Table of Contents
- Why and when horizontal waterproofing is necessary
- Materials for horizontal waterproofing and their installation technology
- Arrangement technology of horizontal waterproofing by the type of foundation
- Rates for horizontal waterproofing with the prices per 1m2
- Recovery of horizontal waterproofing
Horizontal waterproofing is the protection that is applied to a horizontal surface. Horizontal protection of the foundation, walls, and other structures from penetration and exposure to water is very important, since without it your house or building may be exposed to water and moisture. The following article will tell in detail about what can happen if you carelessly approach the issue of horizontal waterproofing, how to do it correctly, and with what materials.
Why and when horizontal waterproofing is necessary
When it is necessary to do horizontal waterproofing?
The answer to this question is quite simple. If you follow the design standards and construction technology of almost any building or private house, then during the work it is necessary to make horizontal waterproofing of the foundation, and it does not matter whether it is a ribbon foundation or a slab one. The reason for this need lies in the fact that the foundation is in the ground, and it is made of concrete or concrete blocks of different types that absorb moisture located in the same soil. It is not only about groundwater carrying aggressive and harmful impurities for concrete, but also about the upper water, rainwater saturating the soil with moisture and water.
Why it is necessary to do horizontal waterproofing and what would happen if it is not done?
The absence of horizontal protection can lead to the following negative consequences:
- Destruction of the foundation of a concrete or block foundation when exposed to minerals and impurities in groundwater and rainwater – Groundwater and other waters carry various minerals and substances that can harm concrete and eventually destroy it.
- The formation of cracks and destruction in the structure of the concrete due to temperature differences – Water and moisture is absorbed into the concrete, freezing in winter and thawing in spring, which leads to the permanent destruction of any concrete substance. These damages form voids, pores, and microcracks in concrete, which can later turn from a micro-problem into a large crack and structural disturbance.
- Leaks and flooding – microcracks in the foundation formed as a result of freezing of moisture and temperature changes (or other influences), over time, begin to pass water through, which penetrates into the built house and leads to unpleasant consequences, such as increased humidity, mold, fungus or flooding.
- Capillary rise of moisture – in the absence of horizontal insulation of a strip or slab foundation, moisture that is absorbed into the concrete can freely, capillary rise from the foundation up the walls, forming leaks, wet spots and increased humidity of the walls inside the room, which in turn can lead to damage to finishing elements (paint, plaster walls), the formation of mold and fungus dangerous to human health in the room.
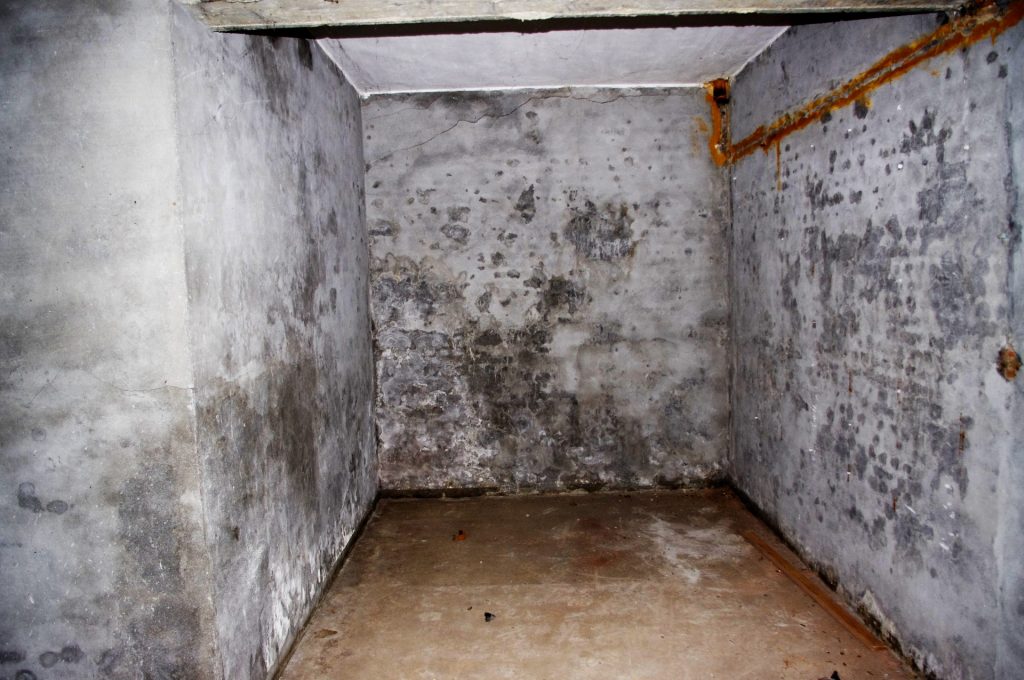

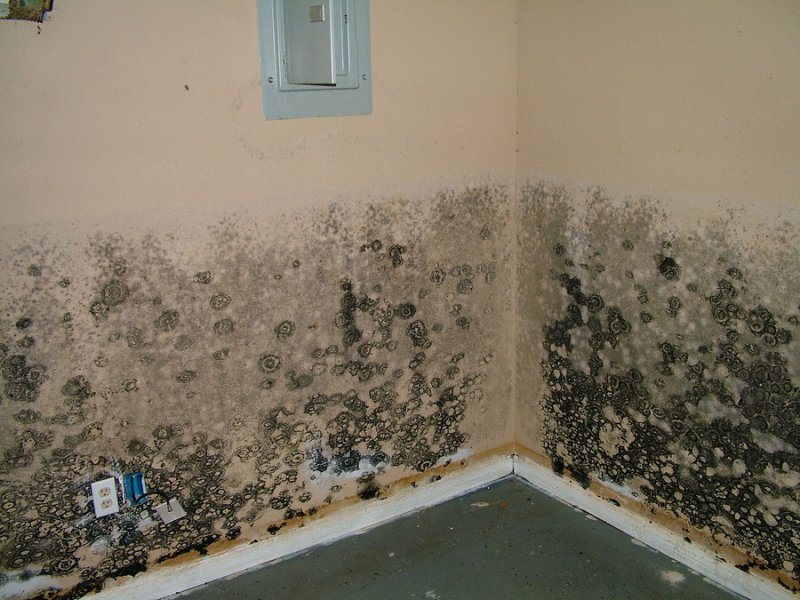
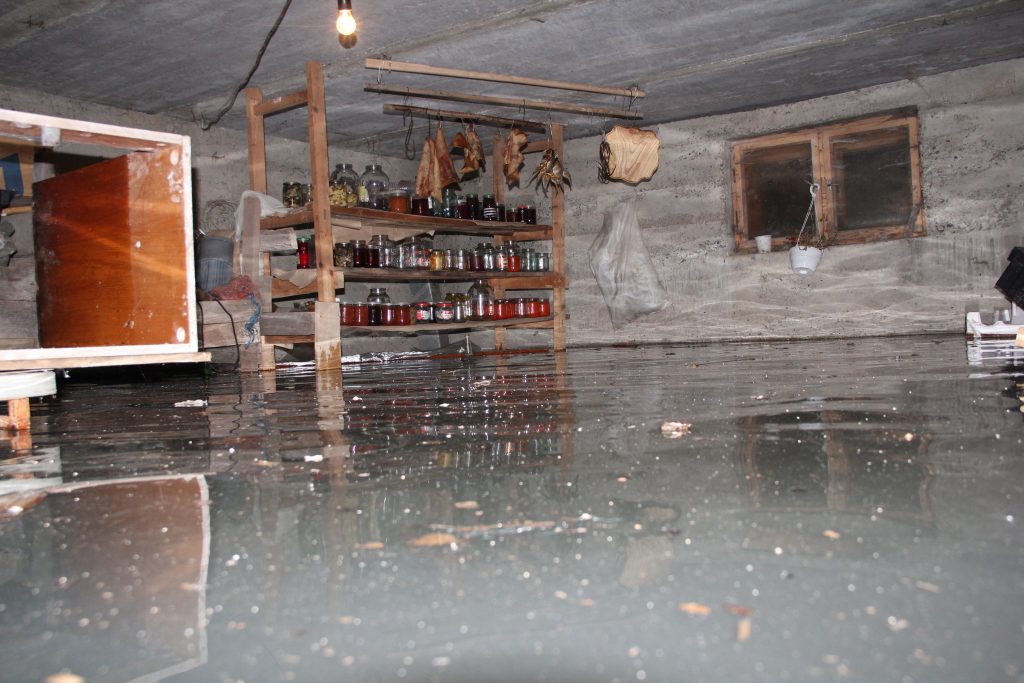
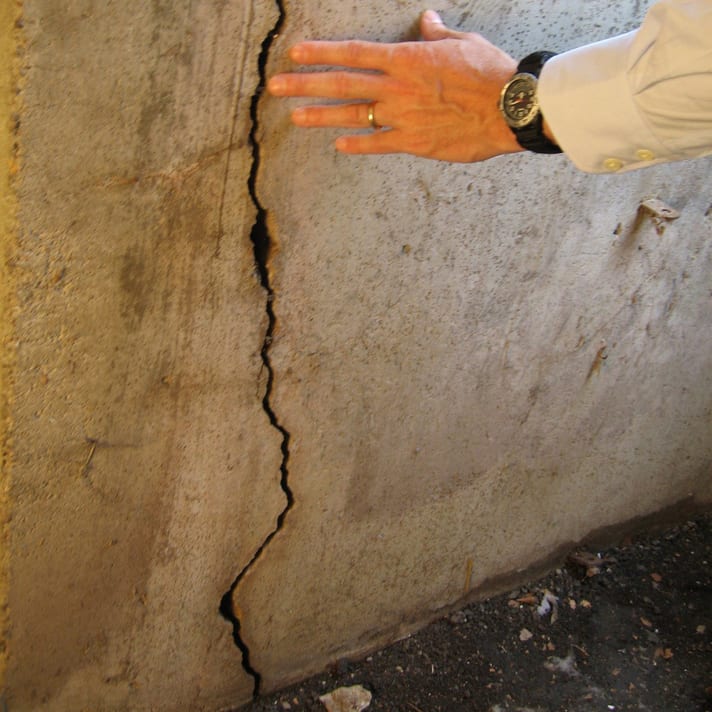
Materials for horizontal waterproofing and their installation technology
The horizontal cut-off can be made of different materials with different characteristics and methods of installation. The choice of the right material depends on the type of structure and the material from which it is made.
Roll pasting waterproofing
