Table of Contents
- How the waterproofing membrane works, its advantages and disadvantages
- Where can membranes be used as a waterproofing coating
- Types of waterproofing membranes and their characteristics
- PVC Membranes
- Membrane waterproofing arrangement — How to do the work correctly so as not to redo it later
- Prices for the arrangement of membrane waterproofing
- Waterproofing Cost Calculator
- Frequently Asked Questions about Membrane Waterproofing System
Membrane waterproofing — is one of the most modern types of waterproofing coating that perfectly protects buildings from the harmful effects of water and moisture. When waterproofing a building, private house, pond or foundation using various membranes, a high-quality waterproofing coating is laid on the surface, preventing water and moisture from passing through it and affecting concrete, brick or other building composition.
How the waterproofing membrane works, its advantages and disadvantages
By its composition, the membrane belongs to the group of polymer insulating coatings. Most membranes are made by layering the thinnest rolled layers on top of each other, each of which has its own characteristics. The layers merge into one substance under the influence of temperature and pressure, giving the final product a set of special properties. Most often, manufacturers lay an additional outer layer of bright yellow color, which allows you to determine the location of damage to the membrane.
When installing waterproofing using a membrane, the membrane is laid on the base like a carpet and attached to it with a special clamping bar or rail. The seams between the sheets are sewn together with hot air or glued together with a special glue.
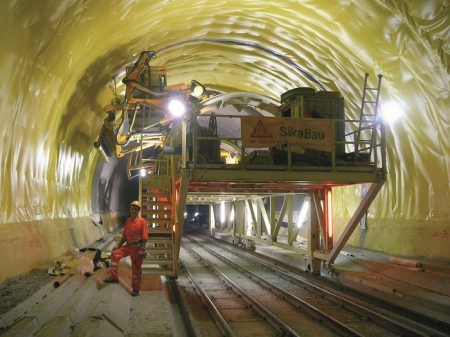
Advantages:
- This is a durable material that, with the right installation, can last at least 50 years. A long service life is established due to the complex structure of membrane waterproofing. In many types of membranes, the composition includes substances responsible for resistance to the action of salts and other trace elements.
- Membrane waterproofing is not afraid of temperature changes, it can safely withstand both extremely high and extremely low temperatures.
- The temperature range at which installation and operation is possible is approximately from -60 to +120 degrees.
- High quality and elasticity of the material prevent the possibility of rupture and, accordingly, leaks. The flexibility of the material is also facilitates its arrangement.
- The elasticity of the material is maintained at any temperature, which greatly extends the service life of the waterproofing coating.
- Low weight and occupied volume facilitates the transportation of the material and the process of its installation.
- Before installing the membrane, there is no need to carry out certain procedures related to careful preparation of the substance. This feature favorably distinguishes membrane waterproofing from bitumen, where a properly prepared surface plays a key role.
- The material is convenient to use on all surfaces, especially in areas, where there are no superstructures, for example, an elevator shaft or a pipe. Membrane waterproofing can be laid even on a heat-insulating layer.
- The membrane is arranged in such a way that considerate or any other moisture practically does not accumulate on it and under it.
- The installation of the membrane takes place without the need for the use of live fire, which distinguishes it from the surfaced installation.
Important: In accordance with the standard, many membranes have a brittleness temperature of -49 degrees, respectively, they will remain flexible and pliable for the installation at extremely low temperatures. However, adhesives, primers and ribbons with which the seams are connected may not withstand negative temperatures, which will eventually lead to weakening of the seams and possible future penetration of water and moisture.
Disadvantages:
- Instability to mechanical influences. When in contact with sharp objects, it can easily tear. Because of this, difficulties may arise if the membrane is not properly glued.
- The availability of a large number of seams over the entire area of the waterproofing coating. Seams -are the weakest points in any coating and one of the biggest drawbacks of all roll waterproofing including membrane one.
- Complete absence of adhesion (adhesion) of the material to the base. Since the membrane lies on the surface of the carpet and there is a void between it and the base, then if there is even a small microcrack or hole in the membrane or in one of the seams, the water will pass under the membrane carpet freely and spread under it, leaning the room in the weakest places.
- Relatively high price compared to bitumen waterproofing.
Alternatives to membrane insulation:
Taking into account such disadvantages as the presence of seams and the lack of adhesion (adhesion) to the base, which is characteristic of the entire line of rolled waterproofing materials, the following systems can serve as an alternative:
- Liquid rubber – This material can be studied in more detail in the article “Waterproofing with liquid rubber”.
- Polyurethane waterproofing – This material can be studied in more detail in the article “Polyurethane waterproofing”.
Both of these systems have basic properties that are distinctive from the membrane and other rolled materials:
- Complete absence of seams.
- 100% adhesion to the base.
Where can membranes be used as a waterproofing coating
Today membranes are used for waterproofing the following structures of buildings and constructs:
- Flat roofs
- Pitched roofs
- Ponds
- Swimming pools
- Waterproofing of underground parts of buildings and structures
- Waterproofing of the foundation
- Foundation slab
- Walls
- Waterproofing of the basement from the outside
Waterproofing of the roof
Membranes can be used as waterproofing in the construction and construction of roofs of various types. Membranes are used not only in a flat roof, but also with a slope. Thanks to some types of membranes, the useful area of a flat roof can be used for the arrangement of a garden, greenhouses or places for recreation.
Waterproofing by the membrane method helps to hide the architecture from unwanted protrusions, smoothes sharp corners. To do this, the connecting parts of the structure, panels are pre-measured and joined with extreme accuracy.
You can read more about roof waterproofing in the following articles:
- Waterproofing of the roof: methods of its construction and types of materials for performing high-quality work
- Waterproofing of a flat roof. Recommended materials, methods of their installation and prices for work
- Waterproofing and repair of pitched roofs
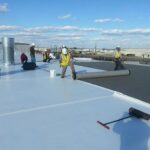

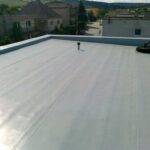
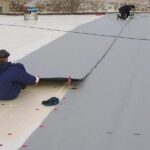
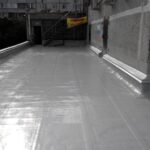
Waterproofing of the foundation
When laying the foundation, it is recommended to use PVC membranes, the composition of which is based on polyvinyl chloride. During installation, the membrane is fixed to the foundation walls themselves using special clamping strips or slats.
Another feature of foundation membranes is the ability to facilitate future repair of waterproofing at the stage of its initial installation, by laying systems of insulating cards and installing injection fittings. This structure allows you to prevent leaks and quickly dispose the damaged area by performing injection work from inside the future structure. Repair is carried out using injection fittings, into which various compounds are pumped, thereby acting not on the entire insulating layer, but only on the site of damage.
You can read more about foundation waterproofing in the article – “Foundation waterproofing arrangement: Methods, materials, prices and recommendations of specialists”.
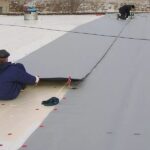
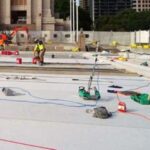
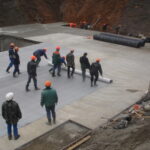
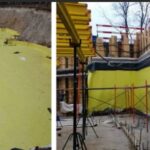
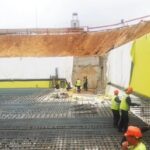
Waterproofing of walls
Walls without high-quality waterproofing are subject to external influences: Water, moisture, temperature gradient. All these undesirable processes from the outside can cause the destruction of concrete or brick from which the walls are made. In the absence of proper waterproofing of the walls in the basement and socle rooms, mold and fungus may also appear, negatively affecting the quality of life in the room.
Membranes are good because they are extremely easy to install even on vertical walls. Installation is carried out clean and preferably dry surface, when laying there is no need to glue the material over the entire area, it is enough to fix it with a bar.
Preparation of walls for waterproofing is carried out by cleaning the walls from old insulation materials, finishing elements, dust and dirt, as well as stripping them from chips and sharp protrusions. Unwanted cracks are filled with a special solution and leveled.
You can read more about waterproofing walls in the article – “Waterproofing of basement and house walls from the outside and inside – Methods, materials, prices and technology”.
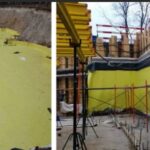
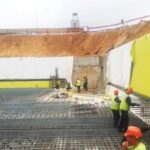
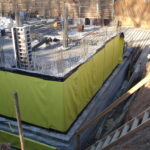
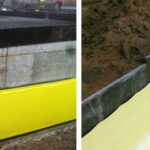
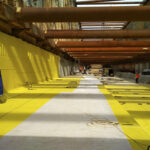
Waterproofing of ponds and reservoirs
When arranging various types of reservoirs and ponds, PVC or Ethylene Propylene Dien Monomer membrane is often used. This method is acceptable both for clay bases and for soil ones.
Preparation for insulation work requires cleaning the surface of the pond from rhizomes, boulders and other natural elements that can damage the insulation film. After that, the base is carefully rammed. The waterproofing coating is mounted either with one seamless sheet or several large sheets that are hermetically connected to each other. The mounted membrane is brought over the edges of the reservoir into a specially prepared trench along its perimeter.
You can read more about the waterproofing of ponds in the article – “Waterproofing of ponds and reservoirs: Methods and materials“
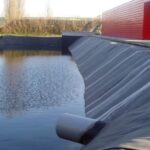
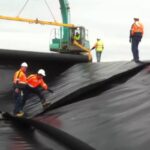
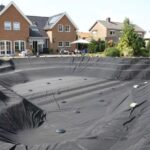
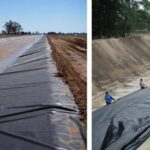
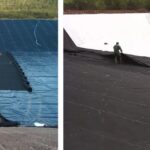
Types of waterproofing membranes and their characteristics
Waterproofing membranes are divided into several types depending on the composition, each type has its own features of installation and operation. High-quality protection of the structure from water will be effective only if the material for this protection is selected correctly.
Important: The wrong choice of waterproofing material may in the future lead to additional expenses for heating the room.
PVC Membranes
PVC membranes — are the most popular and demanded type of waterproofing today. Its prevalence is associated with high quality, which is achieved by the design feature of the material.
PVC is used mainly on such constructs of building as:
- Roofs
- Foundations
- Foundation slabs
- Walls
Advantages:
- The complex structure of the PVC membrane causes its high elasticity, the material can stretch up to 400 %.
- Resistance to aggressive environmental salts.
Disadvantages:
- The potential harm to health from volatile plasticizers should be noted among the disadvantages that are part of the membrane. And also polyvinyl chloride membranes are not very strong and can tear.
Main Features:
PVC consists of two layers: the lower one is made of pure polyvinyl chloride and is often painted in bright colors to immediately detect damage. The top layer is complex in composition: it includes chalk, antiperens and plasticizers.
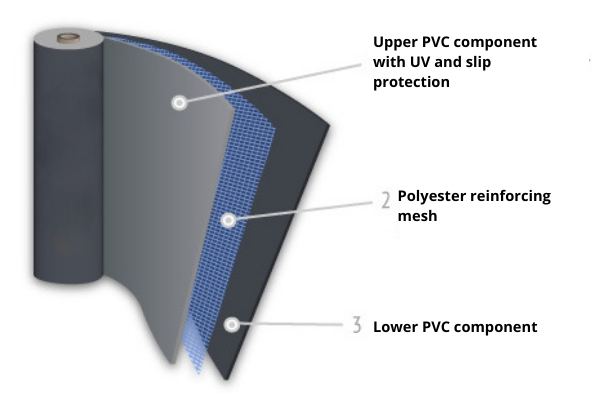
Table of characteristics:
The name of indicator | Unit of measurement | Value |
Tensile strength | Н/50 mm | along the roll ≥1100 across the roll ≥900 |
Extension at max. load, not less than | per cent % | 15 |
Tear resistance, not less than | Н | 150 |
Full folding at negative temperature | °С | -30 |
Water absorption by weight, no more | per cent % | 0,3 |
Wear under the influence of UV radiation | No cracks on the surface | |
Water resistance, 10 кPа for 24 hours | No traces of water penetration | |
Resistance to dynamic penetration (impact resistance) on a hard base (in parentheses-on a soft base), not less than: | 1,2mm 1,5mm 1,8mm | 600 800 1100 |
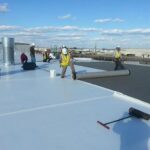
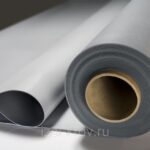
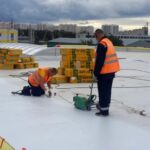
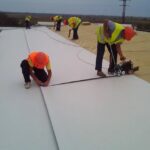
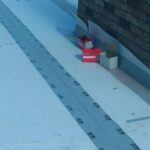
Installation features:
PVC membranes are easy to install: they do not require careful surface preparation, but it should be borne in mind that in contact with bitumen or phenol, there is a high probability of damage to the insulating layer. Sheets of PVC material are easy to connect, hot air is applied to the edges to stitch the sheets, but the strength and reliability of the fastening is preserved, which minimizes the possibility of leaks.
