Table of Contents
- The main advantages and disadvantages of liquid rubber waterproofing sealant
- Types of liquid rubber Waterproof Coating
- Liquid rubber waterproof sealant application technologies
- Waterproofing with liquid rubber sealant- Application step by step guidelines:
- Where is liquid rubber sealant used and on which surfaces can it be applied?
- Waterproofing of the foundation with liquid rubber waterproof sealant
- Waterproofing concrete foundation walls with liquid rubber sealant
- Waterproofing basements with liquid rubber waterproof sealant
- Waterproofing pond made of concrete with liquid rubber sealant
- Waterproofing roofs with liquid rubber waterproof sealant
- Waterproofing concrete floors with liquid rubber waterproof sealant
- Liquid rubber sealant for waterproofing: materials price and the cost of application per 1m2
- Waterproofing with liquid rubber sealent: application prices for 1m2 of spraying
- Comparison between the price of waterproofing by spraying liquid rubber waterproof sealant and other methods:
- Equipment for liquid rubber application by spraying
- Liquid Rubber waterproof sealant Manufacturers
- Consumer reviews
Liquid rubber is a product of bitumen processing. In fact, latex and other modifying additives, stabilizers, polymers, and water are added to bitumen. As a result, a single-component or double-component emulsion system is obtained, the properties of which allow it to be used for high-quality waterproofing. Liquid rubber can be both double-component and single-component.
When applying double-component liquid rubber, polymerization occurs with the help of the second component, namely calcium chloride. Polymerization occurs almost instantly since the two components meet on the surface at the moment of spraying the rubber and enter into an instant reaction.
The liquid component begins to harden immediately, but gains final strength within 24 hours, depending on weather conditions. Such protection is very resistant to temperature conditions from -45 to +50, respectively, rubber is suitable for waterproofing, objects located in different climates.
The main advantages and disadvantages of liquid rubber waterproofing sealant
Advantages of liquid rubber waterproofing sealant:
- No seams. After application, the resulting waterproofing membrane does not form seams, and seams are known to be weak points in any waterproofing system;
- 100% adhesion. Liquid rubber sealant has 100% adhesion (adhesion) to the base. And this means that the resulting coating will not have cavities and voids under it, where water can accumulate. In addition to the absence of voids, good adhesion guarantees that if a hole is formed in the waterproofing membrane, the liquid will accumulate exactly at the place of the hole, and will not spread under the coating to different places;
- Matches the form. When spraying with liquid propellant, the resulting membrane matches the shape of the base and its irregularities, which simplifies the work, and also removes the risk of leaks in the places of abutment. As you know, the abutments are one of the weak and responsible places in any waterproofing; The coefficient of stretching is 600%-800%. This coating has received a large coefficient of tension, which allows it not to tear and not to diverge, when the building or structure shrinks. This is well suited for dynamic nodes;
- The coefficient of stretching is 600%-800%. This coating has received a large coefficient of tension, which allows it not to tear and not to diverge, when the building or structure shrinks. This is well suited for dynamic nodes;
- Ecology. It is non-toxic and absolutely safe to apply, even in drinking water tanks.
- Safety. It can be applied by cold spraying, respectively, does not require permission for fire and other dangerous work;
- Speed of application. LC is applied by airless spraying, in a team of 2-3 people, on average up to 600 m2 per day, which allows you to cover a large volume in a very short time, as a result of which the cost of work is reduced;
- Warranty. Considering that this is a reliable and high-quality coating, most contractors using high-quality rubber give a 7-year warranty for their work;
- Price. The price of liquid rubber waterproofing sealant is lower than the price of other waterproofing compounds of the same quality.
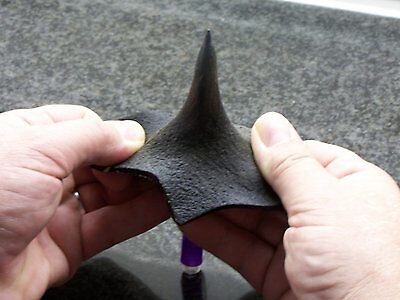
Disadvantages of liquid rubber waterproofing sealant:
- The complexity of application;
- When applied by spraying, there is a need for special equipment. This equipment is quite expensive and in order to use it requires experience and training;
- Liquid rubber is unstable to various solvents, respectively, it cannot be applied to various compositions based on solvents, for example, glue for insulation based on petroleum products or alcohol.