The pasting waterproofing is made mainly of bitumen-polymer materials. There are pasting rolls based on fiberglass impregnated with a bitumen-polymer binder, and protected on both sides by polypropylene material, and there is a self-adhesive baseless material, is obtained by applying a self-adhesive bitumen-polymer binder to an anti-adhesive film, followed by closing the binder on the front side with a polymer film.
The pasting waterproofing is supplied in rolls of various sizes and colors. The pasting sheets are designed for the installation of cut-off waterproofing, as well as for the protection of foundations, walls, floors, and basements from the inside and outside.

Advantages of pasting waterproofing:
- Easy installation which does not require special equipment;
- Long service life;
- Fireless works.
The technology of installation of self-adhesive pasting materials on the horizon:
- It is necessary to clean the base from dust and dirt;
- To prime the bases with bitumen primer;
- To open the self-adhesive roll from top to bottom;
- To stick the rolls on a horizontal or vertical surface, pressing against the base. When installing vertical waterproofing, it is necessary to fix the upper edge of the sheet with a metal edge rail.
Detailed instructions for the installation of pasting waterproofing on a horizontal base can be downloaded by clicking on the link: Installation instruction on pasting waterproofing
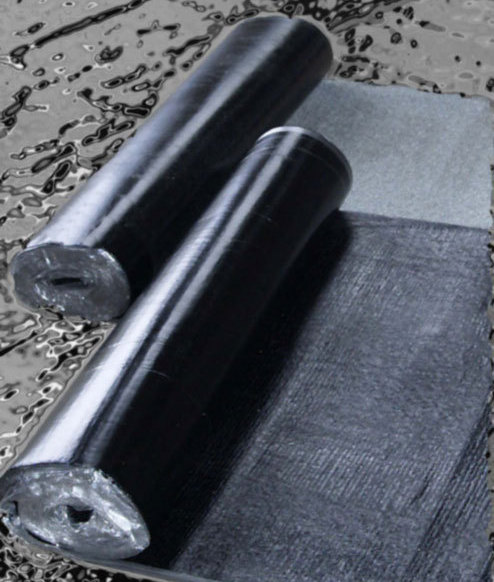
Rolled surfaced waterproofing
Rolled surfaced sheets are obtained by double-sided application of a bitumen binder consisting of bitumen, filler, and various additives to a fiberglass or polyester base. The bitumen layers above and below are protected by an easily combustible plastic film. The surfaced rolls are supplied in various sizes and are intended for the installation of works related to waterproofing of foundations, roofs, walls, and other structures.
