Table of Contents
-
Types of waterproofing for the pool
- Liquid waterproofing
- Coating waterproofing and mastics
- Liquid rubber for pool waterproofing
- Double-component waterproofing
- Penetrating waterproofing for the pool
- Pool waterproofing membrane
- Liquid glass
- Cement waterproofing and Polymer cement mixtures
- Polyurethane systems
- What is the best waterproofing material for swimming pools to choose?
- Waterproofing of the concrete basin bowl — detailed instructions and features of waterproofing of individual nodes
- Prices for a pool waterproofing arrangement
- Pool leaks: pool waterproofing repair methods
- Waterproofing of the pool with your own hands: How to make properly the waterproofing of the pool
- Pool waterproofing works – tutorial video
One of the main issues at the stage of arrangement of any pool is its waterproofing. It is extremely important to protect the structure from cracks, and leaks, as well as from the formation of areas of dampness and mold, and thereby ensure the absolute safety of the water filling the pool.
In modern construction, the use of a variety of technologies for waterproofing pools is common, as well as the use of various materials, each of which has its own characteristics. How, with the use of what compositions and under what conditions the waterproofing of the pool is carried out, and will be discussed in this article.
Types of waterproofing for the pool
To date, there are several types of waterproofing used to protect swimming pools from various damages. Each of them has its own positive and negative sides, as well as unique operating conditions suitable for some territories and unsuitable for others. Let’s look at the most common types of waterproofing pools in more detail.
Liquid waterproofing
Liquid materials for waterproofing swimming pools are often used in modern construction. Such compositions are characterized by high elasticity, excellent hydrophobic properties, as well as high strength indicators. Moreover, waterproofing with liquid materials reliably tolerates significant temperature changes and retains its properties both in warm and cold seasons.
The described materials include, first of all, liquid rubber, polyurea, and polyurethane compounds. These compositions are excellent for the treatment of swimming pools and are used in all regions of our country. However, each of these materials has its drawbacks. Rubber, for example, does not withstand UV exposure. Let’s talk in more detail about the weakness of these materials a little later.

Advantages of liquid materials:
- Full adhesion to the base;
- No seams;
- The ability to apply some materials by spraying;
- Long service life
Coating waterproofing and mastics
Another standard technology of hydrophobic treatment of swimming pools is considered to be coating waterproofing and the use of mastics. Plastering materials are characterized by elasticity, and they are also very easy to apply to the work surface. The application of paste-like compositions is carried out using a roller or a spatula: the material should be evenly distributed over the surface and then wait for it to harden.
The obvious advantages of coating compositions can also include:
- easy of their repair
- the ability to easily distribute materials in hard-to-reach and uneven places, such as corners, protrusions, and other elements.
- 100% adhesion (adhesion) to the base
- absence of seams and joints.
The coating materials include
- Polyurethane mastics
- Bitumen mastics
- Cement-based compositions
It is important to understand that not all coating and liquid compositions are suitable for finishing waterproofing of swimming pools, since many of them do not have resistance to ultraviolet radiation. If such protection of the structure is necessary, you should carefully study all the compositions and choose exactly the one that suits you in terms of performance characteristics.

Liquid rubber for pool waterproofing
Copes well with the task of protecting the pool structure from leaks and other damage and such material as liquid rubber. It is a mastic of bitumen-polymer composition, which is evenly distributed over the surface using a brush, roller, or sprayer.
The use of liquid rubber allows you to get a seamless coating that does not diverge at the seams like other materials, and therefore perfectly protects the pool structure from moisture. In some cases, builders make a choice in favor of complex waterproofing, combining the use of liquid rubber and hydrophobic film.
Calcium chloride is added to its composition for fast and high-quality solidification of the material, which accelerates the solidification process. The effect of the substance is explained by the fact that liquid rubber has an aqueous base, which needs to be removed from moisture for the composition to solidify as soon as possible. The result is a durable but at the same time quite elastic coating.
The only drawback of liquid rubber is its low resistance to UV radiation. This feature does not affect the material covering the bottom, since it is additionally protected by a thick layer of water filling the pool. However, the layers of liquid rubber located on the surface are capable of cracking and collapsing under the influence of sunlight.
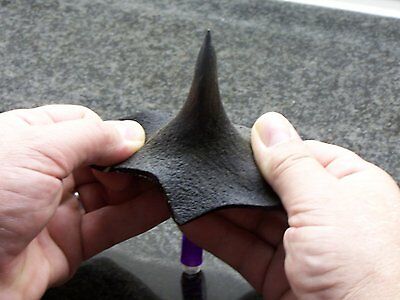
Double-component waterproofing
Waterproofing of swimming pools today is also often carried out using double-component hydrophobic materials. Their main feature is that they include two components. Today there are many double-component materials on the market with different characteristics and components.
Double-component materials are:
- Based on polyurethane;
- Based on cement;
- Based on bitumen;
- Based on polyurea.
Double-component compositions are delivered to the construction site in the form of several buckets with various components or in the form of bags filled with a dry mixture (polymer-cement compositions), and large cans with emulsion.
For example, polymer-cement double-component compositions consist of a dry mixture based on cement, quartz filler, and polymers and a liquid part represented by an emulsion of various polymers. Each bag contains from 22 to 28 kg of the mixture, and from 8 to 10 liters of the liquid component, are transported in cans. Preparation of the composition is carried out immediately before the start of the working process. Immediately after the preparation, the elastic material is evenly distributed over the base. The solution obtained after mixing the two components is distributed over the work surface using a spatula, roller, or brush.

