Table of Contents
- What is polyurea
- Types of polyurea and coatings, based on it
- Advantages and disadvantages of polyurea
- Characteristics of polyurea waterproofing
- Sphere of application of polyurea
- The technology of application polyurea
- Waterproofing with polyurea. Price
What is polyurea
Polyurea is a universal composition for waterproofing, and is successfully used for roofs, tanks, balconies, terraces, swimming pools and other concrete structures.
Polyurea was invented in the early 1980s, when a less moisture-sensitive form of polyurethane was required for waterproofing. By replacing the hydroxyl group in urethane with an amine group, a product was formed that we now call polyurea. It has significantly less sensitivity to moisture than other urethane-based coatings. This is one of the newest technologies in waterproofing. Developed in the late 1980s for the automotive industry, polyurea is currently used in a wide range of applications, including as waterproofing. The use of polyurea as an industrial waterproofing has increased dramatically in the last decade due to its special qualities and characteristics: The coating of polyurea dries quickly, is corrosion and wear-resistant, waterproof and can be quickly applied by spraying.
Types of polyurea and coatings, based on it
It is divided into three main types -aliphatic, aromatic and hybrid Polyurea:
- Aromatic
Of the two most common types of polyurea, the most common are aromatic, offering a wide range of physical characteristics for various waterproofing applications. In fact, the only characteristic that these polyurea coatings do not provide is resistance to ultraviolet radiation. - PM aliphatic polyurea
Aliphatic polyurea uses different chemistry to ensure stability and UV resistance. This additional advantage has its price since aliphatic polyurea is usually twice as expensive as aromatic polyureas. This kind or type of polyurea is mainly used for the application or spraying waterproofing on roofs, balconies, and terraces, since it is these constructs that are most susceptible to ultraviolet radiation. - Modified (hybrid) variants of polyurea
This type is formed when various additives are added to the original composition, according to the type: flame retardants, epoxy resins, plasticizers, and other additives that improve the performance of the coating. When adding the above additives, in addition to the waterproofing properties of the material, others are added to it, for example, UV resistance, high elasticity coefficient, etc.
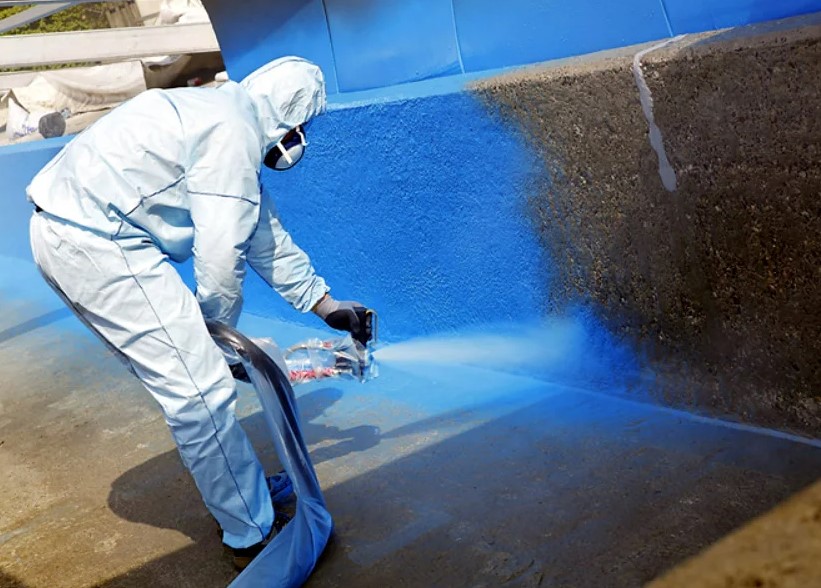
Advantages and disadvantages of polyurea
One of the reasons that polyurea coatings are rapidly gaining popularity is the wide variety of positive properties that they demonstrate. Industry experts say that, in fact, virtually no other coating can compare with this product when it comes to the achievable physical properties of the material. These formulations can be modified to achieve different properties, from high elasticity to excellent tensile strength. It all depends on how these compounds will be modified and how correctly applied.