Advantages:
- Durability;
- Can withstand relatively heavy loads;
- Good heat resistance;
- Frost resistance;
- Non-toxic.
Installation technology:
- Surface preparation;
- Priming the surface with a bitumen primer;
- Deposition of rolls using a burner.
Detailed instructions for the surfaced waterproofing arrangement can be downloaded by clicking on the link: Installation instructions for a waterproofing membrane made of bitumen-polymer rolled materials
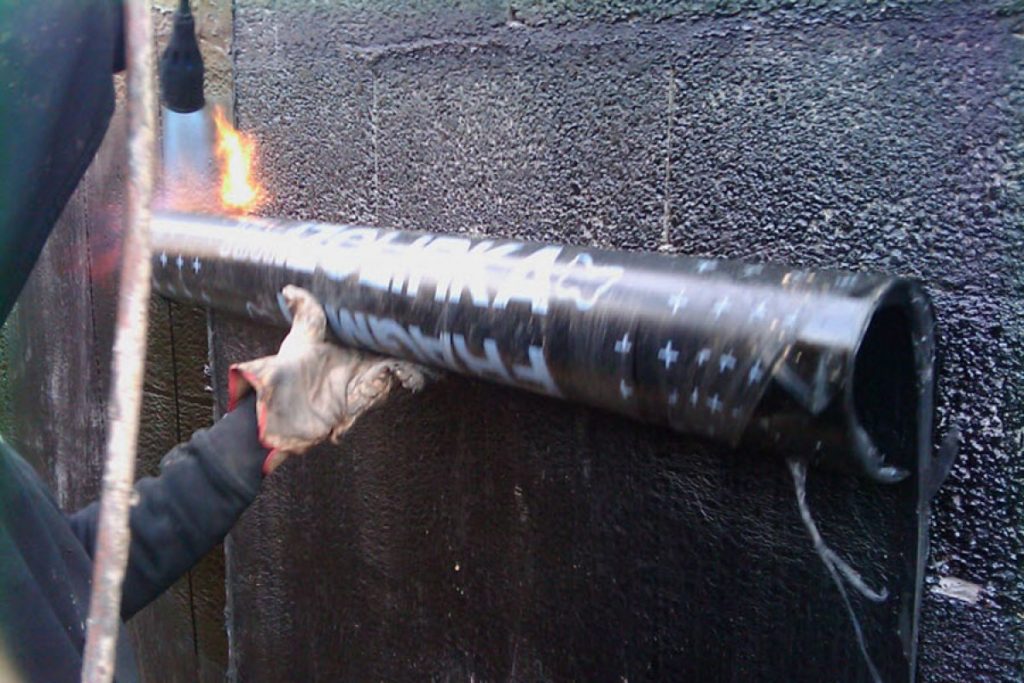
Penetrating waterproofing
Penetrating compositions are made of special cement, fractionated aggregates, organic additives, and chemically active substances. Penetrating materials are known for the fact that they can crystallize in the pores of treated concrete. Due to their unique properties, penetrating substances are able to stop the passage of water through concrete structures, as they form hard-to-dissolve crystals in filled capillaries and pores at the treatment site.
Advantages:
- Environmentally safe;
- Complies with the valid hygiene standards on the territory of the Russian Federation.
Installation technology:
- The treated surface should be moistened abundantly;
- Apply the penetrating composition with a brush or roller;
- Moisten the area where the material was applied abundantly every 10-16 hours for 4-6 days.
