Table of Contents
- Advantages and disadvantages of sprayed waterproofing materials
- Varieties of sprayed waterproofing
- Where and in what areas “liquid rubber” is used
- The technology of spraying “liquid rubber” and the main sprayed materials
- The price of sprayed waterproofing
- The arrangement of sprayed waterproofing by spraying – recommendations
Sprayed waterproofing is a waterproof material designed for waterproofing various surfaces, such as foundations, walls, roofs, etc … The method of application of which is mainly spraying with special equipment.
Sprayed waterproofing materials are suitable for the application onto the foundation of:
- Concrete
- Brick
- Asbestos
- Felt
- Metal
- Bitumen
- Other bases.
Sprayed waterproofing is recommended to be applied onto:
- Foundations
- Foundation slabs
- Walls
- Roofs
- Concrete structures
- Swimming pools
- Reservoirs
- Flat and pitched roofs
- Other structures.
The main difference between sprayed waterproofing from other methods is that it is sprayed, which implies the possibility of applying the material to a large area in a short time.
Advantages and disadvantages of sprayed waterproofing materials
Advantages:
- Seamless. These membranes have no seams and joints, which increases their reliability, since seams are one of the weakest points in any waterproofing. Seamless waterproof membrane — provides complete insulation, which no other is capable of. This is because the sprayed insulation lies as a solid carpet without seams and without joints, which means no leaks because it creates a seamless monolithic film.
- Maximum adhesion. Good adhesion to the surface, thanks to which, under the protective layer on any surface, including the foundation and roof, cavities are not formed through which water walks under the surface;
- Application speed. This method of insulation is applied with the help of special equipment, a working unit of 2-4 people can perform waterproofing of an area of 400-800 m2 of roof or foundation per day.
- Being a fluid, waterproofing coating, it lies on any uneven surface, repeats its structure, and lies on those places where ordinary membranes do not show themselves well, for example, various irregularities. What makes this method of better insulation?
- No hot jobs. The application of such insulation is carried out by means of a cold application process, which eliminates the inconveniences and dangers associated with fire and hot methods used. This means that during the production of works, you do not need to obtain a permit for firework.
- Vapor permeability. This insulation allows vapors or moisture inside the building to escape easily outside.
- Strength. The strength of the resulting film and the high elasticity of most compositions can withstand the natural movements of the structure without the risk of ruptures or cracks.
- Easy maintenance. This method of isolation requires minimal routine maintenance.
Disadvantages:
- The complexity of installation. Sprayed insulation is very difficult to spray yourself, as this requires special equipment and skill. Accordingly, it is necessary to invite a specialized organization to spray the material.
- The complexity of application in narrow spaces. Liquid-sprayed insulation materials are sprayed under pressure through a special spray gun. For spraying, you need a distance from the surface of at least 0.5 m, respectively, if the distance between the ground and the wall of the basement or foundation is less, then the spraying method will not suit you.
Important: It is worth noting that today on the market, there are a large number of sprayed coatings and each of them has its advantages and disadvantages.