Advantages:
- Adhesion – Polyurea has good adhesion and adhesion to a variety of substrates – concrete, metals, wood, and much more.
- Operating temperature – A wide range of operating temperatures and ambient humidity. The material works from -35 to +50.
- No seams – When applying the material to the surface, a single coating is formed without seams and joints.
- Fast polymerization – the adhesion of the material to the surface occurs almost instantly, allowing the applicator to create a ready-made coating thickness in one pass. With the help of spraying, it is possible to perform from 300-400 m2 of work in 1 day. This allows the owner to return the facility to operation many times faster than using traditional PVC membrane-type coatings, saving days or even weeks.
- Elasticity – With the necessary modification, the coating can be elastic.
- UV resistance – With the right modification and additives, the polyurea coating will be resistant to solar radiation.
- Resistance to mechanical damage – the material forms a sufficiently strong membrane.
- Coloration – Polyurea can be tinted in different shades and colors.
Disadvantages:
- High cost of raw materials – Polyurea is an expensive material compared to other compounds with similar characteristics, for example, polyurethane waterproofing.
- This coating is quite difficult to apply, which often leads to the fact that it turns out to be ineffective and quickly becomes unusable.
- Increased surface requirements. Sandblasting or priming the surface is crucial for the successful arrangement of polyurea. And this is additional expenditures on equipment. Most of the unsuccessful projects of applying waterproofing from polyurea have little to do with the mixture itself, but rather with inadequate or poorly implemented surface preparation.
- The equipment required for the arrangement of polyurea coatings is very expensive, its cost varies from $10,000 to $ 50,000 or more.
Characteristics of polyurea waterproofing
The thickness of the coating can vary from 2 to 5 mm in one layer. The curing time of the polyurea ranges from instant to two minutes, which allows you to get back quickly to work. Polyurea is a logical solution when seamless and durable membranes are needed for waterproofing.
Additional characteristics of polyurea, such as slip resistance, UV, and special surface textures, can also be included in the waterproofing material. The inherent flexibility of the composition is an additional advantage compared to thinner and less flexible coatings such as epoxy resin.
The following table shows detailed characteristics of polyurea:
Composition | Polyether polyamines, the aromatic polyurethane prepolymer |
The ratio of components 1 and 2 | 1 : 1 (volumetric) |
Content of non-volatile substances | 100% |
The density of the mixture of components (from +10 up to +35°С) | 1,05 kg/l |
The viscosity of 1st component (Brookfield. instrument plug 4, speed 750, Т=25°С) | 400 |
Viscosity of 2nd component (Brookfield. instrument plug. 4, speed 750, Т=25°С) | 630 |
Gelation time of the applied layer | 10 seconds |
Curing time of 100% adhesion | 50-70 seconds |
Curing time of coating (at +20°С) | Pedestrian loads -in 2 hours traffic loads – in 24 hours |
Operating temperature °С of heating components | +70–85°С |
Estimated consumption rates (by the thickness of the coating layer of 2,0 mm) | ~2,5 kg/м2 (including minimal natural losses during spraying). The actual consumption depends on the quality of preparation and properties of the protected surface (geometric characteristics, roughness, evenness, absence of pores, and other defects), the skill level of operators, proper working conditions, and adjustments of equipment (feed pumps and dispenser), the configuration of the “spray gun” (mixing chamber, tip, filters), as well as conditions on the work site (wind speed, air temperature, and protected surface). |
Polyurea in comparison with traditional waterproofing:
The following table compares polyurea with the traditional waterproofing membranes:
Polyurea | Rolled surfaced waterproofing on a bitumen basis | PVC membrane | |
Method of installation | Non-firing | Firing with a burner | With a hair drier and mechanical fixation |
Availability of seams | Not available | Available | Available |
Adhesion to the base | 100% | 40% | No adhesion |
Coefficient of elasticity | 600-800% | 10-20% | 10-20% |
Installation speed m2/per 1 day | 400-600 | 20-50 | 30-60 |
The warranty period for works | 7 years | 3-5 years | 1-2 years |
Sphere of application of polyurea
The technology for spraying polyurea as a waterproofing hole is successfully used in the following areas:
- Concrete roofs
- Metal roofs
- Terraces
- Balconies
- Water tanks
- Swimming pools
- Fire and technical tanks
- On pedestrian tunnels
- Underground parking
- Foundations of buildings
- Treatment facilities
The abrasive-resistant characteristics of polyurea make it an ideal composition for complex waterproofing projects. For example, it is ideal for waterproofing tanks at sewage treatment plants that are exposed to aggressive environments, turbulence, erosion, and large amounts of hydrogen sulfide gas, as their contents are sifted, mixed, and dehydrated. The polyurea coating provides the necessary resistance to abrasion, chemical, and shock effects, respectively, suitable for waterproofing and protecting bridges and other similar structures subject to vibrations and movement.