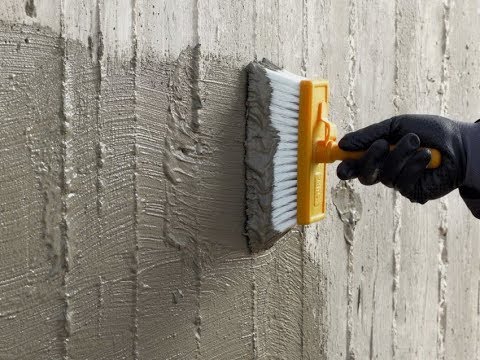
Working scheme of penetrating compounds in the structure of concrete:
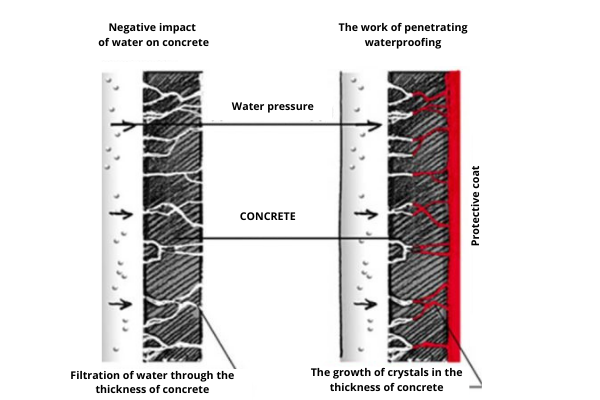
Injection waterproofing
Injection waterproofing implies the use of various epoxy resins and helium compounds for insertion into the body of the structure or its cold seams. Injection formulations differ in varying degrees of viscosity, flexibility, and behavior of the material in contact with water.
Choosing the right injection formulation in accordance with the specific requirements of the project is the first key success factor and can significantly affect the effectiveness of the work performed.
Self-injection is a procedure for injecting cement, polyurethane, epoxy, or acrylate material into damaged or cracked structures for reliable sealing, elimination of leaks, repair of damaged structures, and restoration of their waterproofness for a long time.
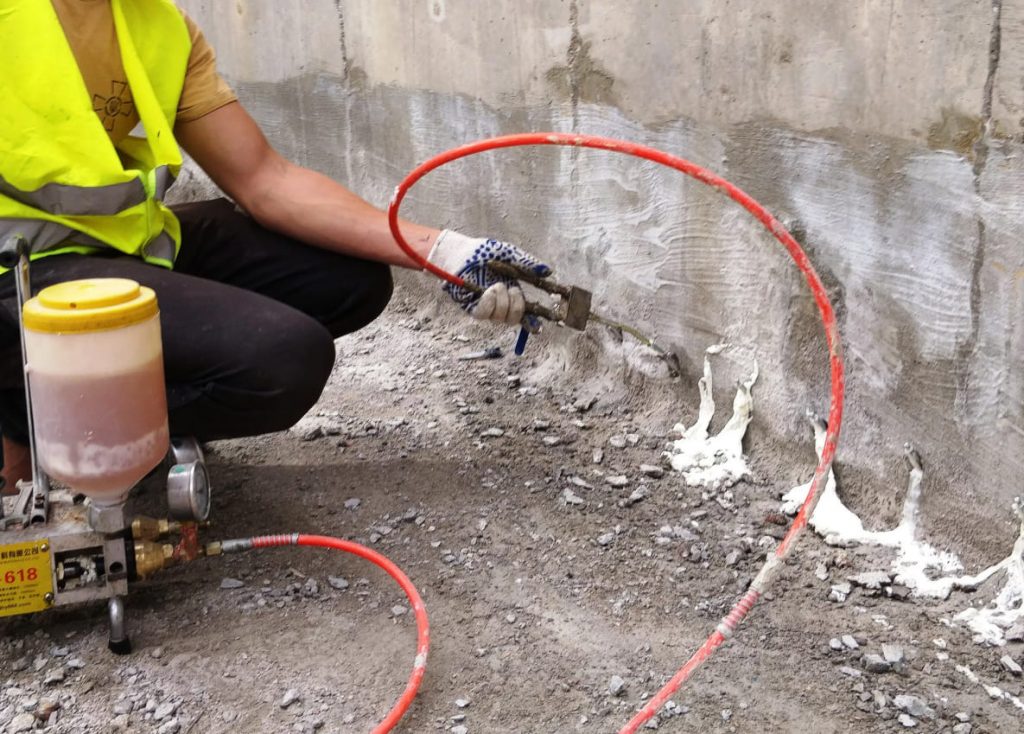
Advantages of the injection method:
- Can be used to seal various substances, such as concrete, brick, stone, and other natural substances;
- Can be used at any stage of construction, including during initial construction or later to extend the service life or repair, depending on the specific requirements of the project;
- Can be used both outside the room, on foundation or basement walls, and inside;
- Suitable for waterproofing the body of the structure, as well as for the arrangement of waterproofing joints (cold, concreting, deformation, etc.)·
- Injection waterproofing is one of the most effective methods of eliminating leaks from inside a private house or building.