Penetrating waterproofing for the pool
The main feature of waterproofing of penetrating type is that such materials penetrate deep into the pores of the concrete coating and reliably clog them, thereby preventing moisture from entering deep into the base. Due to the addition of polymeric substances to the compositions under consideration, their penetrating power increases to a depth of 20-30sm.
The use of such compositions allows not only to protect the pool structure from moisture but also to increase the frost resistance of concrete, as well as prevent the formation of damp and mold areas on the surface of the pool bowl or in its depth.
However, it is best to entrust the distribution of the penetrating mixture over the work surface to professionals. This is due to the fact that such material is quite difficult to apply, and special difficulties arise with the processing of joints, seams, and areas of connection of pool equipment.
You can read more about penetrating compounds in the article – “Penetrating waterproofing: A detailed description of its work on concrete, types of materials and application technologies“.

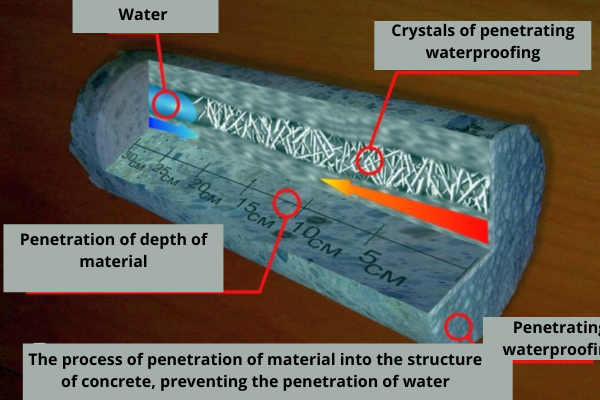
Pool waterproofing membrane
To protect the pool structure from various damages, the use of film membranes is also common. The most popular option is a membrane based on polyvinyl chloride or PVC. It is not difficult to lay it on the surface with your own hands, however, for monolithic permanent structures, it is recommended to consider another waterproofing option.
The main advantage of the film is its excellent hydrophobic properties, resistance to mechanical damage, the ability to tolerate temperatures from -50 to +80 degrees Celsius, as well as elasticity, that is, the ability to “adapt” to any complex or imperfectly even shape of the base.
In any hardware store, you can find a huge variety of waterproofing films: they are represented by numerous colors, drawings, and patterns. Also, the films differ in density, so they can be selected for absolutely any design. Such a hydrophobic material will not only protect the structure from moisture but also decorate the pool bowl.
You can learn more about membranes and their properties in the following articles:
- Roll waterproofing arrangement with detailed installation instructions
- Membrane waterproofing: Types of materials and methods of their arrangement