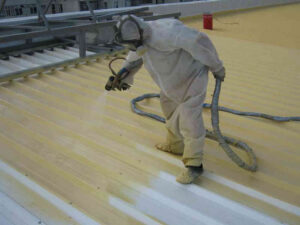
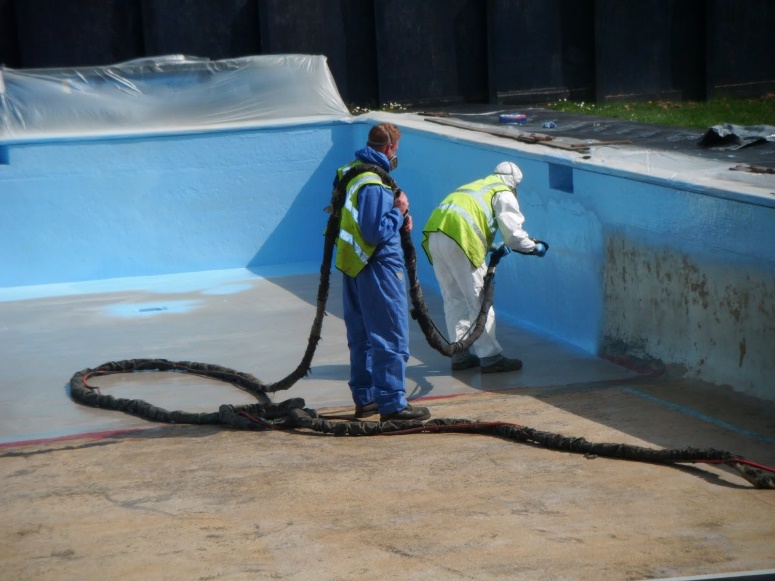
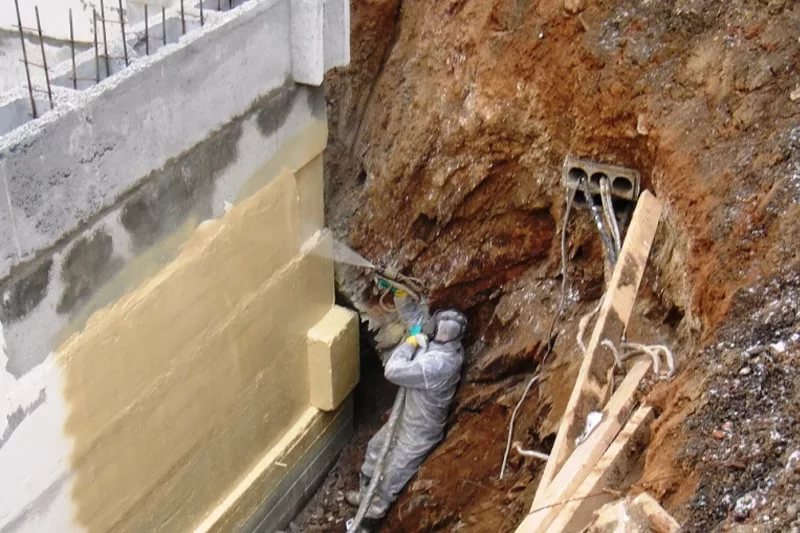
Waterproofing of the roof with a polyurea
One of the most popular applications is its spraying on various roofs, terraces, and open balconies exposed to ultraviolet rays. It is UV resistance that gives polyurea sufficient advantages when applied to the roof. However, do not forget that the price of the coating is quite high and, accordingly, not everyone is ready to apply this waterproofing compound to their roof.
