Table of Contents
- What is plaster waterproofing and where can it be applied
- Types of plaster waterproofing and methods of their application
- Methods of applying plaster waterproofing
- Prices for plaster waterproofing installation
- Recommendations on the choice of plaster waterproofing
- Alternatives to using plaster waterproofing
Plaster — is mainly mixtures intended for leveling various surfaces, however, some such mixtures have, in addition to their standard properties, such features as resistance to moisture and water. Such plaster mixtures are called Plaster waterproofing. In fact, such waterproofing can not only level the surface but also protect the base from the impact and penetration of water and moisture.
What is plaster waterproofing and where can it be applied
Plaster waterproofing — is a mixture of waterproofing and water-resistant properties intended for the primary leveling of the base and for applying the final layer. High-quality waterproofing plaster will slow down the rate of destruction of the foundation base or the construction of walls made of concrete or brick, prolonging its service life.
For the most part, a plaster system with waterproofing properties is used to strengthen the surface (most often the foundation). However, there are some types of these systems that are used for other purposes, for example, sound insulation and thermal insulation, mixtures that isolate harmful substances are less common.
Where is plaster waterproofing used?
Water-resistant plaster can be used on such structures as:
- Foundations;
- Basements/Foundation walls;
- Swimming pools;
- Floors;
- Concrete tanks.
Plaster insulation is excellent for covering rooms exposed not only to positive water pressure but also to the negative effects of moisture, for example, from the outside to the inside. Compositions that withstand negative water pressure are often needed in cases where there is no access to the room from the outside, but it is possible to perform waterproofing only from the inside, for example:
- Basements of private houses, old mansions, business centers;
- Walls of residential buildings, socle, and technical floors;
- Foundation walls made of brick or concrete;
- Underground structures;
- Various tanks.
Plaster waterproofing of the foundation and walls
For foundations and walls of foundations made of bricks, FBS blocks, or concrete, it is often plaster that has waterproofing properties as a waterproofing material that is used. Basically, these mixtures are used where there is a need for leveling the base or where there is a brick base with numerous seams and irregularities on which other waterproofing systems simply will not fall without prior leveling.
Despite the special waterproofing characteristics of waterproofing mixtures for the plaster arrangement, these mixtures are often used as an auxiliary and additional element for protecting walls and foundations from the effects of water. Accordingly, in most cases, when performing waterproofing of the foundation or construction of basement walls and basement floors, an additional main layer of waterproofing is applied to the plaster that is resistant to water, which will protect the existing underground structure from water penetration.
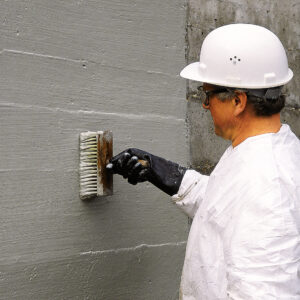
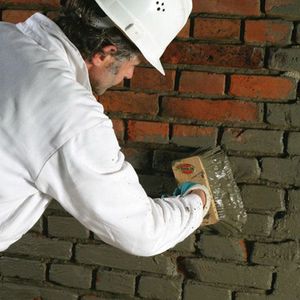
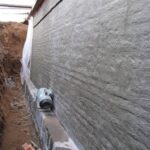
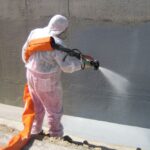
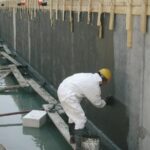
Additional tips on waterproofing underground parts of buildings and structures:
- Horizontal waterproofing of the foundation: The technology of installation and the materials necessary for this.
- Waterproofing of foundation blocks and walls.
- Foundation waterproofing installation: Methods, materials, prices, and recommendations of specialists.
- Waterproofing of basement and house walls from the outside and inside – Methods, materials, prices, and technology.
- Waterproofing of bricks and brickwork.
What is plaster waterproofing made of and its characteristics?
The raw material from which the plaster is made is divided into a binder and auxiliary. The first is actually the basis of the composition, which sets the main properties. Astringent raw materials by their origin can be organic (resins, bitumen, tar) and inorganic (liquid glass, cement) Auxiliary raw materials determine the final properties of the product, changing its main qualities, there are plasticizers and solvents).
Other substances are often added to the composition to give the mixture additional properties. Fillers improve the chemical resistance of the plaster coating and increase the physical characteristics. The fillers are often powders, such as talc, and synthetic fibers. Another group of substances included in the waterproofing is hardeners. Hardeners are used to transfer some substances from a liquid to a more stable solid rate, so they are often used in resin-containing mixtures.
Plaster waterproofing is divided according to its readiness for use into:
- Ready-made– this type can be applied immediately when opening the container, without pretreatment.
- Required preparation – These mixtures cannot be applied to the surface immediately, they should first be prepared, for example, mixed in the right proportion with water or the second component.
Technical characteristics:
Name | Unit of measurement | Characteristics |
Dry mixtures | ||
Consumption of dry mix per 1 mm of thickness | kg/m2 | 0,2 |
Required water consumption for activation | l/kg | 0,15 |
Mortar mixtures | ||
Mobility of the solution | minutes | 60 |
Water resistance | % | 99 |
Ready solution | ||
Waterproof grade | W16 | |
Increasing the grade of concrete in terms of water resistance when applying a layer with a thickness of 4 mm | steps/atm | 2/4 |
Increasing the grade of concrete in terms of water resistance when applying a layer with a thickness of 15 mm | steps/atm | 3/6 |
Compressive strength | MPa | 35 |
Flexural strength | MPa | 9,0 |
Frost resistance | F | 300 |
Frost resistance on contact | F | 50 |
Adhesion strength to concrete | MPa | 2,0 |
Water absorption during capillary suction | kg/m2 per 1h | 0,2 |
Water absorption of the solution after its solidification | % | 8 |
Corrosion resistance | Ph | 4-15 |
View additional specifications
Ready solution | ||
Resistance to acid aggressive environment pH3 | Resistant | |
Resistance to carbon dioxide aggressive environment 80 mg/l. | Resistant | |
Resistance to magnesia 10000 mg/l. | Resistant | |
Resistance to ammonium 2000 mg/l. | Resistant | |
Resistance to sulfate 1000 mg/l. | Resistant | |
Resistance to the effects of petroleum products of 100% concentration (gasoline, kerosene, mineral oil) | Resistant | |
The durability of the coating in a gaseous environment such as hydrogen sulfide and methane | Resistant | |
UV resistance | Not available | |
The coating can be operated at a temperature of | С° | -30 to 150 |
The ambient temperature at which waterproofing plaster can be applied | С° | +5 to +35 |
Application for drinking water tanks | Available |
It is important to note that the above characteristics are a kind of average standard and they may vary depending on the manufacturer and brand of the composition.
Advantages and disadvantages of waterproofing plaster
When choosing this waterproofing technology, you should definitely take into account all the nuances of using this type of compound.
Advantages
- Can be used to level the surface without the need for additional waterproofing;
- Has waterproofing properties;
- Seamless system – the finished coating has no seams and joints, unlike traditional systems of roll waterproofing and membrane waterproofing;
- Saving money on an additional water protection installation.
Disadvantages
- Not all plaster mixes withstand negative water pressure;
- Most plasters with waterproofing characteristics have no resistance to ultraviolet radiation (sunlight), which makes the material unsuitable for final coating when performing external work;
- Not all compositions are resistant to aggressive environments, salts and various minerals in groundwater, which can lead to the destruction of the composition after 2-3 years;
- The low coefficient of elasticity of most plaster systems may lead to the formation of cracks on the completed coating during shrinkage of the foundation of a house or building. It is not recommended to apply plaster waterproofing systems to dynamic nodes that have movement;
- It does not withstand the real flow of water at its negative pressure, mainly in places where there are cracks, cold seams (joint of the slab and the wall), and concreting seams, places of entry of communications. For sealing joints, the installation of waterproofing of the entry points of communications, and waterproofing cracks, it is necessary to use additional waterproofing in the form of suture sealants and injection.
For a more detailed study of the sealing technology of the above nodes, you can read the following articles:
- Sealing and waterproofing of joints – concrete, cold, and deformation
- Waterproofing and sealing of cracks in concrete, brick, and other bases
- Sealing and waterproofing of the inputs of communications into the building
Types of plaster waterproofing and methods of their application
There are many types of waterproofing plaster on the market. For the right choice, it is necessary to have a clear understanding of the task, the features of the project, and the surface on which the waterproofing will be applied.
Important: in order to make your choice correctly, it is recommended to contact a specialized company dealing directly with waterproofing works and having experience working with different materials and systems.
Asphalt plaster waterproofing
Asphalt waterproofing is applied with pastes or mastics in several layers. It is available in cold and hot forms. With hot waterproofing, they work at a temperature of about +160-170 degrees Celsius, and it performs their main task after cooling. Hot asphalt waterproofing is very dense, it can be used even for surfaces with a slope of 45 degrees using an asphalt mortar. Hot waterproofing is more effective and it sets fast enough on the surface.
Cold asphalt waterproofing is applied to the surface in the form of a cold emulsion mass. It is produced with the addition of bitumen, water, and several fillers. Cold waterproofing is applied in three thin layers of 8 mm, at a temperature no higher than 15 degrees. For the drying of cold waterproofing, rain is usually required, as a result of which it takes quite a long time to wait. The coating usually does not last as long as it is hot, but the method of application is undoubtedly much easier and safer.
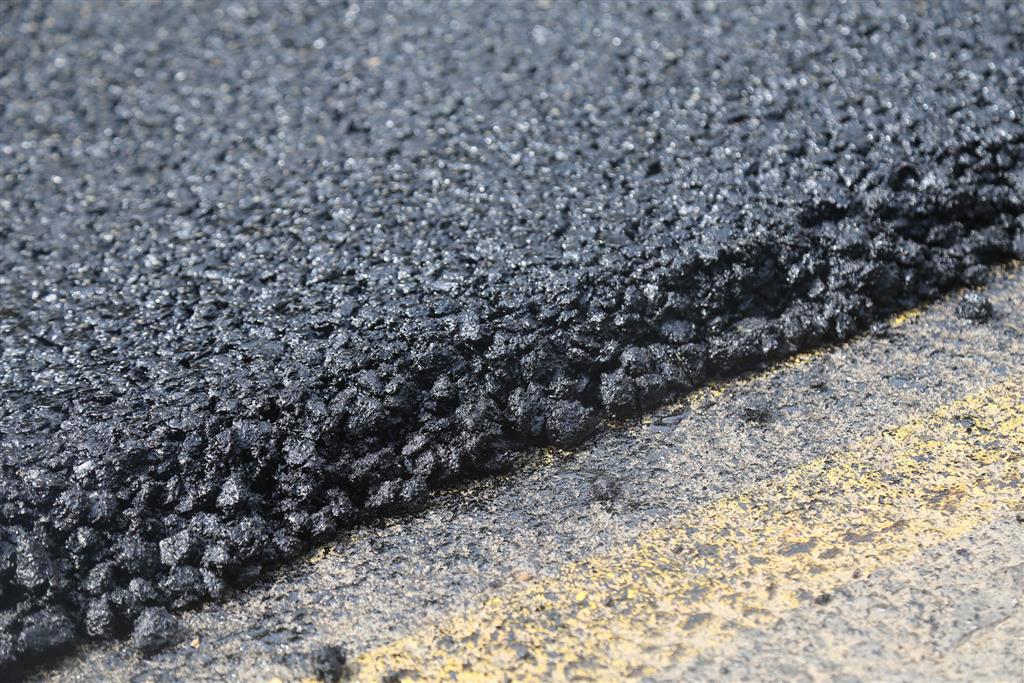
Cast plaster
Cast waterproofing — is the best choice of insulation coating for horizontal surfaces, it evenly covers the entire surfaces, it evenly the entire surface and perfectly protects against the influence of moisture. Cast waterproofing is heated, making the composition thicker, and then poured on a dry surface in two layers, the thickness of the first is about 1 sm, and the second 1.5 sm.
If the insulated surface is wet, the first layer is applied thinner, the first layer is applied thinner, and the thickness can reach up to 6 mm. on top of the case waterproofing, it is recommended to apply another layer of a denser coating, for example, asphalt waterproofing or powdered asbestos. Cast waterproofing is often used in tandem with asphalt waterproofing to protect against the negative effects of road moisture.
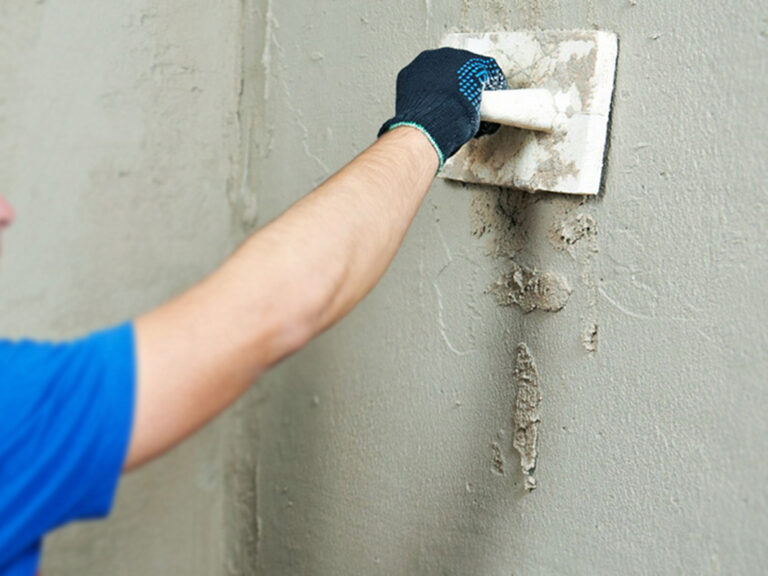
Cement-sand
Cement-sand waterproofing covers underground rooms, basements, and swimming pools. At their core, they are a hardened layer of a solution of sand, water, and Portland cement. To increase efficiency, iron chloride and sulfate-yeast mash are often added to such solutions in an insignificant percentage of cement. Cement-based material with the addition of sand and/or liquid glass is often used for waterproofing foundations and other capital buildings. Cement-sand waterproofing does not leak moisture due to its dense layer.
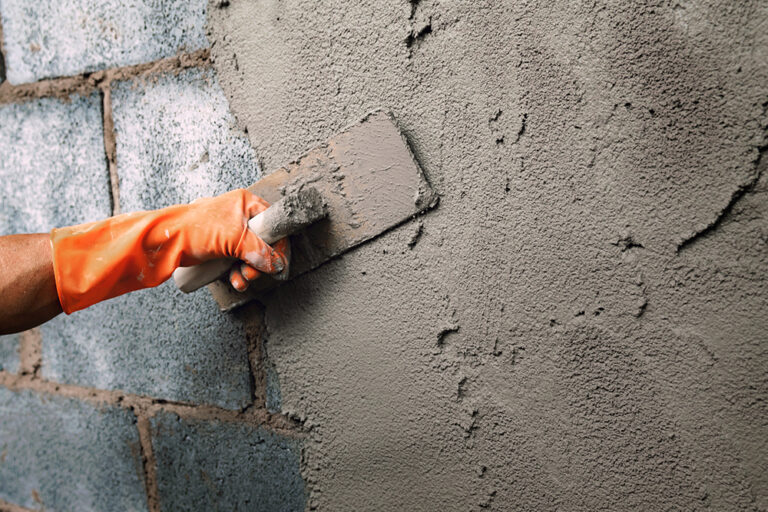
Cement-polymer
These are mixtures based on cement bitumen with the addition of polymers, most of these compositions include latex or liquid glass. Latex gives the mixture more rubber properties, the initial coating is dense and insulates well from moisture and mechanical impact. The material is sometimes applied by spraying. Polymers added to the cement base give the finished coating.
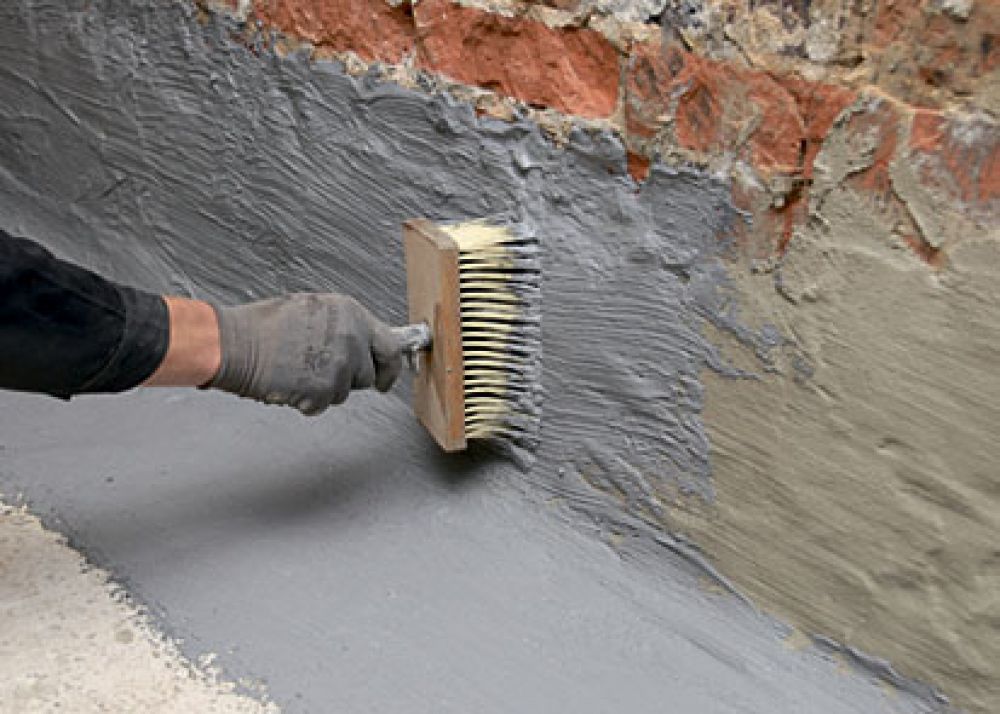
Methods of applying plaster waterproofing
Plaster, including having waterproofing properties, is applied either manually using spatulas and special brushes or mechanized using special spray equipment for this.
Spraying or shotcrete
A number of types of plaster waterproofing are applied by spraying, with this method the surface is covered almost uniformly with small particles of material, as a result, a sealed layer without seams is created.
Before starting work, the surface should be thoroughly cleaned of dust and dirt and the material and equipment should be prepared. Spraying is carried out with the help of pumps and hoses, especially carefully it is necessary to ensure that the latter are not clogged. During work, you need to follow clearly the instructions attached to the material, because the nuances of applying waterproofing from different companies may vary slightly. After applying to waterproof, you need to thoroughly rinse and clean the equipment so that the hose does not clog, and it will work properly next time.
The main advantage of this method — is the speed of application, since the mechanized application can quickly cover large enough areas, unlike manual application, where work is slow.
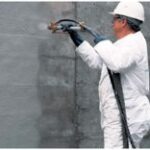
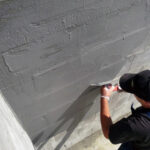
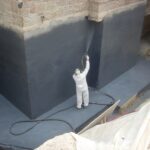
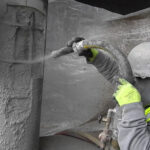
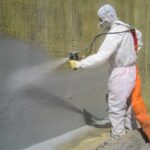
Manually
Applying a plaster mixture that works as waterproofing by hand, allows you to save money because less material is consumed and you do not need to purchase expensive equipment. However, this method requires more time and skills.
The surface cleaning of dirt is slightly moistened with water, only so that the surface is slightly moist, but in no case too wet, this is necessary for better adhesion to the waterproofing material. Further, the dry mixture is mixed with water in the ratio indicated on the package. The future mixture is kneaded with a mixer for 3 minutes, after which the solution is allowed to rest for 5 minutes, then whipped again with a mixer.
The composition for the first layer should be slightly more liquid, then before applying the second layer, it is slightly thickened. The coating is applied with a brush or a spatula in a uniform layer, moving in one direction. The applied material should dry completely, then a second layer is better applied with a spatula because its consistency is already denser, and the movement is made in a perpendicular direction to the application of the first layer.
The top layer should be allowed to dry completely, and at the same time protect from further drying. On very warm days, it is recommended to wet the plastered surface regularly. Exactly one week later, the plaster coating is grouted.
Important: Each composition has its own specific properties and chemical elements added to it. That is why each material has its own detailed application instructions and it is necessary to follow it when performing work.