Liquid glass
Another material — liquid glass, or sodium silicate – is considered one of the methods of waterproofing the pool. It is an aqueous solution with the addition of an acrylic-based polymer, which provides a stable and very durable coating on the working surface. The water component of the material allows it to penetrate into the pores of the concrete base of the pool and securely close them.
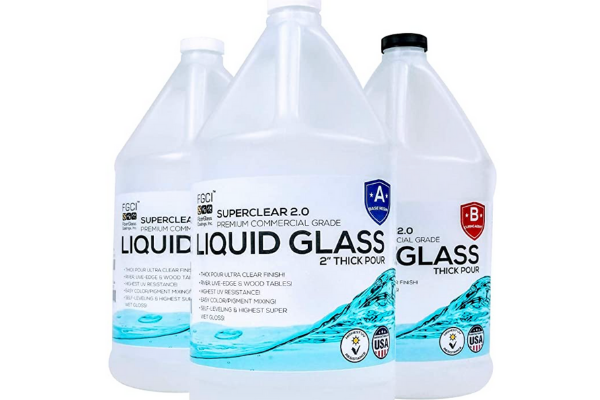
The liquid glass coating is resistant to temperature changes. And its main drawback is that such waterproofing cannot interact with water for a long time. Therefore, it is not recommended to leave the pool covered with liquid glass without liquid: this can lead to cracking and destruction of the sealing compound.
Waterproofing of liquid glass is quite difficult to apply to the surface, so it is best to trust the process of processing the pool with such a material to professionals. The finished solution hardens after a short time after mixing, so it should be prepared in small quantities and quickly and, most importantly, properly distributed over the surface.

Cement waterproofing and Polymer cement mixtures
In hardware stores, you can also find mixtures made on the basis of cement and sand, standard or with the addition of various polymers. Such compositions perfectly withstand significant temperature changes, have a high degree of adhesion to most surfaces, and are also characterized by high resistance to mechanical loads and other influences.
Cement and polymer-cement compositions are excellent for waterproofing both outdoor and indoor pools. However, they also have a significant drawback: such materials are not characterized by elasticity, which is why cracks and pores often form on their surface. The solution to this problem can be the installation of silicone seams, which will take the load when stretching or compressing the waterproofing material.
Among the polymer-cement waterproofing compounds, it is possible to distinguish products from some manufacturers that differ in strength and reliability and are therefore very popular in the construction market.
- Such compositions, for example, include Ceresit CR 166 mixture, which is made on the basis of two components – a dry cement mixture and a liquid polymer emulsion. This composition is characterized by high elasticity, vapor permeability, frost resistance, resistance to chemicals, for example, salts and alkalis, environmental safety, and ease of installation. This material is able to compensate for cracks by opening up to 3/4 mm. Today Ceresit is used for processing structures for various purposes, including for internal and external waterproofing of swimming pools.
- It is also worth highlighting the products manufactured by Mapei, which is famous for its single-component and double-component mixtures and, of course, waterproofing tapes. The most popular formulations, which include two components, have a characteristic gray color and a pasty consistency. They are distributed over the surface using a roller or a spatula, and the work should be completed within 60 minutes: this is how long the viability of the finished mixture is.
- Litokol company produces single-component mixtures distributed over the base in several layers, as well as Coverflex compositions that do not require the installation of a reinforcing frame and reliably protect the structure from vibrations. Coverflex is made on the basis of cement and liquid acrylic emulsion, which, when mixed, give an elastic solution.
- Another popular product is Osmogrout, which is a composition of a penetrating type. It protects the structure not only from the effects of liquid and hydrostatic pressure but also from the negative effects of various chemical elements, such as sulfates and chlorides.
- Another well-known manufacturer, which should not be mentioned when listing the best suppliers of high-quality waterproofing – is the Hydrocompany. It is engaged in the production of various materials, including penetrating, liquid, injection, polymer, and many others, and each of them is characterized by a high degree of adhesion to the concrete base of the pool bowl. Hydro products perfectly tolerate temperature changes, are resistant to ultraviolet radiation, have almost 100% adhesion to the concrete base and resistance to chemicals, and are also characterized by high maintainability.
You can read more about cement waterproofing in the article – “Cement-based waterproofing: Features, types, and methods of its application“.


Polyurethane systems
Polyurethane systems are one of the most reliable and high-quality waterproofing materials. Polyurethane mastics have the following properties:
- Complete absence of seams and joints;
- Full-fledged adhesion to concrete and metal base;
- High elasticity;
- UV resistance – thanks to which the material can be applied as a finishing coating;
- Resistance to mechanical damage;
- The ability to collate in any color according to the RAL catalogue, for example, blue or full blue characteristic of swimming pools;
- The ability to apply a polyurethane coating by spraying.
You can read more about polyurethane systems in the article – “Polyurethane waterproofing“.





What is the best waterproofing material for swimming pools to choose?
The answer to this question lies in the task that the waterproofing coating should perform and the place in which it is located. Further, we will consider some features of waterproofing and recommendations of materials suitable for use in these conditions.
1. Negative water pressure:
If the pool bowl is already standing and there is no access from the outside to it, but at the same time moisture and groundwater from the outside gets inside the pool, then it is recommended to choose waterproofing compounds that work on negative water pressure (from the outside to the inside). Thus, they will not only be able to prevent water from leaving the pool, but also prevent external waters from entering it.
Materials, that cannot withstand negative pressure:
- Bitumen-based waterproofing
- Polyurethane systems
- Surfaced and pasted membranes
- PVC membranes
- Polyurea
Recommended use:
Materials, that can withstand negative pressure from the outside to the inside:
- Cement waterproofing – For example, materials of the HydroPaz series from the German company Hydro.
2. The waterproofing material will serve as the finishing coating of the pool bowl:
In such a situation, it is necessary to use waterproofing, which will have good resistance to UV sunlight. In the absence of such resistance, when the water is drained in the pool, the protective coating may crack or lose its original appearance.
Recommended use:
Materials resistant to UV radiation:
- Polyurethane waterproofing – For example, materials of PolyFlex series from the German company Hydro.
- PVC and EPDM membranes – For example, Sikaplan WT 4220-18H.
Waterproofing of the concrete basin bowl — detailed instructions and features of waterproofing of individual nodes
The technology of the waterproofing coating of concrete pools is different. One is used in the construction of a swimming pool on the street, and the other in the construction of a swimming pool indoors by deepening in the ground.
If the pool is being built on the street, it is important to provide both external waterproofing of concrete walls and internal. External waterproofing is needed to protect concrete from the effects of water and moisture in the ground. In the absence of concrete waterproofing, water and moisture in the ground (rain, high water or groundwater) will be absorbed into the concrete and gradually destroy it, not to mention that this water can penetrate inside the made pool.
If the pool is carried out by the method of deepening in an existing visit, then, as a rule, waterproofing from the outside is not provided and, in this case, it will be carried out only from the inside of the concrete structure.
You can find out about the impact of water on concrete, why it needs to be protected from it, and about suitable materials for this in the article – “Waterproofing of concrete and how to make it: Types of materials and methods of installation“.
Let’s talk a little more about the stages of the internal and external waterproofing of the pool bowl:
- A pit should be dug on the site and prepared for the arrangement of the pool. The first stage of protecting the future pool from water is the arrangement of a reservoir drainage system (if we are talking about deepening indoors). If the pit is being dug on the street, then it is recommended to add ring drainage to the reservoir. The main task of the drainage system is to weaken the water pressure on the waterproofing so that it will last 5 times longer than under constant water pressure.
- Further, during construction, geotextile, formwork, and reinforced frame are installed.
- It is very important not to forget to install a special swelling cord (bentonite) in the reinforced frame at the locations of future cold joints and concrete joints. It will serve as waterproofing joints and seams.
- It is preferable to fill the concrete basin of the pool with high-grade concrete and with the addition of various hydrophobic additives.
- After the concrete has completely dried and shrunk, it is necessary to proceed with its waterproofing, both from the outside (if there is access), and from the inside.
- When installing external and internal waterproofing of the pool bowl, it is recommended to use seamless polymer-cement or polyurethane materials that form a solid, even coating that does not include seams or other joints and has 100% adhesion to the base.
The scheme of the complex waterproofing of the pool

Waterproofing of pool seams
An extremely responsible waterproofing process is the waterproofing of joints, embedded elements, communication inputs, and seams inside the pool. This sealing is carried out at the stage of concreting the future walls of the pool. Sealing of all joints and cold joints of concreting is carried out using materials such as hydrophilic rubber in the form of a swelling bentonite cord. The bentonite cord is mounted on a reinforced frame in the places where future cold joints and concreting joints pass. The installed cord swells upon contact with water so that water and moisture do not pass.
You can read more about the waterproofing of joints in the article– “Sealing and waterproofing of joints – concrete, cold and deformation“.


Waterproofing of the pool under the tile
The technology of waterproofing the pool under the title implies the internal treatment of the bowl with the help of coating materials. First, the base is thoroughly cleaned, leveled, and prepared for the application of a hydrophobic composition. It is also important to clean the work surface so that it will acquire a characteristic roughness, providing a high degree of adhesion of the waterproofing material to the base.
Then a primer is applied to the surface, and after it dries, the coating waterproofs itself. After the composition has solidified, it is important to check the surface for defects and, if they are found, immediately compensate for them. Upon completion of the main stages of the work, the matter remains small: you need to buy a tile you like in a construction store and decorate the pool bowl with it.
The joints between the tiles are most often treated with epoxy-based grout. Such compositions are characterized by resistance to chemicals and high mechanical strength. Moreover, they are able to retain their color throughout the entire period of operation. Grout compositions are suitable even for thermal pools and structures filled with seawater.

Waterproofing of the pool from the inside
Waterproofing of the pool bowl from the inside includes the following activities:
- Before starting work, a thorough visual inspection of the pool bowl is carried out. At this stage, it is extremely important to detect any cracks, cracks, and other damages that may be present on the structure. All detected surface defects are immediately filled with sealant.
- Then the base is cleaned so that its surface becomes rough. This nature of the base will ensure its excellent adhesion with other compounds, the application of which involves internal waterproofing.
- A primer or a standard primer is evenly distributed over the rough surface of the base.
- At this stage, waterproofing is applied. As a rule, waterproofing is applied in 2-3 layers, and if we are talking about liquid or coating materials, then each subsequent layer is laid strictly after the previous one has dried (the solidification time is indicated on the package with the selected composition).
- The last stage of the workflow includes checking the tightness of the applied internal waterproofing by conducting hydro-tests and correcting all defects.
- In the final stage, if necessary, the final finishing of the structure is carried out, after which it will be possible to start its direct operation.

In the matter of choosing waterproofing for the pool bowl, it is best to rely on high-quality materials, even if such processing of the structure will not be the cheapest. Otherwise, you risk significantly reducing the service life of the pool.
Waterproofing of outdoor swimming pool
Structures, located outdoors are exposed to a more serious environmental impact than, for example, indoor swimming pools. It is important to understand that with the outdoor location of the pool, both the structure itself and the waterproofing material are regularly exposed to ultraviolet radiation, temperature stages, chemicals, and many other factors. Therefore, the choice of hydrophobic compounds should be approached very carefully, and it is also important to remember that street structures are necessarily treated both from the inside and outside.
For example, liquid rubber, which cracks from exposure to ultraviolet light, it is not suitable for processing the inner bowl of an outdoor pool. The use of cement mixtures will also not be the last solution. It is best to make a choice in favor of polyurethane compounds, even if they cost a little more. If the pool is planned to be drained for the winter period, then liquid glass should not be used as waterproofing, which cracks in the absence of contact with water.
Properly selected waterproofing should meet such requirements as to strength, high elasticity, reliability, excellent adhesion to the substrate, as well as resistance to various influences in the planned operating conditions. Only in the case of a competent choice will the main property of the hydrophobic composition be achieved, namely, confident protection and long service life.
Prices for a pool waterproofing arrangement
The prices listed below can be changed depending on the complexity of the object and other nuances. To accurately calculate the cost, you can contact our estimate department by e-mail or by phone number, specified in the contacts.
Description of work | Unit of measurement | Price in $ |
Works on installation of a rolled surfaced membrane | m2 | starting from 10 |
Works on the installation of a PVC membrane | m2 | starting from 12 |
Works on the arrangement of EPDM membrane | m2 | starting from 13 |
Works on the application of liquid rubber by spraying | m2 | starting from 8 |
Works on the application of liquid rubber manually | m2 | starting from 9 |
Works on the application of penetrating compounds | m2 | starting from 9 |
Services on the arrangement of polymer-cement waterproofing | m2 | starting from 15 |
Works on the application of polyurethane waterproofing | m2 | starting from 15 |
Installation of tanks for swimming pools | m2 | starting from 300 |
Sealing of communication entry points | piece | starting from 150 |
Pool leaks: pool waterproofing repair methods
The way to repair and eliminate leaks in the pool directly depends on how the structure is built, the nature of these leaks, and the causes of their occurrence. Further, we will analyze each type of leak and the method of elimination.
Types of leaks and methods of their repair:
- Cracks in the body of a concrete structure – If there are cracks or microcracks in the concrete bowl, then an injection sealing method should be used to repair them since surface repairs using a hydro seal or an expanding sealant will not fix the situation for a long time. For a full-fledged repair, you need to fill all micro-voids and cavities in the depth of the crack, and this can only be done by injection. Accordingly, the problem area is expanded and cleaned, and a special expanding sealant is compacted there in layers, after which injectors are installed along the perimeter of the crack and the injection compound is injected under pressure.
You can read more about crack sealing technology in the article – “Waterproofing and sealing of cracks in concrete, brick, and other bases“. - Leakage in the locations of cold joints and concreting joints – Seams and joints are the weakest points in any structure and they begin to leak in the first place. For their repair, it is also recommended to use an injection sealing method. The seam should be stitched with a small indenting installation, then the expanding sealant should be sealed in layers, installed along the perimeter of the packer in increments of 20-25sm, and injected so that the waterproofing compound gets into the thickness of the seam, filling it completely.
You can read more about the technology of sealing joints in the article – “Sealing and waterproofing of joints – concrete, cold and deformation“. - Pipe entry points – Another weak point in most structures are the entry points of various communications. It is recommended to repair these places using bentonite cords, sealants, hydraulic seals, and if necessary, injection formulations. When repairing a hydraulic seal, it hardens within three minutes and is characterized by high strength and resistance to hydrostatic pressure, however, this method will not last long without an integrated approach.
You can read more about the technology of sealing the entry points in the article– “Sealing and waterproofing of the entrances of communications to the building“. - Leakage in the body of the concrete bowl – If the pool bowl itself leaks, then the reason lies in the lack of high-quality waterproofing of the surface. If flaws are visible in the waterproofing coating, then they can simply be repaired by installing a patch (if we are talking about a membrane) or a repair compound (if we are talking about coating materials). If it is impossible to identify a specific problem area, it is recommended to completely replace the waterproofing with a more reliable and durable one.