Today, on the market for waterproofing materials, there are other sprayed compositions that are also UV-resistant, and have a good coefficient of elasticity, strength, and water resistance. For waterproofing the roof, for example, polyurethane materials are very well suited, according to the type of material PolyFlex from HYDRO, or similar material from the BASF concern.
Important: It is recommended to apply polyurea and polyurethane insulation to the base itself, and not to the existing bitumen or PVC membrane, since these membranes do not have 100% adhesion (adhesion) to the surface and if there is a hole in the new coating as a result of operation, water will penetrate under the old membrane and walk under it, coming out from the inside at the weakest point, which will not allow you to calculate the place where the hole was. When applying polyurea insulation to the bases, in case of a hole, for example, as a result of snow cleaning, water will accumulate in one place, which will simplify the repair process.
You can read more about the waterproofing of roofs in the following articles:
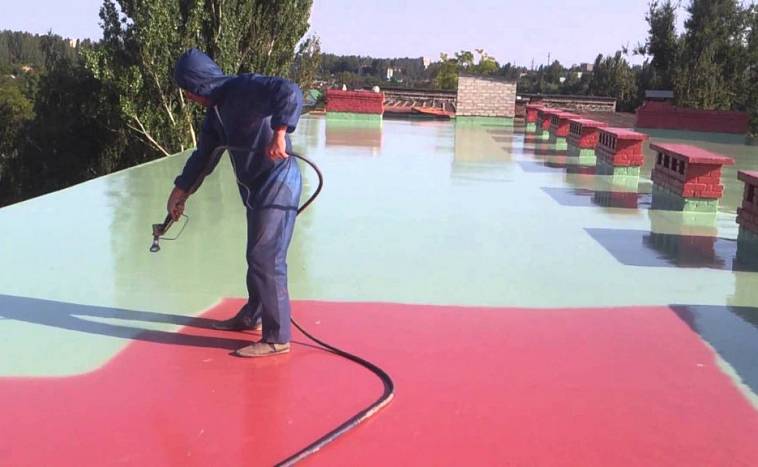
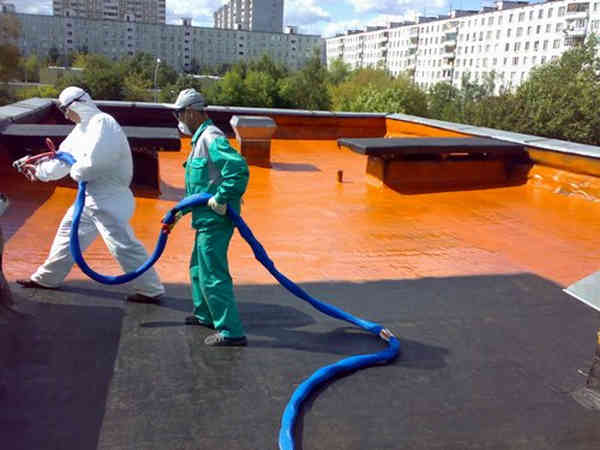
Waterproofing of foundation with polyurea
Polyurea can also be used for waterproofing the foundation. Since UV resistance is not required when performing foundation protection work, both single-component and double-component compositions can be used for these works. To apply insulation to the foundation, beforehand, it is first necessary to clean the surface from dust and dirt and to make a fillet at the transitions from the horizon to the vertical (to remove the weak point at 90 degrees at the junction). Polyurea is a fairly durable material, so it does not require additional protection from mechanical damage during filling.
You can read more about the waterproofing of the foundation and walls in the following articles:
- Installation of foundation waterproofing: Methods, materials, prices, and recommendations of specialists
- Horizontal waterproofing of the foundation: The technology of the installation and the materials necessary for this
- Vertical waterproofing: materials and methods of its installation
- Waterproofing of basement and house walls from outside and inside – Methods, materials, prices, and technology
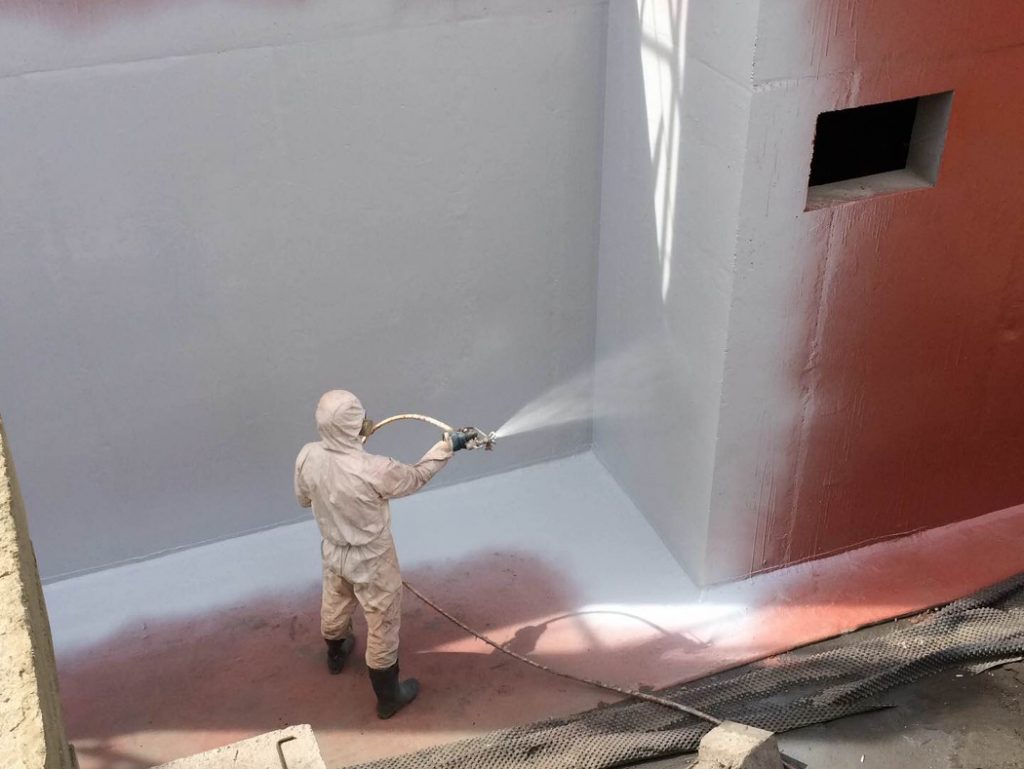
As a cheaper alternative for waterproofing of the foundation, while there is nothing worse for its waterproofing qualities, you can use:
The technology of application polyurea
Polyurea can be applied either manually or with the help of special equipment, depending on the material used, goals and objectives.
Applying polyurea manually
There is a polyurea that can be applied without the use of special installations. These compositions are applied with a brush or roller.
To apply manually, you need to follow the following technological processes:
1. To prepare the surface;
2. If necessary, apply a primer;
3. Mix the components in the correct proportion according to the manufacturer’s instructions;
4. Apply the material in 1 or several layers exactly following the manufacturer’s instructions.
Different brands of polyurea, are suitable for different methods of their application. Hand-applied materials are mainly suitable for local work, small balconies, and roofs in private homes where the amount of work is small. For industrial facilities and large volumes, spraying compositions are mainly used.
Spraying of polyurea
Most of the polyurea-based formulations need to be applied by spraying using spray installations for two components. The installation shows the exact dose of different components and mixes them. With the help of such a unit and a special gun with a self-cleaning function, the spraying process takes place under high pressure.
When spraying insulation with polyurea, the following techniques should be followed:
1. Prepare the surface – Remove dust and dirt, remove sharp corners, and level the base;
2. Preheat the necessary components – Preheat all components separately, which allows mixing to be carried out as efficiently as possible;
3. Mixing of components – this process takes place in a special chamber where certain conditions are met;
4. Preparation of the mixture – The pressure and temperature both inside the container and the supplied mixtures should be high, this is what makes it possible to spray the mixture qualitatively;
5. Spraying of mixed components to form a coating of the desired thickness.
You can learn more about the spraying process in the following video:
Equipment and machine for the installation of polyurea – how it works in detail:
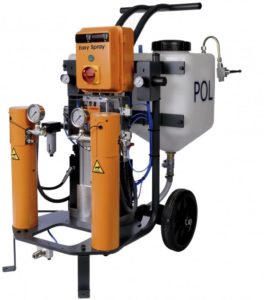
Most of the urea mixtures used for waterproofing are sprayed by using multi-component spray equipment. It is usually supplied as a double-component system, with a mixture of amine resin and isocyanate additive. The material is poured into 55-gallon drums in units. Further, during operation, it is transferred from 55-gallon drums to separate tanks of spray equipment, where it is heated to the appropriate temperature (140°F-160°F). The machine then feeds isocyanate and polyol resin through heated hoses to the spray gun in an exact ratio (usually 1:1).
It is easy to spoil the polyurea, since it has a set time, which is measured in seconds, so it is very important that the chemicals do not mix until they leave the gun. Otherwise, everything will get stuck and harden inside the gun. Some polyurea manufacturers sell mobile spray plants that include all the necessary tools and equipment installed either on a trailer or on the back of a truck.
Waterproofing with polyurea. Price
The price of such waterproofing depends on its type, modification, and manufacturer. Below are the average prices, and the average prices for the work on its application. The price for the process includes exactly the spraying of waterproofing on the surface.
The price of the material per 1m2 in $ starts from | Price of works per 1m2 in $ starts from | The total price per 1m2 in $ starts from | |
Sprayed polyurea | 31 | 12 | 44 |
Hand-applied polyurea | 27 | 10 | 38 |
When studying the price per 1m2, it is very important to pay attention to the consumption of the selected substance when it is sprayed or applied to 1m2 of the surface. It is important to note that the actual consumption may differ from that stated by the manufacturer if you do not have a perfectly flat surface. Waterproofing with polyurea will cover all the irregularities, but at the same time, the material consumption per 1 m2 will be increased.
Before monitoring prices, it is very important to determine the task that it should perform, since different mixtures are suitable for different tasks, the price of which may differ by more than 200%. For example, a modified UV-resistant polyurea will cost 2 times more expensive than a material that does not have similar properties.
Comparison of prices between the method of applying polyurea and other waterproofing methods
Works description | Unit of measurement | Price in $ |
Works on the installation of surfaced waterproofing | m2 | 5 |
Works on installation of PVC membrane | m2 | 8 |
Works on installation of polyurea | m2 | 12 |
Works on installation of mastic waterproofing | m2 | 3 |
Works on installation of liquid rubber mechanically | m2 | 3 |
Works on installation of liquid rubber manually | m2 | 5 |
Works on installation of cement-mineral double-component waterproofing | m2 | 9 |
Works on installation of polyurethane waterproofing | m2 | 9 |
Application of primer | m2 | 2 |