Important: There are three main success factors that affect the effectiveness and durability of injection projects. It is very important that the right combination of injection materials, injection equipment and injection method is chosen.
Working scheme of horizontal injection waterproofing:

You can read more about injection in the article – “Injection waterproofing“
Liquid rubber
Liquid rubber consists of modified bitumen, latex, binders, and other polymers. When the surface is horizontally coated with liquid rubber, a waterproof coating is formed that can withstand the movement of any structure and even shrinkage of the foundation of the house, since liquid rubber has an excellent coefficient of tension and elasticity.
Advantages of liquid rubber:
- No seams;
- Elasticity is more than 800%;
- 100% adhesion with the surface;
- The ability to cover an area of 400m2 per day (when using spraying).
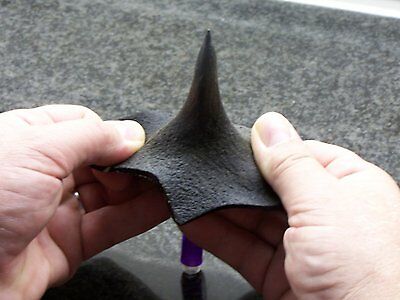
Installation technology of horizontal water protection:
- Removal of sharp corners and peeling elements;
- Analgesia of the surface;
- Applying a primer (base coating);
- Spraying or applying liquid rubber.
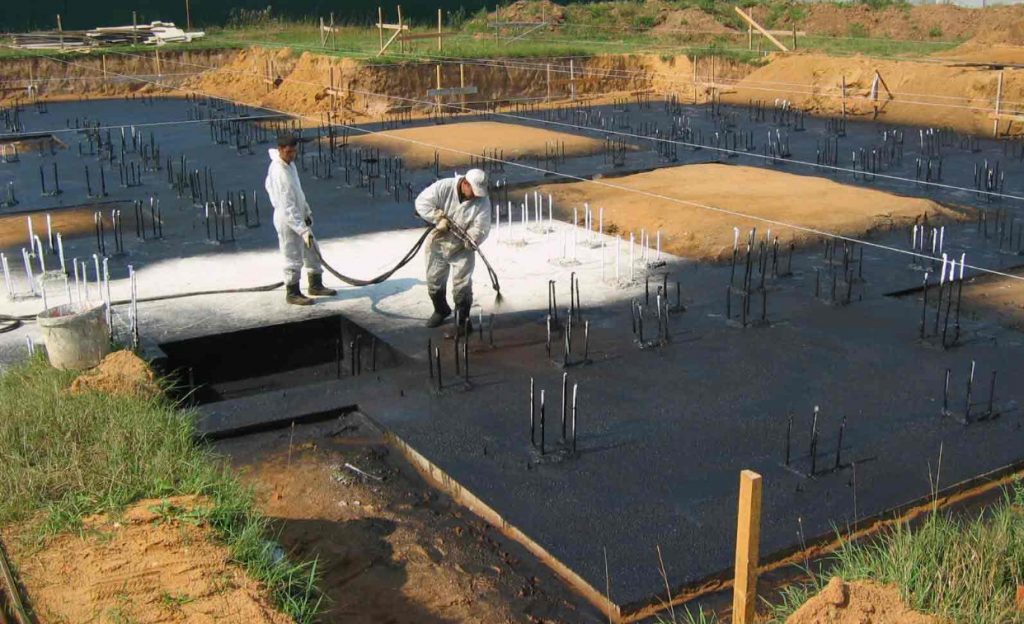
You can read more about liquid rubber in the article – “Waterproofing with liquid rubber“
Differences between the main types of insulation in the table
The following table compares the main types of waterproofing:
Liquid rubber | Roll surfaced and pasted | Penetrating | |
Availability of seams | Not available | Available | Not available |
Adhesion to the horizontal base | 100% | 40% | 100% |
Coefficient of elasticity | 600-800% | 20-90% | Not available |
Mounting method | Spraying or brush and roller | Surfacing with a burner | Brush and roller |
Application by the type of foundation (recommendation) | Slabby ribbon | Ribbon | Not recommended |
Service life of the material | 40 years | 10-30 years | 5-6 years |
Warranty period for works | 7 years | 3-5 years | 1-2 years |
Arrangement technology of horizontal waterproofing by the type of foundation
The technology and method of waterproofing on the horizon may vary depending on the type of foundation and its structure, since each foundation has its own characteristics.