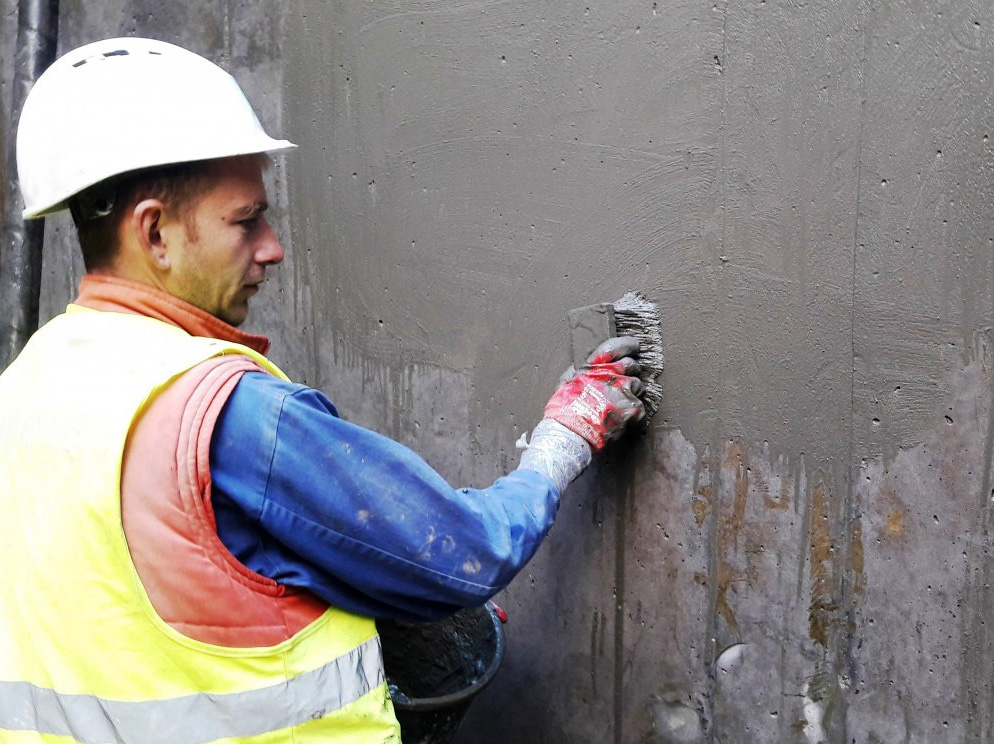
The use of auxiliary materials for high-quality application
Sometimes, when applying various plaster mixtures, reinforcement or reinforced mesh is used. The reinforcement is needed to give the material a more stable state so that the coating does not flow off the surface after application. Glass and synthetic fabrics are most often added to fittings, and plastic and metal nets are also often used.
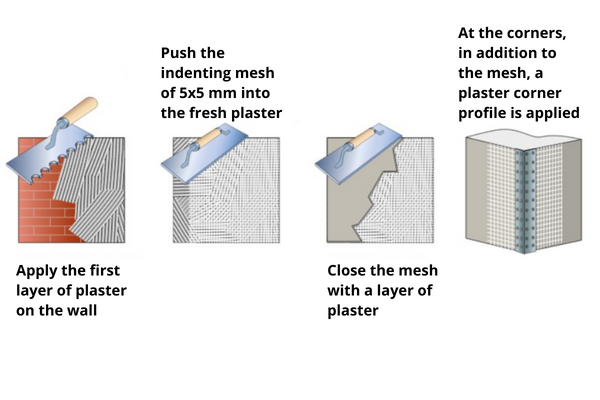
Additional scheme
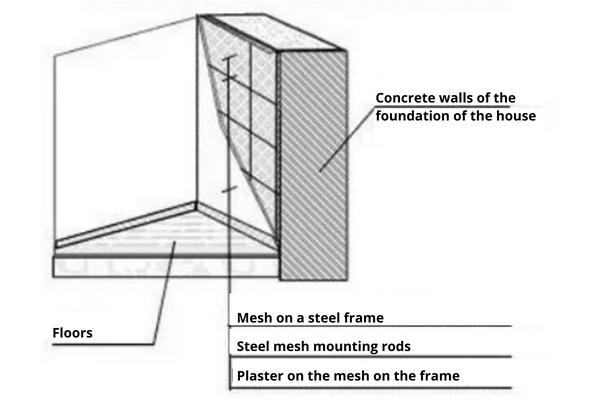
Prices for plaster waterproofing installation
The prices listed below may vary depending on the complexity of the project and the material used in the performance of the work.
Description of work | Unit of measurement | Price per 1m2 in $ |
Preparation of the foundation | m2 | 5 |
Manual application of plaster waterproofing | m2 | 12 |
Mechanized application of plaster waterproofing | m2 | 20 |
Application of polymer-cement waterproofing | m2 | 15 |
Primer of the base | m2 | 8 |
Recommendations on the choice of plaster waterproofing
The modern market is saturated with different types of plaster waterproofing from various manufacturers. In such a situation, you need to learn to choose the best ones. The packaging of the plaster should contain basic information about the use of the product. If possible, it is better to take mixtures that dry quickly without the need for third-party factors.
Outdoor insulation should be resistant to temperature changes and the negative effects of sunlight. Insulating compositions for internal use should not be toxic and should preferably keep negative water pressure (from outside to inside).
Popular materials
Today there are a lot of different plastering materials in the market of different price segments. But there we should not forget that in most cases, buying a cheap waterproofing compound, the chance of getting a low-quality or short-lived one is quite high. By investing in the insulation layer, you are investing in the durability of the structure.
The most popular materials:
- HydroPaz – This is a line of German industrial materials with unique waterproofing properties. These materials withstand not only positive but also negative water pressure, which makes their use invaluable in places where is no access from the positive side. In addition to waterproofing advantages, some products from this line are also supposed for the restoration and repair of brickwork, destroyed sections of concrete, and sections of reinforcement and concrete interface.
- Lakhta – The coating of lakhta turns out to be homogeneous without seams, creating a strong integral layer protecting the bases of the walls from water. Seams and irregularities do not appear even in places of notches and cracks on the insulated surface. Due to the durable coating, the lakhta can be used for waterproofing pools and other depressions filled with water.
Lakhta is quite stable: it is not afraid of chemical exposure or temperature changes, and the coating withstands temperatures from -150 to +200 degrees. Plaster is easy to apply, one layer without reinforcement can reach up to 3 centimeters, and with reinforcement — up to 5, some types from the Lakhta line can be applied even on a wet surface. Lakhta is often used for waterproofing important water structures in which reliability and preservation of integrity are important. - Runit – Runit is a powder with waterproofing properties that do not settle when drying. The composition of runit includes various mineral additives, Portland cement, and mineral filler. Runit is applied to bitumen, stone, and brick surfaces as a final or preparatory layer with a thickness of about 1-1,5 sm. The material is resistant to aggressive environments, mineral oils, and seawater, so it is often treated by marine research buildings.
The surface calmly tolerates sudden temperature changes and can be repeatedly defrosted and thawed. The main advantage of runit is the high degree of adhesion of the insulating coating to the insulated surface, which ensures its durability. Runit can be applied by machine by spraying. Runit, unlike other plaster mixtures, which also perform the role of waterproofing, can be used as a basis for applying any other building materials with inclusions of minerals and polymers. This is due to the low penetrating ability, which makes the material immune to external influences.
Alternatives to using plaster waterproofing
To perform most of the work related to waterproofing, there are alternative solutions that provide no less high-quality protection of buildings and structures from the effects of aggressive environment and water.
The systems, mentioned below for protecting buildings and structures from water, as well as plaster insulation, do not have seams and have 100% of adhesion to the base.
Outside:
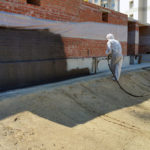
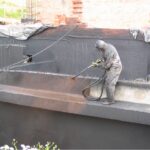
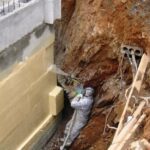
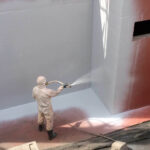
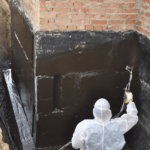
From the inside:
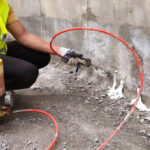
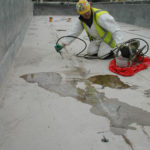
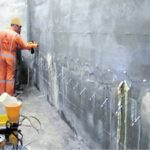
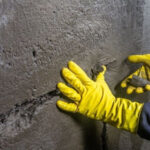
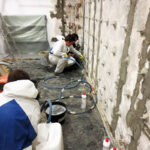