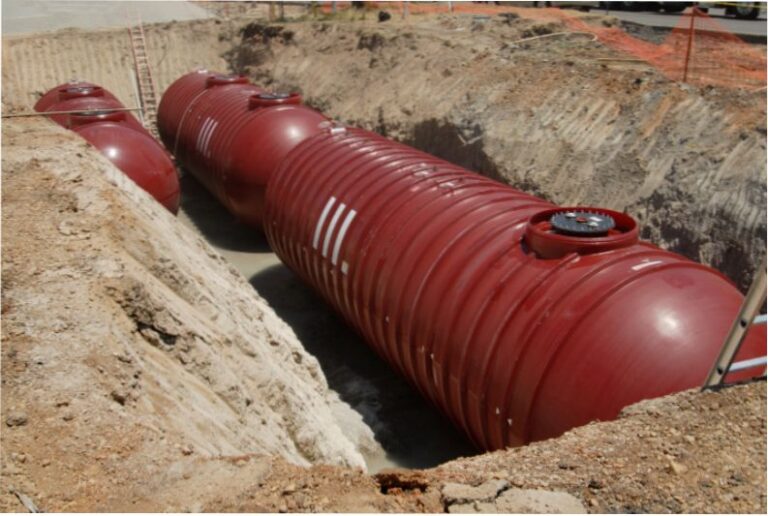
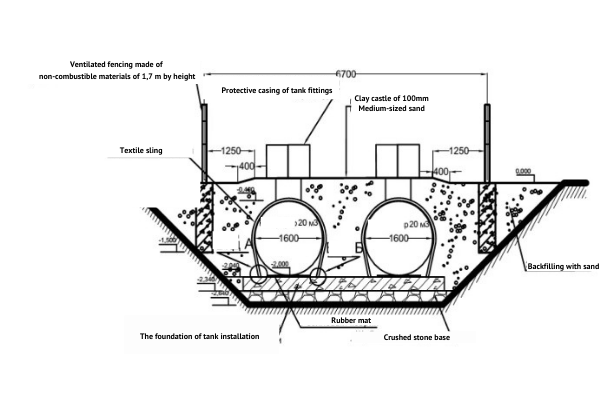
Waterproofing of water tanks
The insulation of drinking water storage tanks should not only have waterproof qualities for many years but also meet all sanitary requirements related to the storage of drinking water. The following waterproofing materials meet these requirements:
- PVC and TPO membrane – Hydro TPO Aqua is a homogeneous thermoplastic polyolefin waterproofing membrane for drinking water facilities. This membrane meets the hygienic requirements for the storage of drinking water in accordance with the German DVGW W 270 worksheet and the KTW manual. The membrane is mechanically attached to concrete, which greatly simplifies the preparation of the base for its installation.
The base for mounting this membrane should be as smooth as possible and free from sharp edges, depressions, and other defects that can mechanically damage the membrane. In the inner corners at the joints of the vertical and the horizon, it is necessary to make a fillet from the repair solution. For additional mechanical protection of the membrane, a geotextile mat (approx. 500 g / m2) is used, it can be installed on the bottom of the tank before installing the membrane. - Polyurethane waterproofing Polyflex (German manufacturer HYDRO) is also suitable for drinking water tanks.
- Polymer cement waterproofing is a seamless waterproofing coating based on cement, water, and various polymer additives. HydroPaz polymer-cement potions from the German manufacturer HYDRO, as well as similar potions from BASF, are suitable for contact with drinking water.
Waterproofing of steel and metal water tanks
Polyurethanes are ideal not only for concrete but also for all types of steel and metal tanks. Liquid polyurethane is non-toxic and environmentally friendly. It is suitable for drinking water stored in a steel, concrete, or metal tank. This component is a sprayable, elastic, and seamless membrane that repeats the shape of any base. Metal underground tanks must have high water resistance. Steel tanks play a vital role – they function as containers for drinking water, chemical waste, fuel, and other liquids. When it comes to preventing damage and maintaining the integrity of a steel or metal structure, waterproofing is essential. Polyurethane protects the steel surface from chemical influences. Its water resistance, excellent adhesion, and elasticity make it ideal for preventing damage to metal surfaces.