Horizontal waterproofing of the ribbon foundation
Waterproofing on the horizontal surface of a ribbon-type foundation is recommended to be made of pasted, surfaced or mastic materials, while the latter form a reliable seamless coating with 100% adhesion to the base. When choosing coating materials, it is best to use liquid rubber or high-quality mastics applied in 2-3 layers. When performing work related to the insulation of the tape type of foundation, horizontal protection should be applied in 2 places:
1.between the foundation sole and the foundation blocks (No. 1 on the diagram)
2. between the blocks and the subsequent wall (No. 2 on the diagram).
The horizontal protection of the tape will serve as a cut-off and will not allow capillary moisture to rise through the blocks and exit indoors in the form of a wet or wet spot.
Installation scheme of horizontal waterproofing of the ribbon foundation:
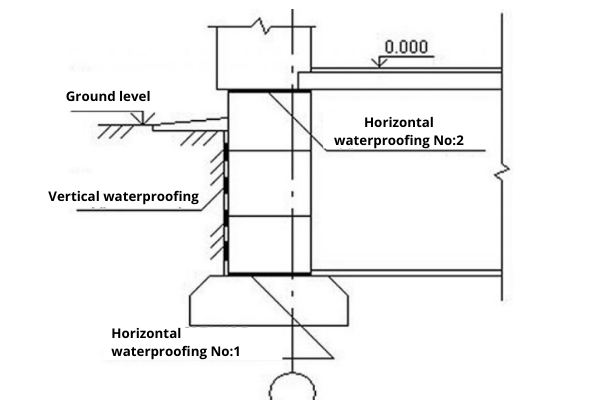
Horizontal waterproofing of slab foundations
When installing a slab foundation, a rigid base is first mounted, on which the slab, so-called leveling concrete will be erected, and it is on it that the first contour of horizontal insulation is applied. After pouring the slab, before erecting the walls, horizontal waterproofing is applied to the slab (2nd contour). After the walls are erected, the vertical waterproofing joins with the horizontal one, forming a hydraulic lock. To protect the slab foundation on the horizon, the materials below can be suitable:
- Surfaced;
- Membrane;
- Pasting;
- Coating;
- Liquid rubber.
Recommendation: when using liquid rubber as waterproofing, an elastic, seamless rubber coating with full adhesion to the surface is obtained at the output, which makes this material an ideal option for long-lasting protection of the slab and other foundation elements from water and moisture. Such characteristics as the absence of seams make liquid rubber a more reliable and durable coating, and elasticity will not allow the material to crack or disperse at the seams when the foundation shrinks.