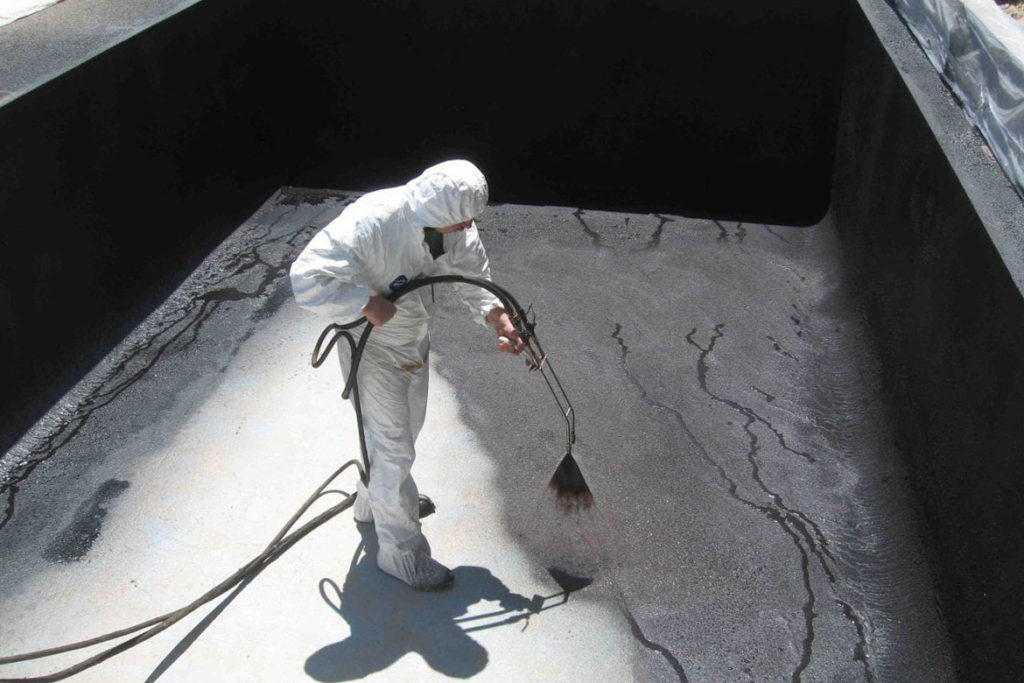

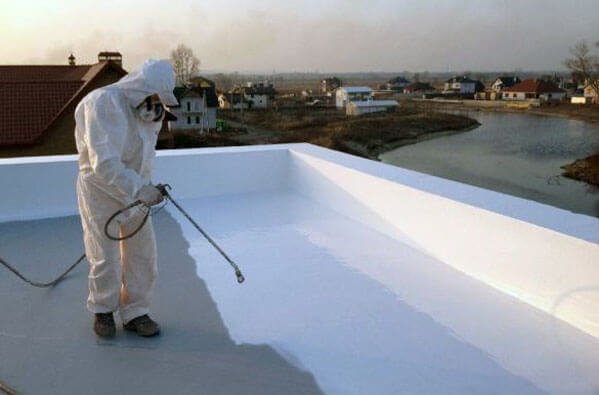
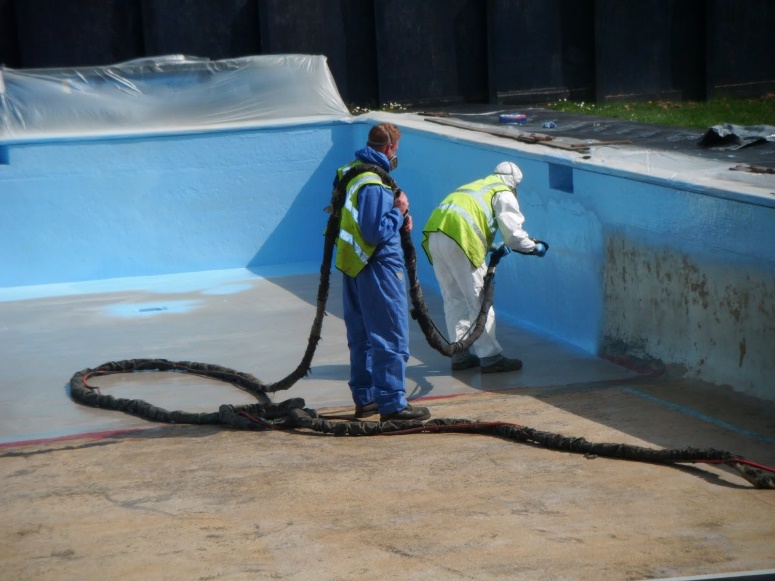
Varieties of sprayed waterproofing
Basically, sprayed compositions are available in three main categories: bitumen, polyurethane, and polyester.
- Modified bitumen.
Bitumen is modified using various substances such as natural rubber or latex, to make it more resistant, waterproof, and elastic. The most famous bitumen-based sprayed product is the so-called single or double-component liquid rubber by the type of FLexLock or Flexlock Pro. Double-component liquid rubber is sprayed by cold spraying using a special airless spraying unit. Such a coating can last from 25 to 40 years, depending on the quality. - Systems based on polyurethane.
Polyurethane waterproofing, they are applied by cold spraying and has a high class of fire safety. These products are also resistant to UV radiation and do not require additional protection when they are sprayed on the roof, balcony, or outdoor terrace. These roof covering systems are generally more stable when used in wet conditions and their service life can reach 25-45 years.
One of the most famous manufacturers of high-quality polyurethane waterproofing is the BASF concern and the German HYDRO Corporation with the PolyFlex product. Some polyurethane waterproofing coatings are also amenable to tinting and can be of various colors and shades, for example, blue for swimming pools or green for an operated terrace or roof. - Systems based on polyurea.
Waterproofing with polyurea – is a more modern and advanced system than the traditional systems used in waterproofing and protective coatings. However, this is not a new technology. In fact, it exists and has been in use for almost three decades. The technology is based on the reaction of an isocyanate component with a mixture of amines.
Isocyanate can be of aromatic or aliphatic composition. This reaction proceeds quickly and is completed within a few seconds, so special mixing and application equipment is required, which will be used by a specialized application team.
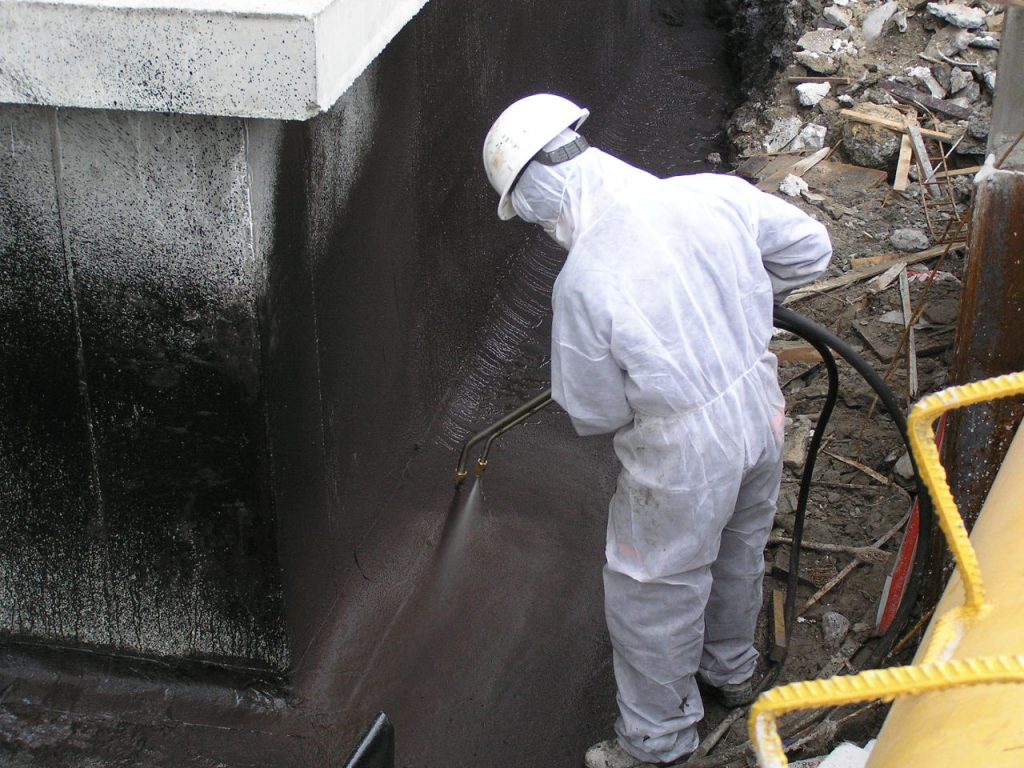
Where and in what areas “liquid rubber” is used
Liquid rubber is one of the most popular sprayed insulation materials. Due to its unique properties, this material can be used in various fields for insulation and protection of structures such as:
- Buildings foundations
- Basement wall
- Basement Outside
- Roofs of buildings
- Foundation slab
- Concrete and metal reservoirs
- Terraces
- Balconies
- Concrete reservoirs and ponds
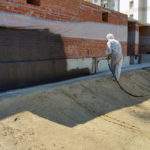
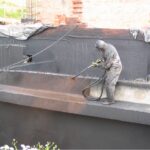
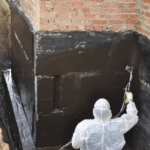
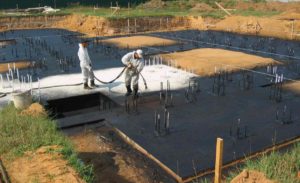
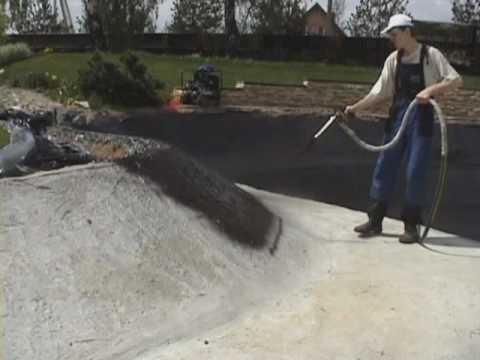
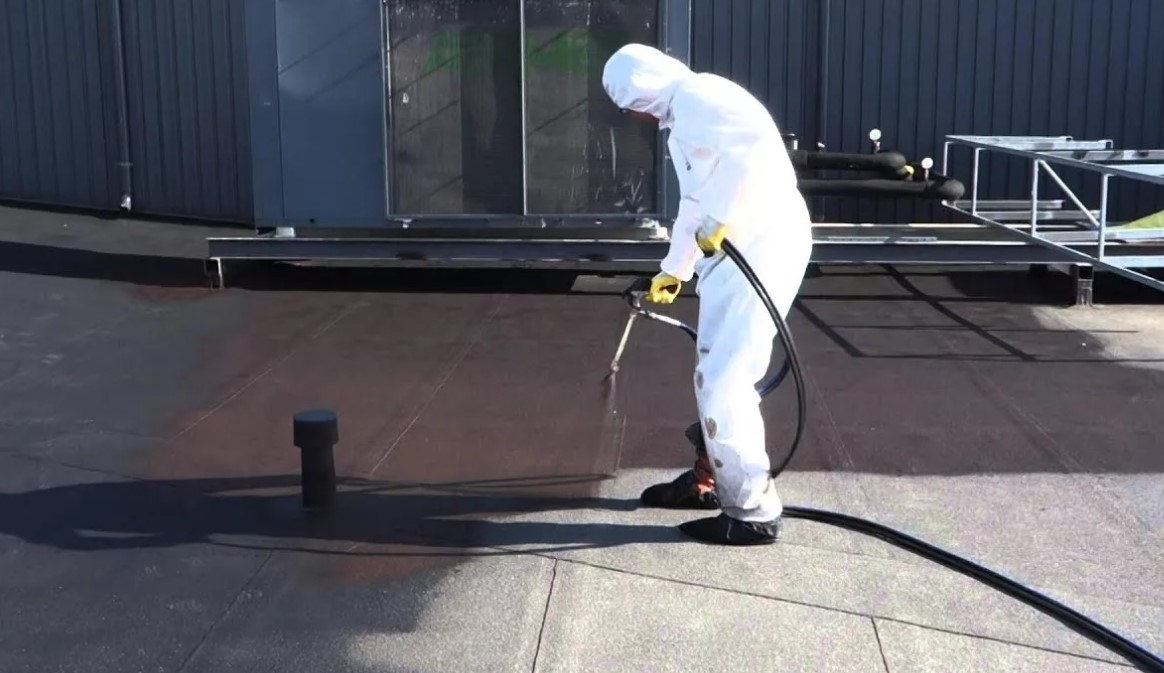
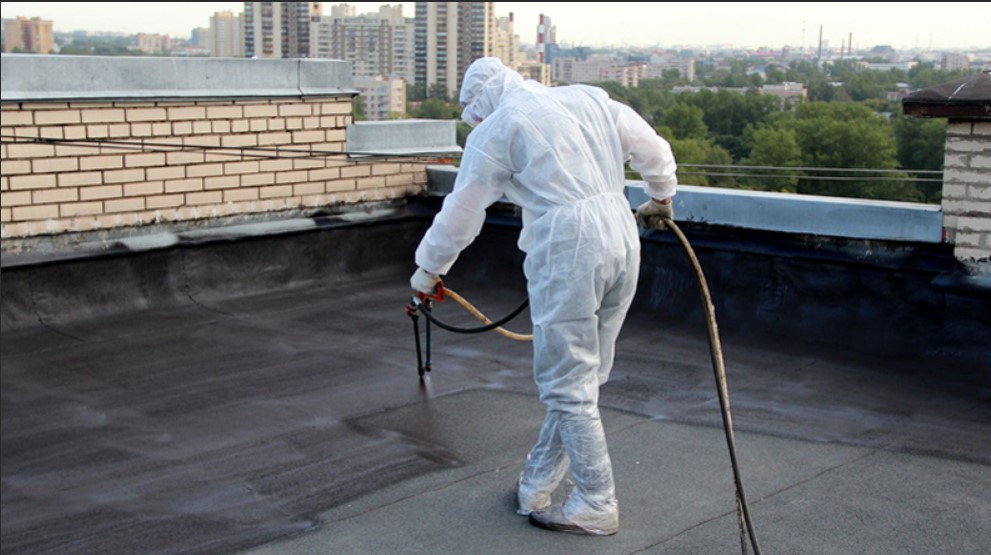
Liquid rubber is suitable for spraying on the following bases and surfaces:
- Concrete
- Brick
- FBS (Solid Concrete Blocks) blocks
- Metall
The technology of spraying “liquid rubber” and the main sprayed materials
Materials such as liquid rubber, polyurethane, and polymer-cement insulation are sprayed by the method of non-flash cold spraying. For these purposes, various equipment is used that feeds the material to the surface under pressure.
When spraying liquid materials, it is very important to observe the technology of work and surface preparation. To do this, follow the following recommendations:
1. Surface preparation – The base should be cleaned of dirt, dust, and peeling elements. If there are sharp bumps on the surface, they should be removed.
2. If during spraying there is a transition from the horizon to the vertical, then at the junction (plate wall) it is necessary to make a small skirting board (fillet) so that when the insulation passes from the horizon to the vertical there are no 90 degrees since such a transition will be a weak spot where the waterproofing coating may crack in the future.
3. Primer arrangement – Before applying most of the sprayed materials, the surface should first be primed with a special primer. The application of the primer improves the adhesion (adhesion) of the applied insulation to the surface.
4. Preparation of equipment – Before the waterproofing installation, it is necessary to prepare carefully the equipment for spraying. Check that the pumps are working and the hoses are not clogged.
5. Preparation of the material – If spraying involves two-component materials, then you should first mix the necessary components, following the manufacturer’s instructions (for each material has its own).
6. Compliance with the technology – When spraying, it is necessary to clearly follow the instructions of the manufacturer of the waterproofing compound. For example, when spraying liquid rubber, the spray application is made so that the two components are sprayed so as to meet on the surface. Polymerization of 2 components into a rubber membrane occurs at the time of their meeting.
7. Cleaning the equipment – After spraying, the installation should be cleaned, otherwise, it will clog and the next time it will malfunction. For example, the installation for spraying liquid rubber after use should be cleaned with gasoline or “White Spirit”, otherwise the remnants of rubber will thicken and clog the pump and hoses.
The price of sprayed waterproofing
The prices and cost of sprayed waterproofing vary depending on the selected waterproofing material, the manufacturer of this material, and the quality of the material. Since it is most likely that you will find the right balance between price and high-quality development. In addition, most foreign companies make their products according to international standards using high-quality foreign components. If you analyze the price of sprayed waterproofing for 1kg. of a manufacturer, then be sure to pay attention to its consumption per 1m2 and the number of necessary layers.
Sometimes there are situations where the price for 1kg is quite low compared to the prices for other materials, but it has a large consumption per m2, which, in fact, increases the cost of its spraying by 1m2. Sometimes such an increase, in the end, turns out to be more expensive than spraying a more expensive composition (whose consumption is 1 m2 lower).
Comparison of prices for different types of sprayed waterproofing:
The price of material per 1 m2 $ starts from | Works price per 1m2 in $ starts from | The total amount per 1 m2 in $ starts from | |
Double-component liquid rubber | 10 | 3 | 12 |
Polyurethane resin | 17 | 9 | 26 |
Polyurea | 26 | 11 | 12 |
To sum up, compared to prices, the optimal cost material will be sprayed 2-component liquid rubber. The most expensive material today is polyurea.
Comparison of prices per 1m2 between different types of liquid sprayed waterproofing and other types of coatings
Works description | Unit of measurement | Price in $ |
Works on the arrangement of surfaced waterproofing | m2 | 5 |
Works on the arrangement of PVC membrane | m2 | 8 |
Works on the arrangement of polyurea | m2 | 13 |
Works on the arrangement of mastic waterproofing | m2 | 3 |
Works on the arrangement of liquid rubber by spraying | m2 | 4 |
Works on the arrangement of liquid rubber manually | m2 | 5 |
Works on the arrangement of cement-mineral double-component waterproofing | m2 | 9 |
Works on the arrangement of polyurethane waterproofing | m2 | 9 |
The cost calculator of waterproofing works
Click to open the calculator and calculate the cost of works
Calculation of waterproofing cost
The total cost of waterproofing
The arrangement of sprayed waterproofing by spraying – recommendations
The sprayed coating is an ideal solution when you want to perform waterproofing of the roof, basement, balcony, terrace, reservoir, fountain, pool, etc … Most sprayed waterproofing systems are available in various shades, which makes them suitable for different constructs. With different designs, it is necessary to choose a different sprayed mixture, optimal in quality and cost. We conducted a survey among 50 construction companies engaged in waterproofing works and applying sprayed waterproofing, and identified the following recommendations for use:
- For waterproofing of concrete, brick, and other surfaces located below zero (underground), such as walls, foundations, basements outside, concrete tanks, etc., it is best to use a double-component sprayed liquid rubber of the FlexLock type.
- For waterproofing, small balconies, terraces, concrete tanks from the inside, swimming pools, fountains, etc., it is best to use polyurethane waterproofing.
- For waterproofing roofs and roofs over an old waterproofing membrane, it is best to use sprayed two-component liquid rubber.
Hello what kind of I step liquid rubber waterproofing do you recommend? Thanks
Hello, thank you for your question. When choosing waterproofing, it is necessary to take into account what exactly it should protect, for example, the roof, foundation, pool, etc., where it is applied (indoors or outdoors) and on which surface you will apply it (concrete, metal, brick). Regarding the recommendations, for example, Sika products are very well suited for waterproofing the roof, and BASF products and a Liquid rubber Sealant for the Foundation are suitable for foundations.