PVC membranes of various thickness are available on the market, designed for installation on roofs and foundations at various depths.
Thermoplastic Polyolefin (TPO)
TPO membrane is thermoplastic polyolefin, which uses advanced polymerization technology to combine ethylene-propylene (EP) rubber and polypropylene as a base material, consisting of mesh fabric as a matrix reinforcement before polymerization.
TPO is mainly used in the installation of a waterproofing layer in such structures as:
- Reservoirs
- Ponds
- Tanks for drinking water and other liquids
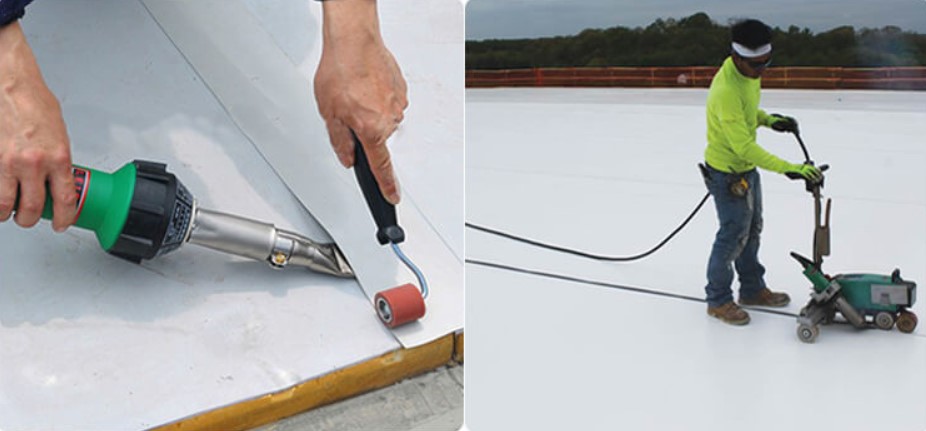
Advantages:
- TPO membranes differ from other membranes in their strength and elasticity. At the same time, the material is quite environmentally friendly, its composition does not include volatile synthetic substances.
- Polyester fiber fabric between two layers of TPO improves physical properties, increasing tensile strength, abrasion resistance and puncture resistance.
- The seams between the sheets can be welded with a special device.
- The service life of the original is more than 70 years.
- Weather resistance. It has good efficiency in the temperature range of -70°C~150°C.
- No additional protection procedure is required during installation.
- May be exposed to sunlight.
Disadvantages:
- Building materials are not very popular for insulation of the roof and foundation due to the high cost.
Main features:
Double-layer membranes consist of a polymer mixture and a reinforcing mesh. The first component consists of polypropylene and rubber, that is, it includes rubber and plastic. The composition of the polymer mixture also often includes various types of additives that provide the material with properties that extend the service life.
The table of characteristics:
The name of the indicator | Unit of measurement | Value |
Tensile strength | Н/50 mm | ≥1100 |
Extension at max.load, not less than | per cent % | ≥15 |
Impact strength | mm | ≥450 |
Complete collapsibility at negative temperature | °С | -40 |
Thickness | mm | 1,2-2 |
Wear under the influence of UV radiation | No cracks on the surface | |
Water resistance, under pressure of 0,5MPа | waterproof | |
Resistance to static punching | kg | ≥20 |
EPDM
EPDM membrane is an attractive choice for the arrangement of various types of roofing. EPDM is still one of the most preferred materials when choosing architects, roofing consultants and contractors for both new construction and roof replacement projects.
EPDM is one of the most sustainable and environmentally responsible roofing materials used in the construction industry today. Less frequent replacement leads to a reduction in the destruction of buildings and a reduction in environmental impact. The initial production of the membrane has a low energy value (the amount of energy required for the production and sale of the product as a result of the extraction, manufacture and installation of the material).
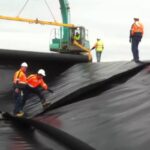
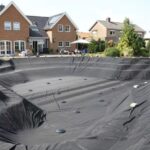
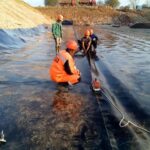
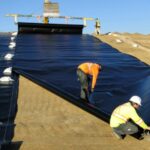
Advantages:
- Compatibility with bitumen surfaces, which allows you to combine two types of waterproofing. This type of materials is absolutely safe and does not emit toxic substances.
- Resistance to cyclic wear.
- Proven resistance to hail.
- High resistance to weathering and abrasion.
- Flexibility at low temperatures.
- Excellent resistance to extreme heat and fire.
- Resistance to heat.
- UV resistance.
- One of the unique properties of EPDM is its ability to be easily repaired and restored. Even after many years of operation, repairs or modifications involving the installation of a new coating on an old roof can be easily carried out with the expectation of long-term performance.
Disadvantages:
- The disadvantage may be a sticky element at the base of the membrane, that is why there is a possibility of a breakthrough of the seams.
Main features:
EPDM — is an elastomeric polymer synthesized from ethylene, propylene and a small amount of diene monomer mixed with soot, process oils and various crosslinking and stabilizing agents. As a thermosetting membrane that recovers its shape after stretching, EPDM retains its physical properties for decades. EPDM is made from large sheets ranging from 10 to 50 feet wide and up to 200 feet long. The membrane can be reinforced and has a thickness of 45, 60, 75 and 90 mm.
EPDM materials are based on synthetic rubber, which gives the composition elasticity and resistance to very high and very low temperatures. The second layer , polyester mesh, provides the membrane with special mesh.
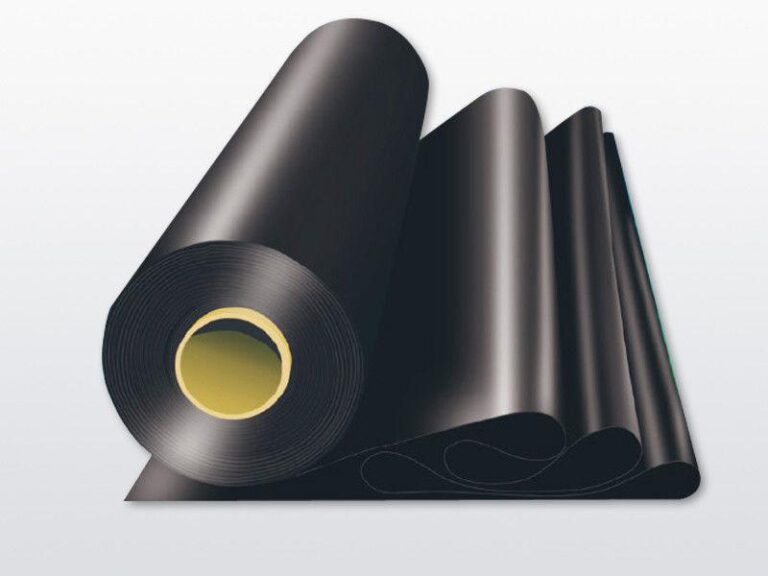
Table of characteristics:
The name of the indicator | Unit of measurement | Value |
Tensile strength | Н/mm² | ≥8 |
Relative extension | per cent % | ≥300 |
Tear resistance | Н | ≥50 |
Frost resistance | °С | <-45 |
Thickness | mm | 1,2-2 |
UV resistance | No cracks on the surface | |
Water absorption | ≤1% | |
Resistance to static punching | kg | ≥30 |
Installation features:
Installation methods (ballasted, fully glued and mechanically fixed) allow the membrane to be installed on slopes with positive drainage up to vertical application for fully glued systems. Good roofing practice always includes provisions for proper drainage for any type of roofing system and in most cases is dictated by local building codes. Since EPDM remains stable over a wide temperature range, this allows it to be installed all year round in any climate.
Membrane waterproofing arrangement — How to do the work correctly so as not to redo it later
The arrangement of various types of membranes can be reduced to several main points:
- Preparation of the base;
- Mechanical fastening of sheets;
- Proper stitching of seams between sheets-seams are the weakest points in this type of waterproofing and it is on high-quality stitching of seams that it is worth focusing on when carrying out work.
How to glue the seams on the membrane
There are 3 ways to connect the seams:
- Hot air stitching-This can be done with a construction hair dryer or a special device.
- Gluing with a special glue – When using liquid glue, the adjacent sheets are cleaned with a product, recommended by the manufacturer. A sealant is used along the edge of the joint, which is applied after the solvent in the adhesive dries (at least 2 hours). Some manufacturers recommend using an additional sealant in the overlap area, which is applied immediately before the connection. The sealant is used as a secondary protection against moisture penetration in case of manufacturing errors at intersections with factory seams.
- Using adhesive tape – this method of sizing seams was developed to speed up the processing of seams while maintaining uniform application throughout the seam. This process involves the use of adhesive tape in combination with a primer for strong bonding of the membrane seams. Adjacent membranes are primed, then, as soon as the primer dries, a tape is applied. No additional sealant is used along the edge of the joint. This method has become more profitable due to the sequence of application.
Some features:
The features of the membrane installation differ somewhat depending on the place of its use. Subtleties that should be taken into account in your work so that there are no reasons for repairs in the future:
Wall mounting
Even before the installation of the membrane begins, it should be cut into convenient pieces;
Parts of the sheets are stacked from bottom to top with a slight intersection— about 10 centimeters.
The intersection points should be additionally glued together with a sealing tape;
The membrane is fixed to the clamping bar of 15-20sm above the planning ground level.
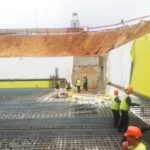
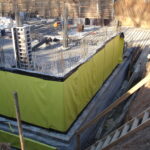
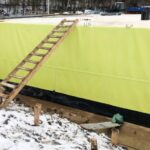
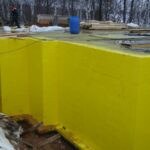
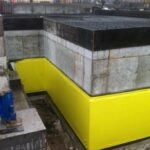
Installation on the foundation
Before starting the installation, the surface should be carefully prepared: clean from dust and dirt, remove all stones, level cracks and irregularities. If possible, cover with an additional layer of primer.
The membrane is not very durable, so you should take care of an additional layer of overlapped geotextile, which will protect the membrane from mechanical damage.
The device goes through two stages: Horizontal and vertical.
- At the first stage, the arrangement of sheets should be performed on the prepared surface. Then you should apply another meter layer at the junctions with the vertical and horizontal sheets.
- The vertical stage begins with the installation of the rondels at a distance of two meters from each other. The membrane is mounted on top of a plastic blank, fixed to each rondel. A protective layer is applied on top to prevent mechanical damage.
A detailed guide on the installation of the membrane on the foundation can be downloaded by clicking on the following link – Installation instructions for the waterproofing system of the foundation of PVC membranes.
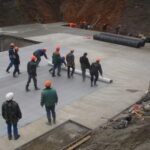
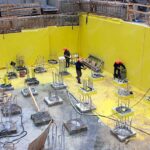
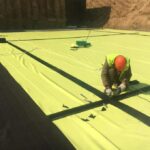
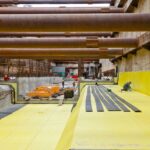
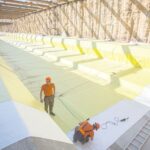
Roof arrangement
Before starting work, the base should be cleaned of stones, sharp objects, irregularities and dirt;
The pieces of the membrane are superimposed on top of the roof base horizontally face up. During installation, the material should not be stretched too much. After that, the waterproofing is pressed. The edges of the waterproofing should be fixed with a special rail, the pieces should be glued on top of each other with an intersection of 15 centimeters.
