Table of Contents
- What is Cementitious waterproofing coating?
- Types of Cementitious waterproofing materials and products
- Advantages and disadvantages of cementitious waterproofing
- Application technology for cementitious waterproofing coating
- Overview of the most famous brands, their characteristics, and consumption per m2
- Prices for materials and works
Cementitious waterproofing systems, as the name implies, are made on the basis of cement and their aim is to prevent the penetration of water, water vapor and moisture into concrete and other surfaces. Later in the article we will study this material in detail, its types and application technologies.
What is Cementitious waterproofing coating?
Cementitious waterproofing systems contain a base of Portland cement, with or without sand, and active waterproofing additives. There are four types of systems: metallic, capillary, chemical additive and modified with acrylic.
Cementitious waterproofing systems are effective at both positive and negative water pressure. These materials are applied with a brush, spatula or spray on concrete, brick or stone surfaces and become an integral part of the base.
All compounds are supplied as a dry mixture and are mixed with water and other components when applied, if available.
Cementitious waterproofing systems are excellent materials for use in civil and infrastructure projects.

The constituent of Cementitious waterproofing coating
All Cementitious waterproofing products are similar by the application and productivity, but they repel water in different ways and this is due to proprietary additives and recipes of manufacturers.
This table describes the tailored composition of Cementitious waterproofing:
Component | Component consumption, kg |
Portland cement | 660 |
Quartz sand | 241 |
Microsilicasuspension | 66 |
Redispersible powder | 33 |
Superplasticizer | 2,3 |
Water-retaining agent | 1,3 |
Standard physical-mechanical and technical characteristics of Cementitious waterproofing:
Properties | Values | Values in accordance with the requirements of standards | |
Water-retaining capacity, % | 95 | Not less than 90 | |
Compressive strength, MPa | 46 | The waterproofing coating should not reduce the design strength of the protected concrete | |
Tensile strength at break, MPa | 1,3 | GOST Р 56703 | |
Adhesive strength, MPa | 1,7 | More than 0,5 | |
Overlapping cracks, mm | 0,8 | More than 0,75 | |
Crack throughput class | А3 | More than 0,5mm | |
Water resistance, atm., class | W14 | Not less than W6 | |
Consumption per 1 m2, kg | 1,5-1,8 |
It is important to note that the above characteristics are a kind of standard set of characteristics for most waterproof cement compositions, however, as we said earlier, different manufacturers add the above components in different proportions, not necessarily as required by the standard.
Important: Sometimes it is worth listening to the well-known proverb - "There is no good cheap. The price of the product, and the product at the price." When buying, pay attention to the cost of waterproofing material and its composition, as a rule, the lower the cost, the less high-quality components were added to the composition or they were added in a smaller proportion.
Where it can be applied
Cementitious waterproofing solutions are mainly used by the waterproofing arrangement of the following constructs:
- Foundations;
- Walls of buildings;
- Walls of basements and socle floors;
- Terraces;
- Balconies;
- Roofs;
- Swimming pools;
- Basement floors and floors
in industrial workshops and wet areas; - Tanks for various purposes, including those for drinking water;
- Tunnels;
- Underground storage facilities and structures;
- Sewage treatment plants;
- Lift shafts;
- Bridges;
- Dams;
- Ports and docks;
- Underground parkings;
- Floor slabs.
These solutions are mainly applied to the concrete base since it is with it that they have 100% adhesion (adhesion).





Types of Cementitious waterproofing materials and products
Waterproofing compositions based on cement are divided mainly by their composition. Each of the types can be both double-component and single-component and has its own strengths and weaknesses.
Main types:
- Cement-sand with metal materials;
- Capillary-crystalline or penetrating;
- Cement waterproofing with the addition of latex;
- Cement-polymer, acrylic, and the addition of liquid glass.
Further, we will study each of the above types in detail.
Cement-sand waterproofing and metal compounds
Metal materials contain a mixture of sand and cement with fine iron aggregate or sawdust.
When mixed with water, to form a suspension for application, water acts as an agent that allows iron filings to oxidize. These materials expand due to this oxidation, which then effectively seals the substrate and acts as a waterproof barrier stopping the passage of water and moisture through concrete or other substrates. This system is one of the oldest waterproofing methods (first patented in 1906) and remains quite effective today.
Metal systems are applied in two or three layers, with the last layer being a sand-cement mixture that provides protection on top of the main waterproofing layer where it is exposed. This final coating prevents leaching or oxidation of the base due to the paints or other finishing elements applied to it. This type of waterproofing also protects the horizontal concrete base from excessive wear due to pedestrian or automobile loads.
Capillary-crystal penetrating
The capillary-crystal system is not only waterproof, but its chemical additives are also able to penetrate into a concrete wall or slab and react with calcium hydroxide and available capillary water, forming crystal structures inside the concrete itself. These crystal structures block the possibility of water passing through the substrate, adding additional water repellency to the shell components.
The chemical process begins immediately after applying the penetrating cement composition, but obtaining the maximum waterproofing effect can take up to 30 days. Penetrating mixtures have other advantages over other cement-based formulations, including the following:
- No need for a protective layer;
- Some materials have the ability to seal hairline cracks, that occur during the operation of concrete;
- Most penetrating crystal systems are not damaged by chemicals and acids, which makes their application ideal for tanks, wastewater treatment plants, and similar structures;
- Penetrates into concrete and reacts with it, forming additional protection against destruction.
You can read more about penetrating cement waterproofing in the following article – «Penetrating waterproofing: Detailed description of its work on concrete, types of materials and application technology».
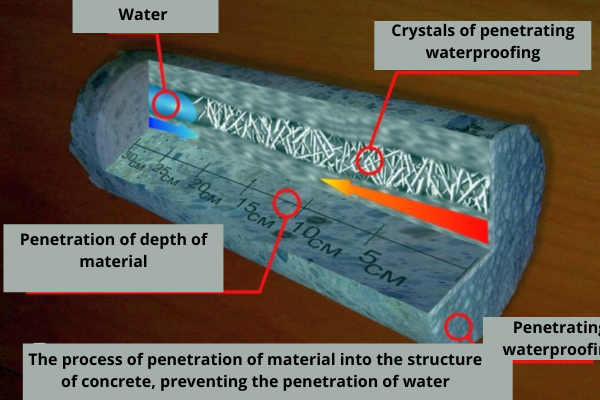
Cementitious waterproofing with addition of latex
Chemical cement systems are a mixture of sand, cement, and patented chemicals (inorganic or organic), which, when applied to masonry or concrete foundations, ensure the water resistance of the foundation by chemical action. The patented chemicals are unique for each manufacturer, but usually include derivatives of silicates and siloxanes in combination with other chemicals, including latex. Although the chemicals do not penetrate the substrate like other cementing materials, they also effectively become an integral part of the substrate after they are applied.
Chemical systems with a thickness of about 1- 2 sm are thinner than others. As with all cement materials, concrete bases should not be dry and it should be moistened before applying the solution.
Cement-polymer and acrylic
Acrylic-modified cement mixtures differ from the rest in that acrylic emulsions are added to the main cement-sand mixture. These acrylics add waterproofing characteristics and properties to materials. Acrylic systems are applied with two spatulas, and the reinforcing mesh is installed after the first layer is applied. This grid adds some opportunities to overcome cracks when they occur. However, since cement-polymer materials are firmly bonded to concrete or stone bases, their elasticity is limited.
These materials are applicable both on the positive side and on the negative side (from inside the room) and, accordingly, withstand negative water pressure from the outside to the inside.
Advantages and disadvantages of cementitious waterproofing
Like other materials cement also has its advantages and disadvantages.
Advantages:
- Easy to apply. Using and applying cement mortars and mixtures as waterproofing is quite simple if you clearly follow the manufacturer’s instructions. The coating cement insulation is applied using a spatula or a brush with stiff bristles.
- Availability. Most of the products are available for purchase in hardware stores.
- Absence of seams and joints. Cement-based coating insulation forms a seamless coating, which has a positive effect on its durability and water resistance.
- No need for a dry base. You can start work quickly after pouring concrete.
- Convenient for subsequent finishing. When using cement-based compounds it is not necessary to erect a screed on them for a subsequent installation of tiles or other finishing materials (unlike Roll and bitumen insulation, on which it is not recommended to mount the tile without first installing the screed).
- Durability. Compositions, made of cement and designed for insulation, in most cases are not only waterproof but also chemically resistant, as well as resistant to abrasion and weather conditions, including frost.
- Binder. Waterproof coatings glue porous and non-porous coatings well, as well as old and new concrete.
Disadvantages:
- Low coefficient of elasticity.
- Most cement materials do not have crack resistance or elastomeric properties. With strong dynamics or even simple shrinkage of the building, the cement insulation cracks, allowing water to penetrate.
Application technology for cementitious waterproofing coating
Cementitious waterproofing can either be sprayed using a special spraying unit or applied manually by coating it. The most popular method of applying cement waterproofing coating is manual application.
Stages of work production:
- Preparation of the base – The first step is to clean the base from peeling elements, dirt, and dust;
- Seal up all existing cracks and other defects of concrete with the help of non-shrink compounds and expanding sealant;
- Take care of the intending installation (a small plinth of Cement-Sand Mixture) for the transition of waterproofing from the horizon to the vertical;
- Thus, you will be able to avoid weak node of 90 degrees during the transition of the coating, for example, from the floor to the walls;
- Moistening of the surface – Cement mixtures should not be applied to a dry base. Before the waterproofing installation, the surface should be moistened to a certain extent, otherwise, 100% adhesion of the material to the base may not work;
- Preparation of the material – This procedure is one of the most important, especially, when it comes to double-component materials. When preparing the mixture, it is necessary to mix dry cement powder with water and other components, as is written in the instructions for a particular material. Each manufacturer has its own instructions to follow;
- Arrangement of coating insulation – The material is applied to the base by coating, using a brush or spatula in 1 layer;
- Installation of the second layer – If necessary, after the first layer is gripped, the second layer can be applied by coating. The waiting time between the first and second layer is determined depending on the applied material (described in the instructions for the material);
- Subsequent finishing – If you plan to install finishing elements in the form of drywall, plaster, or other cladding after applying the coating cement insulation, then first you need to install the furring, which is glued directly to the waterproofing. This eliminates nailing boards with nails or self-tapping crews through the Cementitious waterproofing membrane.
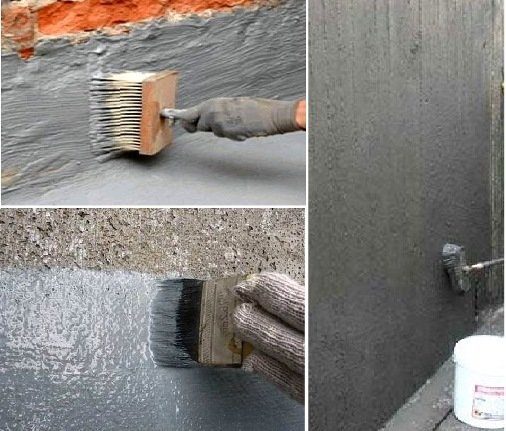
Overview of the most famous brands, their characteristics, and consumption per m2
There are quite a lot of Cementitious waterproofing systems and they all differ from each other in their characteristics, consumption per m2, price, and other parameters.
Ceresit CR 65
The waterproofing mixture of CR 65 is designed for the installation of waterproof coatings on strong bases and surfaces, cleaned of salts and oils.
Composition of CR 65:
- Cement;
- Mineral fillers;
- Colorant;
- Modifying additives.
Application:
Ceresit CR 65 — this is coating protection for the concrete structures, which can be applied to the following constructs:
- Concrete foundations;
- Concrete and brick walls;
- Technical and fire tanks;
- Pits and technical premises.