Waterproofing of the pool with your own hands: How to make properly the waterproofing of the pool
To carry out the waterproofing of the pool on their own is most effective with the help of hydrophobic compositions of the coating type. Cement mixtures and polyurethane mastics are common among them, which are characterized by the relative ease of installation and high strength and efficiency. As a rule, roll waterproofing requires much more skills, experience, and the use of special equipment, for example, burners or construction hair dryers.
Step-by-step working plan:
- Choosing the time for work – if the structure is located on the street, then the processing of the structure should be postponed until a sunny day, on which the ambient air temperature will not be lower than +5 degrees Celsius. At a higher temperature, for example, in the summer, work is carried out early in the morning or late in the evening.
- Choosing the right waterproofing system — when choosing, it is necessary to rely on the properties and characteristics of materials, so that they are exactly suitable for your particular structure, purpose, and task.
- Preparatory work – before applying waterproofing, the surface should carefully be prepared: remove all concrete surges, sharp corners, and chips, and clean from dirt and dust.
- Priming the base if necessary – this procedure is done using a specially selected primer or base paint (it has its own for each material).
- Waterproofing application — the main rule when applying is to follow the manufacturer’s instructions clearly. For example, for most of the coating mastics, before applying, there is a mandatory mixing of the mastic, this is necessary so that the material is not soaked with air and is securely connected to the base. A special belt agitator, which can be purchased in most construction stores, copes most effectively with mixing the compositions.
- Upon completion of all mandatory stages of work, if we are talking about coating or liquid materials, they are left to dry, and this, as a rule, takes at least 2 days. And for sections of the structures directly in contact with water, that is, for the inner surface of the pool bowl, it takes at least 5 days. Manufacturers usually indicate the exact waiting time before filling the pool with water in the instructions for use. During this period, it is necessary to limit any loads on the pool structure.
- If the waterproofing does not go as the final coating, then after drying, you can proceed to the final finishing of the pool. It can be decorated with colorful tiles or mosaics. When using tiles, the seams should be rubbed with epoxy grout.
When using a coating waterproofing for most mastics, the following application instructions are suitable:
- The base of the pool bowl, made of concrete, is cleaned and prepared for operation. The surfaces of the wall and the bottom of the structure are leveled, and all cracks, chips, and other damages are covered with a sealant.
- Then the working surface is moistened, and a layer of waterproofing material of the penetrating type is evenly distributed over it. It is important to be especially careful near the seams and at the points of entry of communications. After that, it is necessary to wait for the hydrophobic composition to dry.
- The next step — is degreasing the base. To do this, a solution of a weak acid is distributed over its entire surface and left for about one hour. After this time, the solution is washed off with water, and its residues are removed by adding 4-5% soda solution with calcium.
- The working surface is dried, after which the application of mastic begins in compliance with a thickness of the composition layer equal to approximately 2-3 mm. The vertical sections are isolated using a brush or roller, and the horizontal sections are isolated by a self-leveling method followed by treatment with a needle roller. Such a tool perfectly removes excess air bubbles from the coating.
- After the layer of hydrophobic composition has slightly seized, the second layer of mastic is applied with a thickness of 1 to 3 mm after the first one has dried.