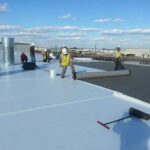
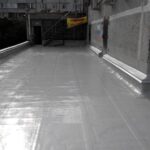
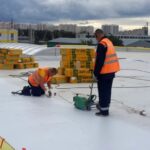
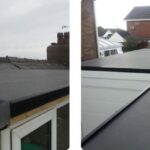
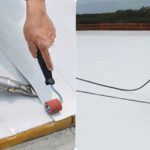
Prices for the arrangement of membrane waterproofing
The cost of installation services depends on the complexity and volume of the work to be done. The quality of the material used may also differ, which also affects the cost. To obtain the final cost of installation, you need to send an application to our e-mail address or call our specialist to your facility to carry out accurate measurements and assess the complexity of the work.
The following price list shows prices for membrane waterproofing of various types, including roofs, foundations, ponds and reservoirs.
Description of work | Unit of measurement | Price in $ |
Arrangement of PVC membrane of 1,5mm by thickness | m2 | 10 |
Arrangement of PVC membrane of 2mm by thickness | m2 | 15 |
Arrangement of TPO membrane | m2 | 10 |
Laying of EPDM membrane | m2 | 20 |
Laying the membrane on a concrete base | m2 | 10 |
Laying the membrane on a profiled sheet | m2 | 20 |
Arrangement of membrane insulation junctions | running meter | 30 |
The arrangement of a membrane inversion roof without mechanical fastening | m2 | 10 |
The arrangement of the membrane during the installation of the ballast system | m2 | 10 |
The arrangement of fire-retardant membrane | m2 | 40 |
The arrangement of a vertical waterproofing with a PVC membrane | m2 | 60 |
The arrangement of vertical waterproofing of the foundation with a TPO membrane | m2 | 60 |
Waterproofing arrangement of the foundation slab with a membrane | m2 | 55 |
Installation of rails and mechanical fastening | running meter | 10 |
Waterproofing Cost Calculator
Calculation of waterproofing cost
The total cost of waterproofing
Frequently Asked Questions about Membrane Waterproofing System
- On which roof structures can membrane be installed?
The availability of a wide range of products makes the membrane system universal. For example, the membrane can be glued directly to wooden, concrete and steel surfaces. Special fastening components are available for decking with low tear resistance (e.g. gypsum, fibrous cement and light steel). Ballasted assemblies can be used only on any surface as long as the structure is able to withstand the weight of the installed system. The choice between a glued, mechanically fixed or ballasted node can be influenced by the type of the structure and its condition. - Is it necessary to dismantle the old insulation during the reconstruction of the roof?
Despite the fact that most roofing materials are completely dismantled, the old or existing system can be left in place after the preparatory work is completed. However, the existing insulation and roof decking should be checked before re-installing the insulation to ensure compatibility and structural integrity. - What is the average specific weight of roofing systems based on EPDM or PVC?
The weight of the roofing system varies depending on the components used. After combining the weight of the components, namely the membrane itself, fasteners and glue, the typical weight is less than 10 kg per square meter. When using a 0.15 sm thick membrane, the weight of the structure will be 1.6 kg per square meter. - Is it possible to paint EPDM or other membranes?
Acrylic coatings are available that can be applied directly to the prepared surface, for example, EPDM sheets. Preparation usually consists of cleaning the EPDM with a high-pressure washer and a cleaning solution. Latex-based paints and varnishes can also be used, however, before, applying, contact the EPDM manufacturer to accurately ensure the compatibility of the compositions. - Are there temperature restrictions on the arrangement of different types of membranes?
In accordance with the standard, many membranes have a brittleness temperature of -49 degrees, respectively, they will remain flexible and pliable for the arrangement at extremely low temperatures. However, adhesives, primers and tapes with which the seams are connected may not withstand negative temperatures, which will eventually lead to weakening of the seams and possible future penetration of water and moisture.