Technical specifications of Ceresit CR 65:
The density of mixture, ready for use | 1,8 ± 0,1 kg/dm3 |
Application temperature | starting from +5 up to +30°C |
Water resistance | not less than 1,0 MPa (W10) |
Compressive strength | not less than 20,0 MPa |
Bending tensile strength | not less than 4,0 MPa |
Adhesion strength to the concrete base (adhesion) | not less than 1,0 MPa |
Frost resistance of the hardened solution | not less than 200 cycles (F200) |
Operating temperature | from –50 up to +70°C |
Consumption rates of Ceresit CR 65:
Operating conditions | Required layer thickness in mm | Consumption, kg/m2 |
High humidity | 2 | 3 |
No water pressure | 2,5 | 4 |
By the water pressure | 3 | 5 |
Maximum thickness | 5 | 8 |
The detailed instructions on the arrangement of Ceresit CR 65 can be downloaded, by pressing the link – Waterproofing Ceresit CR 65 – instructions for its use and application.
Bergauf hydrostop
Bergauf hydrostop is a mixture for waterproofing of the coating type
Composition:
- Cement binder;
- Fractionated sand;
- Mineral fillers;
- Modifying polymer additives;
- Hydrophobic additives.
Application:
Material Bergauf hydrostop is perfectly suitable for protecting the following bases:
- Masonry;
- Concrete;
- Reinforced concrete.
hydrostop can be applied to walls, floor and ceiling with high and normal humidity.
Technical specifications of Bergauf hydrostop:
Application temperature | from +5 °С up to + 35 °С |
Water resistance | W8 |
Compressive strength | not less than 30,0 MPa |
Bending tensile strength | not less than 6,0 MPa |
Adhesion strength to the concrete base (adhesion) | 1 MPa |
Frost resistance | F 100 |
Operating temperature | from – 50 °С up to + 70 °С |
Consumption rates of Bergauf hydrostop:
Operating conditions | Required layer thickness, mm | Consumption, kg/m2 |
Standard | 1 | 1,8-2 |
“Straining” NC cement
A mixture, intended among other things for works, related to waterproofing of various constructs. NC cement is applied both on a stable and dynamic base with movement and vibration.
Composition:
- Cement;
- Cementing component;
- Mineral filler;
- Chemical additives.
Application:
The material is suitable for application to the surface of the brick, concrete, and even masonry.
It is used by the arrangement of the protective layer of the following structures:
- Swimming pools;
- Basements;
- Tanks for various purposes;
- Walls;
- Foundations.
Technical specifications of NC cement (“Straining”):
The density of mixture, ready for use | 1900 – 1950 kg/m3 |
Application temperature | from +5°C up to +25°C |
Water resistance | W6 |
Compressive strength | not less than 20,0 Mpa |
Adhesion strength to the concrete base (adhesion) | 0,5 MPa |
Frost resistance of the hardened solution | F50 |
Operating temperature | from -35°C up to +40°C |
Consumption rates of cement NC:
Operating conditions | Required layer thickness, mm | Consumption, kg/m2 |
Standard | 10 | 18-20kg |
GLIMS WaterStop
Coating waterproofing GLIMS WaterStop – this is an ecologically clean material, designed for installation on various static bases that are not subject to vibration and strong dynamics.
Composition:
- Cement;
- Cementing component;
- Mineral filler;
- Chemical additives.
Application:
glims WaterStop can be applied on the concrete and other bases in such a structure as:
- Basements;
- Walls
- Foundations;
- Pits;
- Facades;
- Tanks;
- Swimming pools;
- Wet areas of technical and residential premises.
Coating glims can be applied to concrete, stone, and brick foundations, aerated concrete, asbestos cement slabs, moisture-resistant drywall, and plasters.
Technical specifications of glims WaterStop:
Application temperature | from +5°C up to +25°C |
Water resistance | W7 |
Compressive strength | not less than 2,5 Mpa |
Adhesion strength to the concrete base (adhesion) | 0,9 MPa |
Frost resistance in cycles | 75 |
Operating temperature | from -35°C up to +40°C |
Consumption rates of glims WaterStop:
Operating conditions | Required layer thickness, mm | Consumption, kg/m2 |
Standard | 2-3 | 3-3,5 |
Weber
Materials under the trademark weber are produced on the territory of the Russian Federation in 4 factories throughout the country. At present weber produces a large number of different coating building mixes, designed, among other things for high-quality waterproofing. One of the most popular materials is a waterproofing mixture Weber vetonit tech. 930.
Application of weber product:
- Weber vetonit can be suitable for protecting the following elements:
- Walls;
- Basements;
- Foundations.
Consumption rates of waterproofing Weber vetonit tech. 930:
Operating conditions | Required layer thickness, mm | Consumption, kg/m2 |
Standard | 2-3 | 3,2-3,8 |
The detailed instructions on the arrangement of Weber dry ss-10 can be downloaded, pressing the link
HydroPaz
HydroPaz is a high-quality polymer cement waterproofing from the German manufacturer of industrial waterproofing company HYDRO.
HydroPaz is a premium material capable of protecting both concrete and brick foundations from penetration and exposure to water for at least 30 years. The unique composition of HydroPaz allows it to withstand both positive and negative water pressure, which makes it possible to apply the material both on the positive side and on the negative side.
Application:
The material is used for waterproofing of all concrete and brick structures as well as for insulation of FBS (Solid Concrete Blocks) blocks and other bases.
Technical specifications:
The density of the mixture, ready for use | 1,9 ± 0,1 kg/dm3 |
Application temperature | from +1 up to +40°C |
Water resistance | not less than 1,2 MPa (W12) |
Compressive strength | not less than 25,0 MPa |
Bending tensile strength | not less than 6,0 MPa |
Adhesion strength to the concrete base (adhesion) | not less than 1,0 MPa |
Frost resistance of the hardened solution | not less than 300 cycles (F300) |
Application temperature | from –60 up to +80°C |
Comparison table between materials
HydroPaz | Ceresit CR 65 | NC Cement “Straining” | glims WaterStop | Weber vetonit tech. 930 | Bergauf hydrostop | |
Consumption, kg/m2 | 2-4 | 2-3 | 3-4кг | 3-3,5 | 3,2-3,8 | 1,8-2 |
Water resistance | W10 | W10 | W6 | W7 | W6 | W8 |
Negative pressure operation | Available | Not available | Not available | Not available | Not available | Not available |
Application temperature | from +1 up to +40°C | from +5°C up to +35°C | from +5°C up to +25°C | from +5°C up to +25°C | from +5°C up to +35°C | from +8°C up to +40°C |
Coefficient of elasticity and stretching | 6,0 MPa | 4,0 MPa | 1,0 MPa | 2,0 MPa | 2,0 MPa | 4,0 MPa |
Rating of builders | 5 | 4 | 1 | 3 | 3 | 2 |
Customer rating | 5 | 5 | 1 | 2 | 2 | 2 |
Prices for materials and works
Below are the average prices for the most popular materials, including coating. The prices of the materials may vary depending on the exchange rate and seasonality.
The prices for the arrangement of works take into account the standard complexity of execution.
If you need to find out the exact prices of a particular waterproofing arrangement and you want to get a detailed estimate for all the work and materials, then you need to send a request to or call an engineer to your facility so that he can make a plan for the necessary work and recommend the right materials and technologies for their installation for your facility and situation.
Prices for Cementitious waterproofing products
Name | Price for 1kg in $ | Price per 1m2 in $ |
Ceresit CR 65 | 83 | 349 |
Bergauf hydrostop | 71 | 242 |
Cement NC “Straining” | 49 | 296 |
glims WaterStop | 67 | 334 |
Weber vetonit tech. 930 | 78 | 409 |
HydroPaz | 191 | 573 |
Prices for Cementitious waterproofing application
Work description | Unit of measurement | Price in $ |
The arrangement of coating single-component cement-based waterproofing | m2 | starting from 8 |
The arrangement of cement-mineral double-component waterproofing | m2 | starting from 10 |
The arrangement of penetrating cement compositions | m2 | starting from 8 |
Spraying of cement and plaster insulation | m2 | starting from 10 |
Base preparation | m2 | 3 |