Comparison table between liquid rubber sealant and other materials
Liquid rubber | Surfaced bitumen-based membrane | PVC membrane | |
Mounting method | Reckless | Firing with a burner | With a hair dryer and mechanical attachment |
Availability of seams | Not available | Available | Available |
Adhesion to the base | 100% | 40% | No adhesion |
Coefficient of elasticity | 600-800% | 10-20% | 10-20% |
Installation speed m2/per day | 400-600 | 20-50 | 30-60 |
Warranty period for works | 7 years | 3-5 years | 1-2 years |
Characteristics of liquid rubber waterproofing sealant:
The following table shows the physical and mechanical properties of liquid rubber sealant:
Volumetric weight | 1100 kg/m3 |
Tensile strength at 0°С | 125 kg/m2 |
Ultimate strength after UV exposure for 3000 hours | 101 kg/m2 |
Tensile strength after immersion in water for 150 hours at a temperature of 45 degrees | 119 kg/m2 |
Conditional strength at the moment of rupture | 0,85 MPа |
Stretching in the air | 1680 % |
Stretching after immersion in water for 150 hours at a temperature of 45 degrees | 1400 % |
Flexibility at low temperature | – 28 °С |
Return to the starting position when stretching 1000 % | > 80 % |
Water absorption no more than in 24 hours by weight | 0,4 % |
Water resistance of the membrane of 3 mm | 0,23 MPа |
Volume loss after immersion for 150 hours at a temperature of 45 degrees | 4,7 % |
Heat resistance not less than | 85 °С |
Adhesion strength with the base | 0,79 MPа |
Average indicators of material consumption:
Thickness of membrane in mm | Consumption in kg/1m2 * |
2-4 | 4.9-5.5 |
5 | 6 |
6 | 8.5 |
*Consumption may vary depending on the manufacturer and brand of the material.
Types of liquid rubber Waterproof Coating
Single – component
Single-component liquid rubber is a waterproofing material consisting of bitumen, latex, and polymer additives. A distinctive feature of single-component formulations is that they are ready for use and do not require a second component for polymerization. Single-component liquid can be applied in one or more layers. Subsequent layers must be applied after the previous one has dried.
Double-component
Double-component liquid rubber requires a second component for its complete polymerization.
The second component is calcium chloride mixed with water in a certain proportion. 2-component compositions are applied mainly with the help of special equipment that simultaneously supplies both components under pressure. When meeting on the surface, the liquid forms a seamless elastic coating.
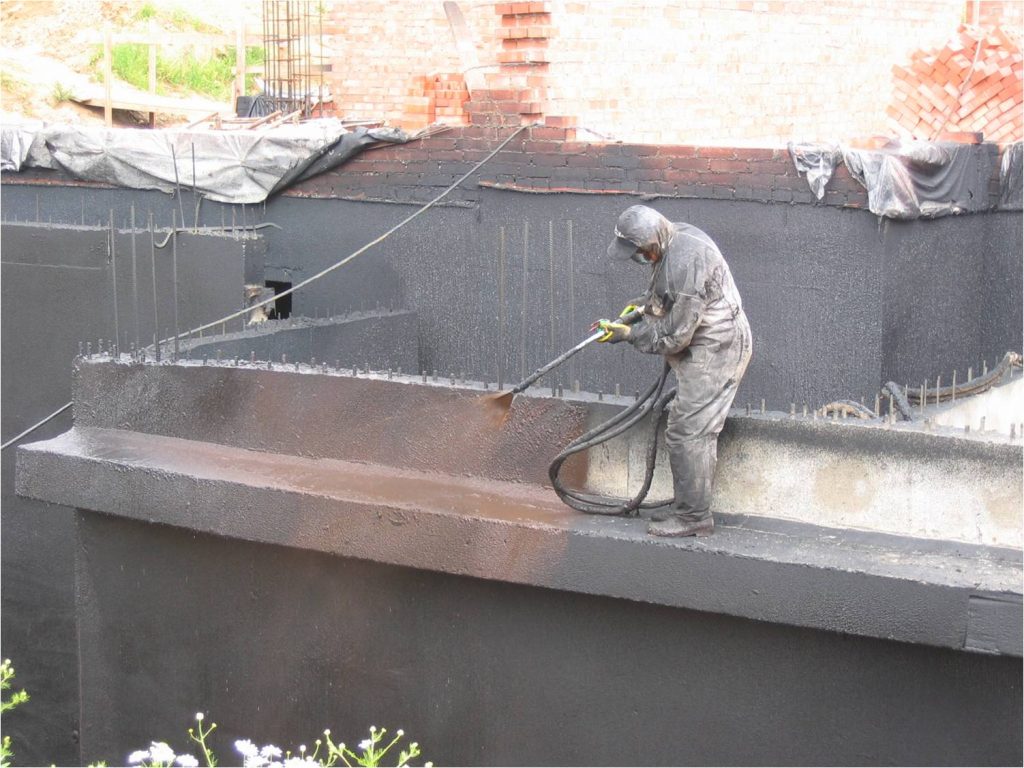
Liquid rubber waterproof sealant application technologies
Application by spraying
The spraying process takes place using a special airless spraying unit that maintains a special pressure and is equipped with 30-60 meter hoses. With the proper equipment, the material can be applied to a building up to 10 meters high, while the installation and barrels with liquid rubber remain at the bottom.
When it comes to double-component liquid rubber, the second component is also involved in the process, namely calcium chloride mixed with water. The proportion in which it is mixed depends on the container and the specific liquid rubber.
When spraying double-compound liquid rubber, a special nozzle is used, with two holes, so that the two components collide on the surface, and instant polymerization and hardening occur. It is ideal for applying to the foundations of private houses and administrative buildings, basement walls, and other concrete structures located below ground level.
The work on spraying double-component compositions is quite complex and requires training and experience both in working with the spraying plant itself and directly with the spraying itself. As a rule, a double-component insulating material is sprayed in 1 layer with a thickness of 2-4 mm.
Manual Application Guidelines For Liquid Rubber Sealant
Liquid rubber can be applied manually by specialists using a brush and roller. Single-component insulation, is mainly applied in 2-3 layers depending on the base – concrete, brick, block, or metal, as well as depending on the type of structure – basement, roof, terrace, balcony, roof, pond, foundation, walls, etc.
Waterproofing with liquid rubber sealant- Application step by step guidelines:
Works on spraying or applying liquid rubber sealant should take into account the following stages:
- Preparation of the base — cleaning the base from foreign materials, sharp bumps, and dust (this is one of the most important stages affecting all subsequent work).
- Primer application – works on applying the primer to the surface are carried out to improve the adhesion or adhesion of the material to the surface.
- If we are talking about single-component rubber: Apply the material to the surface, with the drying of each layer. If we are talking about double-component rubber, then several more stages are added here related to cold spraying with the help of special equipment: – preparation of equipment – spraying of double-component material – cleaning of equipment.
Important: When carrying out these works, it is very important to have knowledge and relevant experience, in a portable case, the material will not be applied according to technology and, accordingly, will not work as needed.
Where is liquid rubber sealant used and on which surfaces can it be applied?
Due to its properties, liquid rubber is a unique product and is suitable for the application and performance of waterproofing works on the following structures:
- Foundations;
- Foundation slabs;
- Walls;
- Floors;
- Roofs;
- Any concrete structures;
- Tanks, concrete ponds, and reservoirs;
- Basements;
- Tunnels.
The material is suitable for application on the following surfaces:
- Concrete;
- Brick;
- Metal;
- Bitumen and other coatings, for example, Technoelast membranes and other types of bitumen membranes;
- Expanded polystyrene.
Waterproofing of the foundation with liquid rubber waterproof sealant
Waterproofing of the foundation is recommended to be carried out with double or single-component rubber manually or by airless spraying, it does no matter whether it is a foundation plate or foundation walls. If you follow the rules of waterproofing of foundations and design standards regarding waterproofing of foundations, then first the LC is applied to the foundation slab, then the walls are erected leaving a small gap or the release of the slab.
After the foundation walls are erected, insulation is applied to them with the entrance to the plate forming a so-called hydraulic lock. Liquid rubber sealant is one of the most reliable solutions for moisture protection for the foundation of a building, since the liquid rubber has no seams, has 100% adhesion to the surface, and has a sufficiently large coefficient of tension, which allows it not to tear and not to diverge during shrinkage of the building or the foundation itself.
When applied to a concrete foundation, it is necessary to carefully prepare the foundation surface, namely, to clean it from dust, dirt, peeling foundation elements, and sharp corners.
Next, on the surface of the foundation, it is necessary to apply a special primer, suitable specifically for liquid rubber sealant. The primer will help to improve the adhesion between the rubber sealant and the foundation itself. After the primer on the foundation dries (from 1-4 hours, depending on weather conditions and temperature), the liquid itself is applied.
You can read more about the waterproofing of the foundation in the following articles:
- Installation of waterproofing foundation: Methods, materials, prices, and recommendations of specialists
- Horizontal waterproofing of the foundation: The technology of the installation and the materials necessary for this
- Waterproofing of the ribbon foundation: Technology and materials
- Waterproofing of foundation blocks and walls.
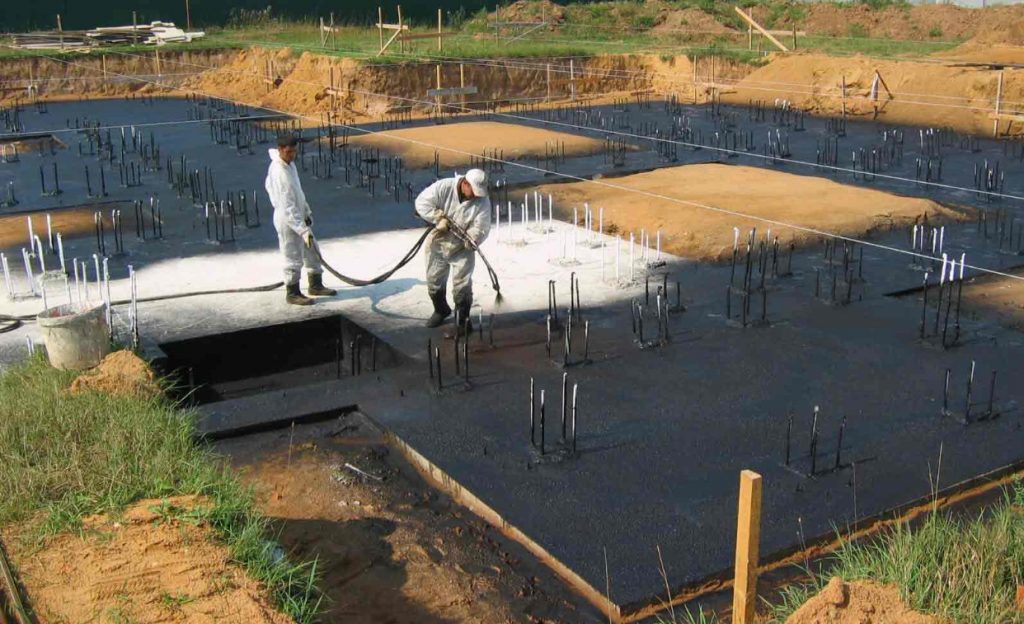
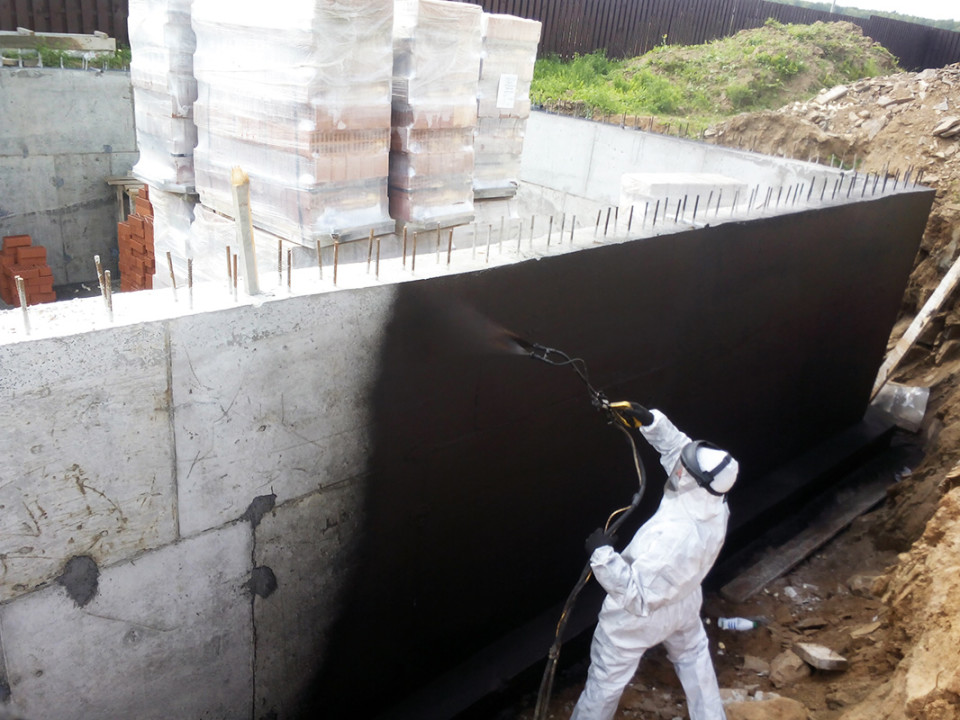
Waterproofing concrete foundation walls with liquid rubber sealant
As for foundations, and for walls, LC is one of the best and most reliable materials for waterproofing. It is applied to the walls using airless spraying, forming a homogeneous, seamless, waterproofing area with maximum adhesion and adhesion to the surface, which eliminates the ingress of moisture and water under it.
With shrinkage and dynamics, the material tends to stretch, not tear. Liquid rubber sealant can be applied to partitions made of concrete, bricks, blocks, aerated concrete, etc. with uneven blocks, alignment is not required, since rubber sealant will perfectly repeat the surface.
Considering the reliability and quality of such waterproofing, most contractors give at least 7 years of warranty when using this particular material for protection. When layering on the foundation walls, it is necessary to prepare the foundation in terms of its cleaning from dust and dirt, peeling elements, sharp stones, and bulges. Before applying, the surface should be primed with a special primer.
When applying liquid rubber, and in principle any other waterproofing material on the walls, it is very important to make a small skirting board at the junctions of the wall plate in order to cut corners at 90 degrees (the so-called fillet). After the liquid rubber has been applied to the walls of the building, you can immediately glue the insulation on it. It is necessary to use water-based glue, not alcohol-based. After installing the insulation on the walls, it is recommended to apply a spike-shaped membrane for additional protection and drainage.
You can read more about waterproofing the walls in the article – Waterproofing the walls of the basement and the house from the outside and from the inside.
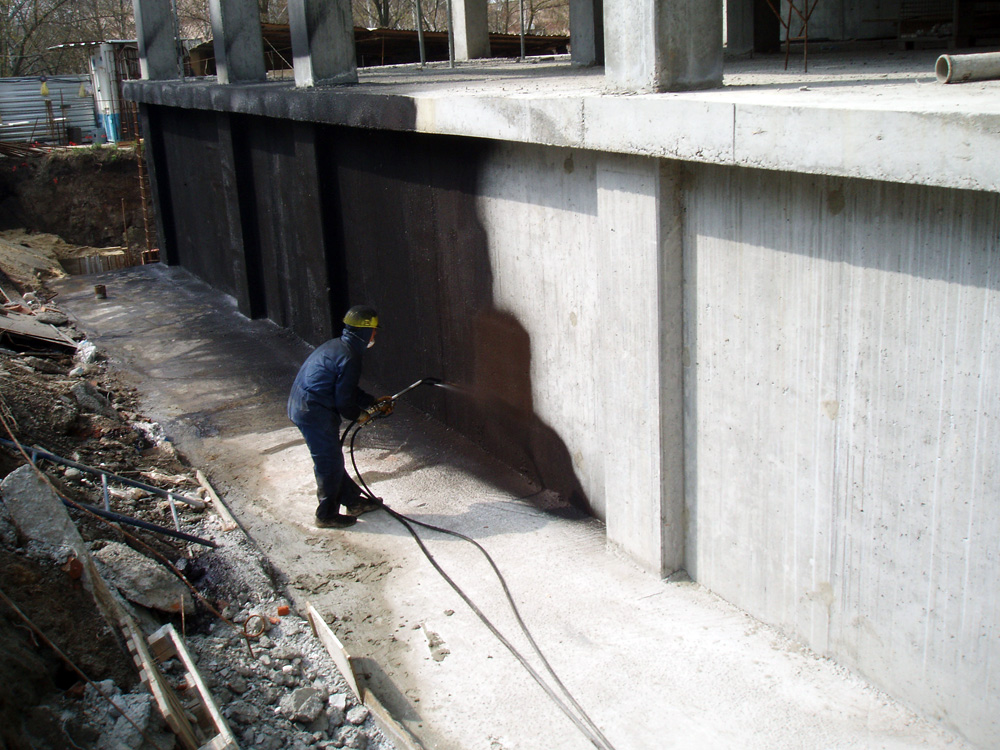
Waterproofing basements with liquid rubber waterproof sealant
The application of liquid rubber as a protective layer for basements is done mainly from the outside since this material fits perfectly on the base. This composition has 100% adhesion (adhesion) to the surface on which it is applied, which is very important for the high-quality and durable protection of basements from moisture and water penetration. The choice of liquid rubber sealant to protect the basement of a house or building from water is due to the obvious advantages of the material:
- Perfect adhesion — water will not walk under the applied coating;
- Lack of seams – it is through the seams that water begins to penetrate under the protective coating in the first place since these are the weakest places;
- The tensile coefficient of the material is 600-800%, it will not allow the material to disperse at the seams or crack during shrinkage of the building or future dynamics;
- Application speed – it is possible to cover from 400-800m2 per day, which is important with a compressed schedule of work.
You can read more about basement waterproofing in the following articles:
- Waterproofing of the basement from the inside: Methods, materials, and stages of work
- How to properly waterproof the basement from the outside
Waterproofing pond made of concrete with liquid rubber sealant
Ponds come in different shapes and for different purposes. The choice of a suitable waterproofing material also depends on the design of the pond and its final purpose. 2-compound liquid rubber, best suited for a concrete pond. The composition is sprayed onto the concrete part of a pond or reservoir and forms a single and seamless membrane. If we talk about non-concreted ponds, then it is best to use a butyl rubber membrane as waterproofing. For a concrete pond, it is also possible to use polyurethane waterproofing of the PolyFlex type or 2-component mineral waterproofing of the HydroPaz type.
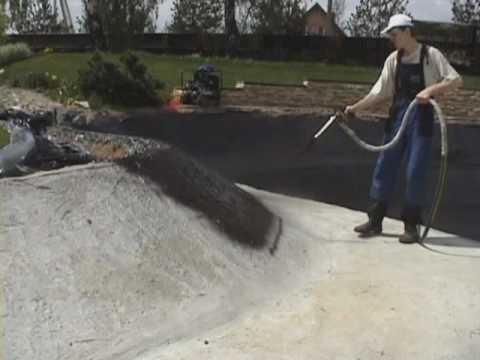
Waterproofing roofs with liquid rubber waterproof sealant
When layering on the roof, the double-component composition has maximum adhesion with concrete, metal, and any other coating, including old metal tiles. This property is mainly for those who, in order to save money, do not want to remove the old waterproofing of the roof or roof, but want to apply waterproofing on top of it.
Important: It is worth noting that if liquid rubber is applied on top of the old roofing, according to the type of surfaced membrane or PVC membrane, then in case of damage to the new waterproofing carpet, water can penetrate under the old waterproofing and continue to walk around the roof area under it, since the old waterproofing of the roof, unlike liquid rubber, has cavities and voids through which water can walk and pass. If you apply liquid rubber on a roofing plate or on any other rigid bases, then it will not have cavities inside, since it has 100% adhesion to the base and if it is damaged, water will accumulate only in one place, and will not go for a walk on the entire surface that is under it.
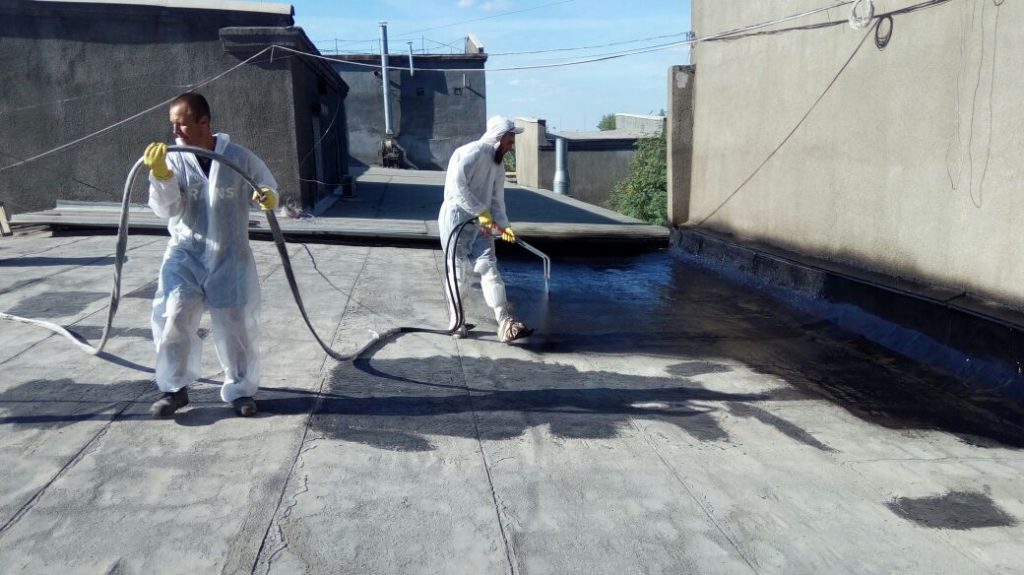
You can read more about roof waterproofing in the following articles:
- Waterproofing of the roof: methods of its construction and types of materials for performing high-quality work
- Roof waterproofing repair: Methods, materials, and prices
Waterproofing concrete floors with liquid rubber waterproof sealant
Waterproofing of the floor is mainly performed from the inside of the room. Waterproofing of the floor happens both in a private apartment in an apartment building, and in the basement of a country house or an administrative building.
If the amount of work on waterproofing the floor is small, it is recommended to perform work on protecting the floor with a one-component liquid rubber of the Flex-Lock Pro type or any other analog. Waterproofing of the floor is recommended to be done in 2-3 layers, with the drying of each of them.
Liquid rubber sealant for waterproofing: materials price and the cost of application per 1m2
The price of the material per 1 kg is $ | Consumption of 1м2 in kg per layer | Consumption of 1м2 in kg per layer* | |
Single-component rubber | 10-14 | 1-3 | 450-2400 |
Double-component rubber | 4-8 | 3-6 | 540-2340 |
* The consumption depends on the applied rubber and the construction.
The cost per 1kg varies, depending on its quality and manufacturer. The consumption per square meter is also different and depends on the manufacturer and the area on which it is sprayed or applied.
Since it takes more on an uneven platform with protrusions than on perfectly smooth concrete. Domestic compositions are cheaper than their foreign counterparts, but in most cases, their consumption is greater, respectively, the price and cost of 1 sq.m eventually increase.
It is also important to understand that the cheaper the composition, the worse is quality and the shorter the warranty period for the manufacturers of works. For example, double-component rubberv sealent differs from manufacturers in the quality of bitumen and the amount of latex added to it, which directly affects its qualities in terms of adhesion, tensile coefficient, and water resistance.
Latex is not produced in Russia and, accordingly, it is a rather expensive component that is supplied from abroad and the payment for it is in Euros
Accordingly, the lower the cost of liquid rubber waterproof sealent, the more likely it is that less of the same latex was added to it. If we talk about the high quality of liquid rubber and the balance between cost and the same quality, today one of the most high-quality and popular compositions among large construction companies is Flexlock liquid rubber from the German company HYDRO.
The only disadvantage of this composition is that the material is almost not available for free sale and it can only be found at authorized dealers and large construction organizations specializing in waterproofing. But, of course, this is not the only liquid rubber on the Russian market. There are quite a lot of manufacturers, you just need to choose the right one for your task.
When studying the cost of the material, it is also important to take into account the volume of purchased raw materials. The larger the volume that you are going to buy, the lower the price per 1kg and the cost of the batch as a whole will be. Prices try to reduce when buying a large volume.
Waterproofing with liquid rubber sealent: application prices for 1m2 of spraying
The cost and price of the work vary from 5 – 8 $ per 1 layer, depending on the chosen contractor, the complexity of the application, the scope of work, and the warranty period.
Comparison between the price of waterproofing by spraying liquid rubber waterproof sealant and other methods:
Works description | Unit of measurement | Price in US $ |
Works on the installation of surfaced waterproofing | m2 | 8 |
Works on the arrangement of PVC membrane | m2 | 9 |
Works on installation of polyurea | m2 | 15 |
Works on installation of the mastic waterproofing | m2 | 4 |
Works on installation of liquid rubber spraying | m2 | 5 |
Works on installation of liquid rubber manually | m2 | 7 |
Works on installation of cement-mineral double-component waterproofing | m2 | 9 |
Works on installation of polyurethane waterproofing | m2 | 9 |
Applying the primer | m2 | 2 |
Equipment for liquid rubber application by spraying
Special equipment is used for spraying liquid rubber. There are installations for airless spraying of liquid rubber running on electricity, and there is equipment running on gasoline. The advantage of a gasoline-powered installation is that it is perfect for carrying out work in places and construction sites where there is no electricity.
Liquid rubber equipment consists of the following main parts:
- Petrol or electric motor
- Pump for component A (gear)
- Pump for component B (vortex)
- High-pressure hose of 20-80m long
- A 2-channel sprayer (fishing rod) and sprayer nozzles (which form two flat identical torches of sprayed components).
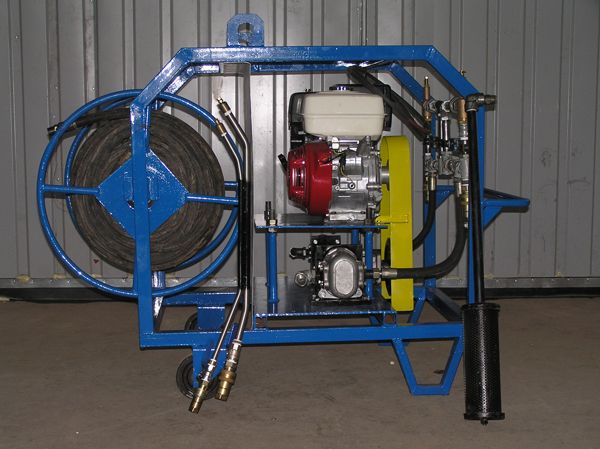
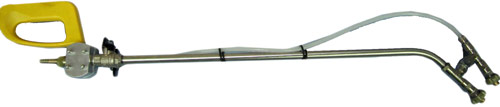
Liquid Rubber waterproof sealant Manufacturers
Foreign manufacturers:
- HYDRO – Liquid rubber brand FlexLock;
- SCHOMBURG – COMBIDIC-2K-CLASSIC brand liquid rubber;
- BASF – Insulation materials based on 2 components;
- KESTRAL – LR brand Mulseal DP;
Consumer reviews
Read reviews:
The following reviews were left by different people who have experience interacting with liquid rubber waterproof sealant:
♦ Noah – Engineer of Technostroy: Liquid rubber sealent was used as waterproofing of the foundation and walls of the business center building at our facility. After its drying, a seamless membrane of the rubber type was formed on the surface. When the technical supervision tried to tear off the insulation from the wall, excellent adhesion was revealed.
♦ Daniel – Private landlord: When repairing and replacing the old insulation of a private house, the contractor used liquid rubber sealent as insulation for the basement walls outside the house. The material proved to be a very high-quality waterproofing coating since 8 years later, not a single leak was detected in the basement of the house despite the high groundwater.
♦ Ethan is a private landlord: he redid the roll-on waterproofing of his basement 2 times. The first time 9 months after its installation, and the second time 2 years later. With each replacement, I had to dig out my foundation anew, dismantle the insulation and insulation, apply a new layer, and then bury everything back. These events cost me a lot of money, so for the 3rd time, I decided to approach the issue of waterproofing more seriously.
I read various reviews and chose one of the best materials – in this case, it was FlexLock liquid rubber waterproof sealant. I called a professional company for consultation, which confirmed the correctness of my choice and applied the selected material to me by spraying. As a result, this year it will be 7 years since everything is dry in my basement.