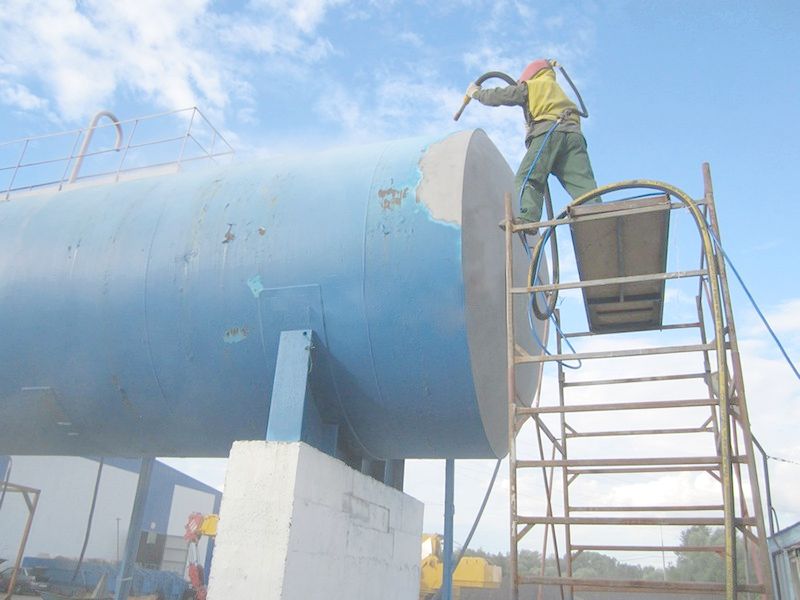
The cost of waterproofing concrete tanks – Price per 1m2
All the prices listed below are the average value of the cost per 1m2. To get an accurate price and a detailed estimate, you need to send us the detailed characteristics of your facility or call our engineer to inspect the facility and draw up a detailed technical specification for the performance of works related to insulation.
Prices for work outside:
Works description | Unit of measurement | Price in $ |
The arrangement of surfaced waterproofing on the horizon | m2 | 5 |
The arrangement of the surfaced waterproofing on the vertical | m2 | 7 |
Arrangement of a self-adhesive membrane on the horizon | m2 | 5 |
Arrangement of a self-adhesive membrane on the vertical | m2 | 7 |
Arrangement of PVC membrane on the horizon | m2 | 8 |
Arrangement of PVC membrane on the vertical | m2 | 10 |
Application of polyurea | m2 | 12 |
Application of mastic waterproofing | m2 | 3 |
Application of liquid rubber by spraying | m2 | 4 |
Application of liquid rubber manually | m2 | 8 |
Application of cement-mineral double-component waterproofing | m2 | 9 |
Arrangement of polyurethane waterproofing | m2 | 9 |
Application of penetrating compounds | m2 | 9 |
Applying the primer | m2 | 2 |
Prices for works from inside:
Works description | Unit of measurement | Price in $ |
Waterproofing of cold joints: -Works on the arrangement of indenting -cleaning the indenting -layer-by-layer sealing of non-shrinkable compositions | running meter | 8 |
Waterproofing of interlock joints: -cleaning the indenting -layer-by-layer sealing of non-shrinkable compositions | running meter | 6 |
Waterproofing of expansion joints: – Works on the arrangement of indenting – cleaning the indenting -elastic profile seal -sealing of non-shrink compound -complex works on injection | running meter | 70 |
Injection waterproofing of seams/cut-off waterproofing – Works on the arrangement of indenting – cleaning the indenting -layer-by-layer sealing of non-shrinkable compositions -Works on the installation of boreholes and packers -complex of works on injection -dismantling of packers and sealing of injection holes | running meter | 1200 |
Injection waterproofing in the concrete body -marking, works on the installation of boreholes and installation of packers – complex of works on injection – dismantling of packers and sealing of injection holes | m2 | 17 |
Injection waterproofing into the brick body -marking, works on the installation of holes and installation of packers – complex of works on injection – dismantling of packers and sealing of injection holes | m2 | 17 |
Cement-mineral waterproofing | m2 | 9 |
Penetrating waterproofing | m2 | 9 |
Waterproofing of communication entry points: -Work on the installation of the indenting -clearing the indenting -layer-by-layer sealing of non-shrinkable composition -Work on the installation of boreholes and installation of packers – complex of works on injection -dismantling of packers and sealing of injection holes | m2 | 98 |