The installation scheme of different horizontal waterproofing of the slab foundation
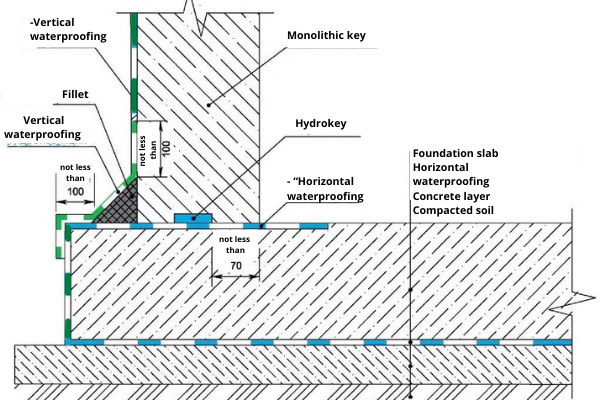
Horizontal protection of pile columnar foundation
In the case of pile construction, waterproofing is laid only at the end of the pile at the junction between the end of the foundation and before the construction of the walls of the house.
The location of the insulation may vary depending on what the grillage consists of.
1. Bored piles under the building made of concrete and concrete grillage – Insulation is placed between the installed grillage and the built wall of the house. Such a system is used to prevent the impact of constructs that differ in their characteristics.
2. Metal screw piles with a grillage made of wood – in this case, insulation is placed on the top of the piles to separate the metal and the subsequent structure.
The scheme of laying waterproofing in a pile foundation on the horizon
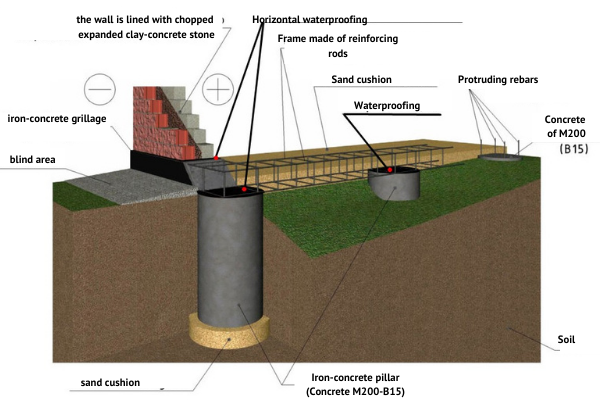
Rates for horizontal waterproofing with the prices per 1m2
The prices indicated are preliminary and may change in complex constructions.
Works description | Unit of measurement | Price in $ |
The installation of surfaced waterproofing on the horizon in 1 layer | m2 | starting from 5 |
The installation of a self-adhesive membrane on the horizon in 1 layer | m2 | starting from 4 |
Arrangement of PVC membrane on the horizon | m2 | starting from 7 |
Application of bitumen-mastic waterproofing in 1 layer | m2 | starting from 2 |
Application of liquid rubber by spraying | m2 | starting from 250 |
Application of liquid rubber manually | m2 | starting from 4 |
Application of polymer-cement double-component waterproofing | m2 | starting from 5 |
Application of penetrating compounds | m2 | starting from 6 |
Application of primer | m2 | starting from 2 |
Calculator for self-calculation of the cost of waterproofing
Calculation of waterproofing cost
The total cost of waterproofing
Recovery of horizontal waterproofing
If, at the construction stage, horizontal cut-off waterproofing between the wall and the foundation was not done or was done with violations, then its recovery after the walls were erected is possible only with the use of injection waterproofing. When the injection installation is made from inside a built basement, socle or other room, polyurethane injection resin penetrates under pressure into the space between the foundation and the erected wall, thereby restoring horizontal waterproofing, which also serves as a cut-off that prevents water and moisture from rising capillarily up the wall.
Waterproofing restoring technology on the horizon using injection:
1. Dismantling of finishing elements that prevent you from reaching the base of the cold seam of the abutment slab- wall. Such elements can be tiles, screed, drywall and plaster on the walls of the basement from the inside;
2. The arrangement of a small borehole at the junction of the wall and the surface of the foundation;
3. Layer-by-layer sealing of the expanding sealant into the made borehole. This procedure is necessary so that when the polyurethane resin is injected into the seam, the composition spreads horizontally inside the wall itself, and does not exit through a weak joint back;
4. Drilling holes at an angle of 45 degrees to the center of the cold seam or joint of the foundation and wall;
5. Installation of injectors or packers in drilled holes;
6. Connecting the injection pump to the installed packers and pumping the injection composition;
7. Dismantling of installed packers with sealing holes with a special expanding sealant;
Detailed recovery scheme:
