Table of Contents
- What is the waterproofing of the basement for?
- How to make properly the waterproofing of the basement and what should be taken into account at the same time?
- Materials and methods of waterproofing the base
- Prices for work on the waterproofing of the socle
- Restoration waterproofing of the basement
The ground floor is a residential or non-residential premise of a private house or public building, which is located below the planning mark of the ground from the outside to a height of no more than half the height of the basement or floor itself.
Given the fact that the ground floor is partially underground and has direct contact with the ground, it definitely needs high-quality waterproofing.
What is the waterproofing of the basement for?
The basement of a house or building is partially located below the level of the planning ground level, which means that its foundation and walls are exposed to certain conditions such as:
- Groundwater;
- Surface and rainwater;
- Aggressive environments and minerals in water and soil destroy concrete and brick.
In the absence of proper protection, the concrete base and the walls of the basement can, like a sponge, absorb moisture and water from the ground, which, when the climate changes to winter, freezes inside and thaws when the air temperature reaches plus.
Such an impact of climate change can destroy the concrete from which the base is made, from microcracks and pores in it, which will only increase every year.
The impact of the above elements on unprotected concrete, brick, and other foundations can lead to very serious consequences.
The consequences of the lack of high-quality waterproofing of the basement?
In the absence of proper protection of the walls and the basement foundation from the outside, you risk not only losing the possibility of arranging a living space in the basement area, but also the integrity of your home with the ability to safely operate the upper floors of the house.
A list of possible consequences with a description of the cause of each:
- The formation of, – As mentioned earlier, the temperature drop, freezing, and thawing of moisture in concrete destroy it, gradually forming microcracks, which increase in size every year. As a result, the cracks formed may threaten the integrity of the base or the bearing capacity of the structures.
- Leaks – Concrete has pores, voids, and microcracks. Thanks to these weak points, concrete absorbs and then passes water inside the house. The more cracks and voids in the concrete, the more water can enter the room, making it unusable and threatening the safety of the operation of the whole house.
- Efflorescence on the walls – white smudges and stains formed on the surface as a result of exposure to the water together with its salts. Efflorescences destroy the walls gradually forming micro-holes in them.
- Mold-Water is absorbed into the walls, and they are constantly in a wet state, which increases the humidity inside the basement and leads to the formation of various kinds of mold from the inside. Mold grows the surface on the surface and under the finishing elements and can spread over long distances from its hearth. The spread in socle and in the house is unsafe for human health and can lead to poor health, prolonged illness, and hospitalization.
- Fungus– Fungus, like mold, is formed due to high humidity and threatens human health.
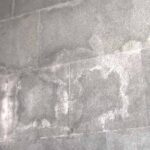
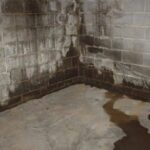
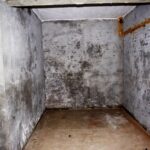
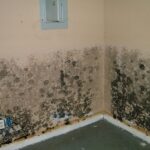
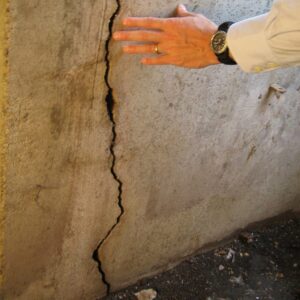
How to make properly the waterproofing of the basement and what should be taken into account at the same time?
If you follow all design and construction standards, then the most correct solution is to make vertical and horizontal waterproofing of all underground parts of the building, including the socle, even at the stage of construction of a house or an administrative building.
The waterproofing installation at the construction stage protects walls, slabs, and foundations from the outside, preventing water and moisture from influencing these structures.
Important: To order waterproofing services for the basement, socle, and structures, located underground, it is only from trusted companies with many years of experience and services, related to the protection of the basement from water, since an error in choosing a suitable waterproofing coating or during its installation can cost you expensive, in terms of not only financial losses but also in terms of the destruction of the house or building itself, by the formation of cracks in the bearing walls of the basement.
Waterproofing of the base outside
To keep the basement in a serviceable condition, a waterproofing coating should be applied to all parts of the floor below ground level, regardless of the presence or absence of groundwater around the house or structure.
Elements of the basement structure subject to waterproofing:
- Foundation – Both slab and ribbon foundations should be protected from water.
- Walls – The part located underground should be protected from water, regardless of the material used for its construction (concrete, FBS blocks, or brick). When installing waterproofing walls, the protective layer should be raised at least 20-30 sm above the design ground level.
When installing insulation from the outside, it is necessary to take into account vertical and horizontal waterproofing.
Vertical waterproofing of the base
Vertical waterproofing is applied to the vertical parts of the basement foundation.
Vertical protection should be applied to the vertical part of the monolithic slab foundation and the vertical of the ribbon foundation.
Monolithic walls, as well as walls made of various types of blocks, should also be protected from contact with water and other minerals.
The scheme of applying vertical waterproofing:
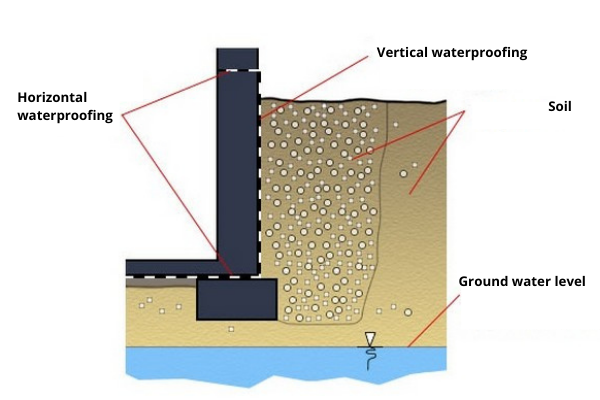
You can learn more about vertical protection in the article – “Vertical waterproofing”.
Horizontal waterproofing
Horizontal waterproofing is applied to the horizontal surface of the foundation and serves as a cut-off between the foundation and the future walls of the basement. It is thanks to the cut-off that moisture and water absorbed into the foundation will not be able to capillary climb the walls and exit from the inside of the basement in the form of a wet spot from the inside or a leak.
Monolithic slab – Horizontal insulation is applied externally in 2 contours, on the concrete preparation and on the slab itself after its insulation.
Ribbon – When waterproofing a ribbon structure, insulation is applied to the sole of the ribbon base, and then to the horizontal surface of the completed ribbon as a cut-off waterproofing (see diagram below).
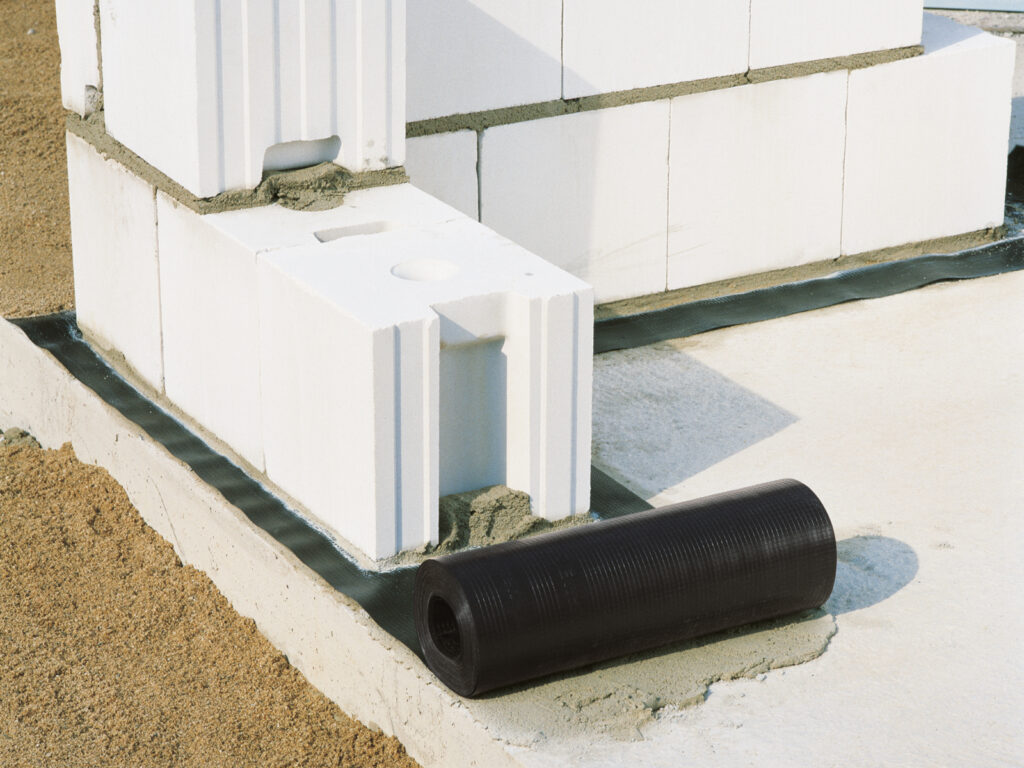
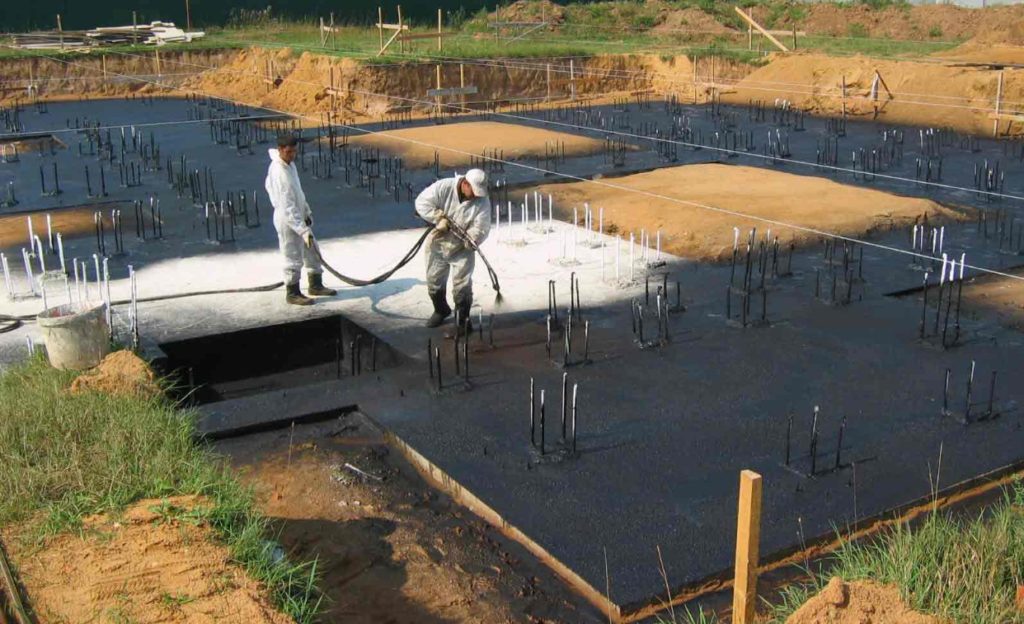
Scheme of application of horizontal waterproofing:
Ribbon foundation:
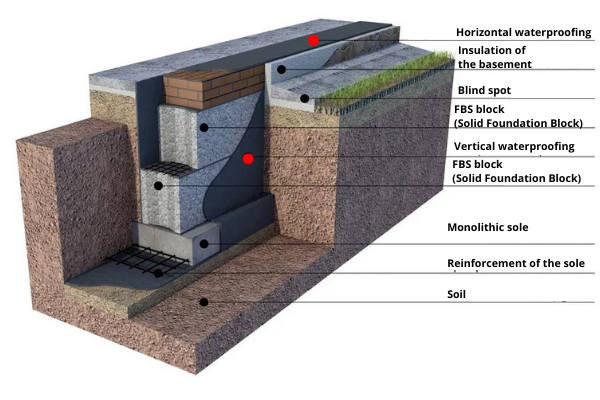
The scheme of the waterproofing installation on the horizontal base of the ribbon foundation
Slab monolithic foundation:
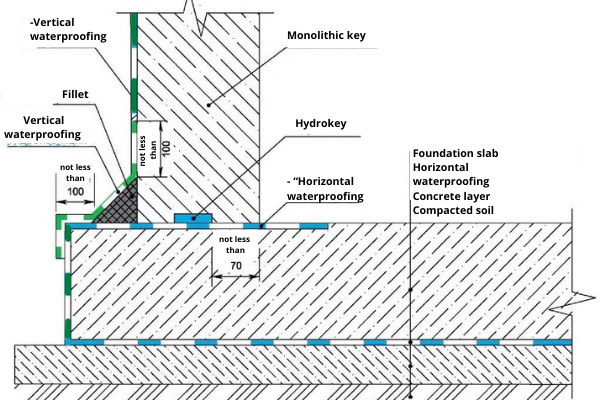
More information about horizontal protection can be found in the article – “Horizontal waterproofing”.
Waterproofing of the basement from the inside
Waterproofing from the inside of the basement is recommended in 2 cases:
- On from inside a building or house;
- A private country house or an administrative building has been built and there is no way to dig out the structure and make waterproofing from the outside.
If it is necessary to perform work related to insulation from the inside of the base, it is best to use injection waterproofing. When injected, polyurethane resin of different viscosity and expansion coefficient is injected under pressure into the body of the structure or existing seams, filling all the pores and voids in concrete, brick, and other substances, making them waterproof.
The scheme of injection waterproofing:
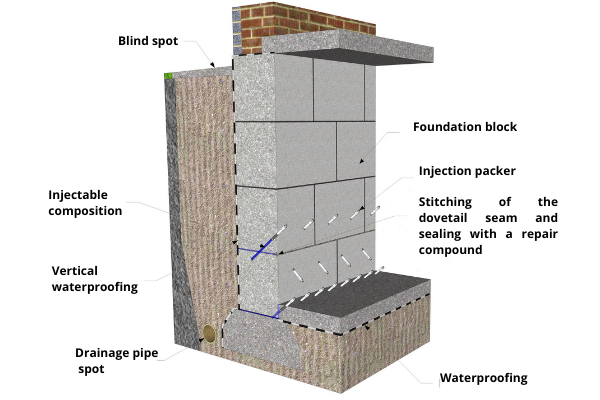
Materials for insulation of the base from inside:
- Injection waterproofing;
- Polymer cement waterproofing working on negative water pressure;
- Penetrating compounds.
Important: When using penetrating compounds, it is necessary to consult with a specialist in the field of waterproofing, since penetrating compounds do not work in all cases and not on all grounds.
You can read more about the work from the inside in the article – “Waterproofing of the basement from the inside. Methods, materials and stages of works“.
Materials and methods of waterproofing the base
As mentioned earlier, the most correct way to insulate the basement is to do all the work outside the house. When performing work outside, the work producer faces a difficult choice of methods, technologies, and materials with which to perform waterproofing of the basement of the house.
Coating mastics
The coating material includes a fairly large palette of various mastics applied to the surface by a coating method using a brush or roller. Coating materials differ in their characteristics and components.
The main types of coating mastics:
- Bitumen – The main active substance in such mastics will be modified bitumen with various polymer additives. Bitumen coating compositions are in great demand and are widely used in the production of waterproofing works, however, most cheap bitumen mastics are unable to stand an aggressive environment and constant water pressure for a long time and usually become unusable after 2-5 years. A high-quality alternative to bitumen mastics is liquid rubber.
- Polyurethane – The main component is polyurethane.
- Polymer-cement – The main component in such compositions is cement with polymer additives.
The coating compositions are applied to the surface in 2-3 layers after the previous one has dried. Some mastics require a primer of the base before application.
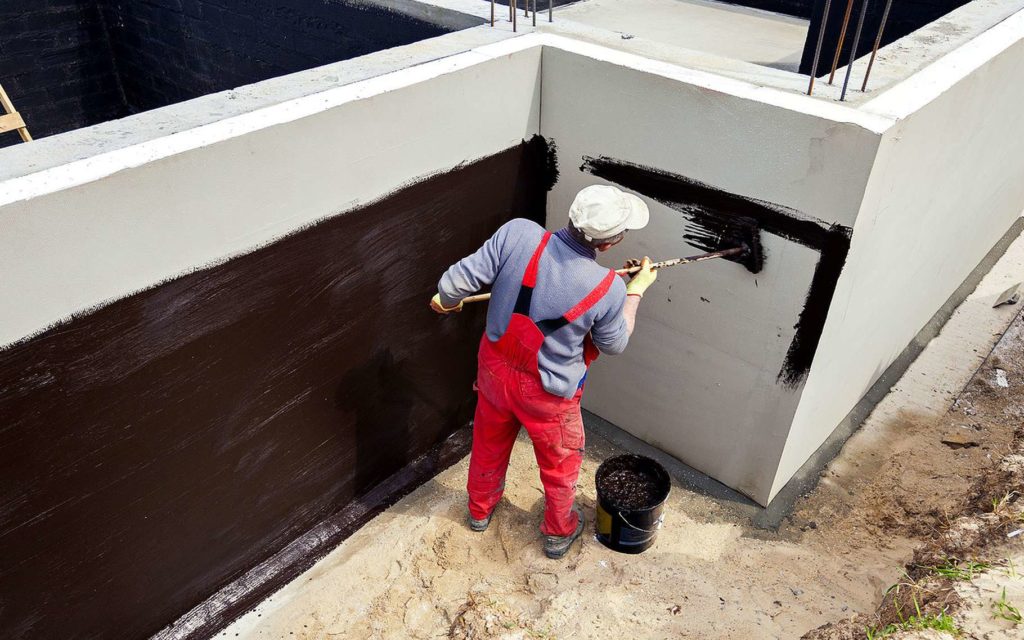
Rolled materials
Rolled materials are supplied in rolls and have various purposes, characteristics, as well as methods of their installation. Roll insulation is one of the most common methods of waterproofing, however, this type of membrane has characteristic disadvantages.
Disadvantages of rolled types of insulation:
- The presence of seams between sheets or rolls – Seams are the weakest point in any coating;
- Lack of 100% adhesion to the base – Rolled types of insulation do not have full adhesion to the base, which allows the water to stagnate and move from one place to another under the insulating carpet.
Basic Roll materials:
- Surfaced – Applied to the surface with an overlap of 15 sm, using surfacing using a burner. Surfaced membranes are recommended to be applied in 2-3 layers overlapping the seams of the previous one;
- Pasting – Have a self-adhesive base with which the material is glued to the surface. As well as in the surface sheets, the pasting sheets also need to be installed overlapping and in several layers;
- PVC and TPO (Thermoplastic polyolefin) membranes – Durable waterproof membranes designed for mechanical attachment to a vertical or horizontal surface. PVC membranes are attached with the help of hot air. PVC rolls are mounted in 1 layer.
You can read more about roll waterproofing in the article – “Roll waterproofing installation with detailed installation instructions“.
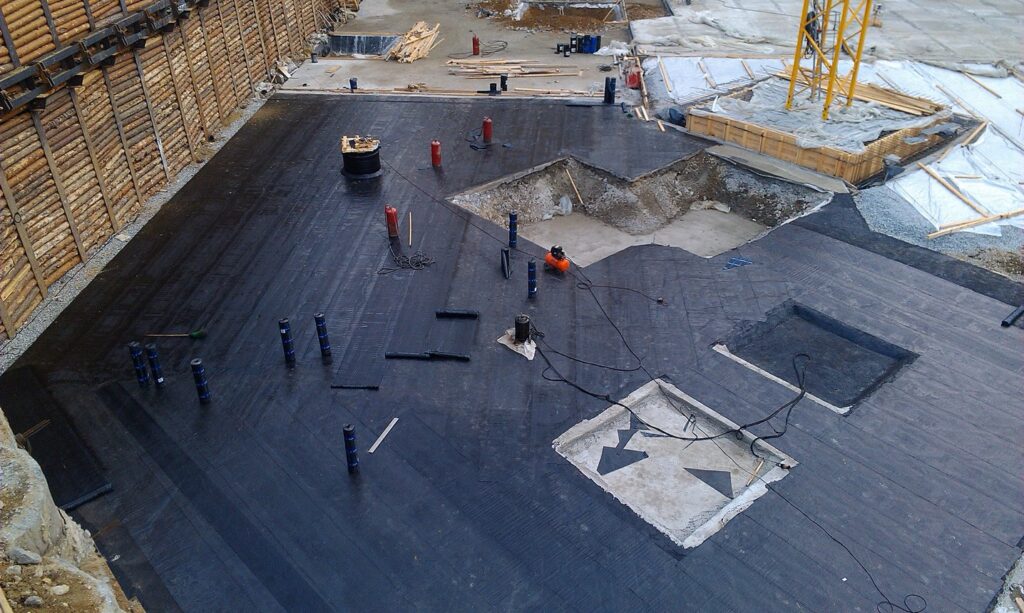
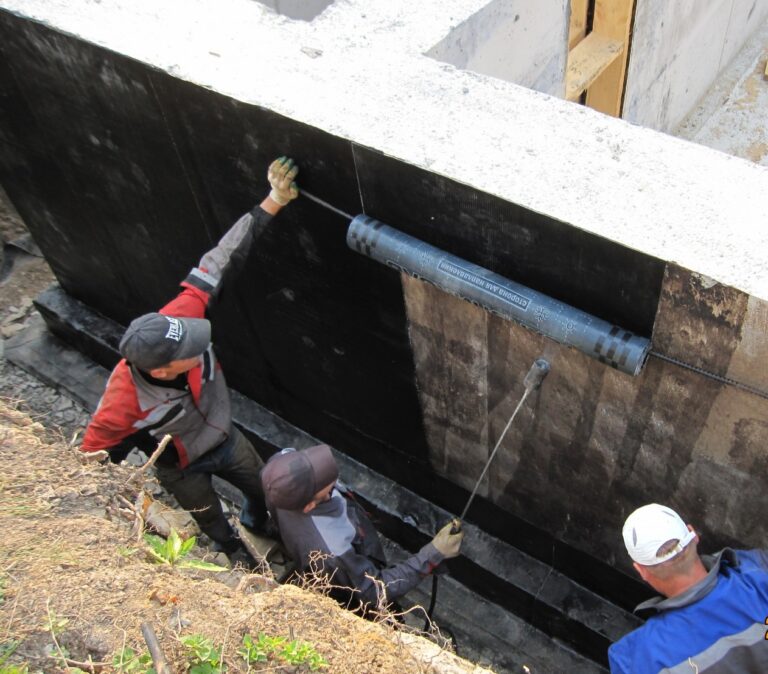
Liquid rubber
Waterproofing with liquid rubber is considered one of the most effective methods of installing a seamless waterproofing coating.
Liquid rubber — is a bitumen-latex emulsion forming a waterproofing coating with the following characteristics:
- No seams;
- 600-800% stretch;
- 100% adhesion to the surface;
- The service life of 50 years.
Due to its unique characteristics, liquid rubber is an idea as waterproofing for most structures, including all structural elements of the basement of the buried floor.
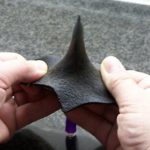
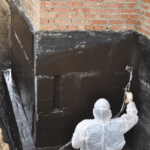
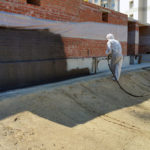
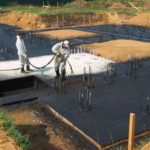
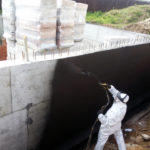
Comparison table and recommendations
This table shows the main differences between different categories of materials.
Liquid rubber | Coating waterproofing | Roll insulation | |
Mounting method | Non-firing By spraying Manually using a roller or brush | Non-firing By spraying Manually using a roller or brush | Using a burner and a live fire Construction hair dryer (for PVC) Roller clamping |
Number of required layers | 1 layer for double-component 2 layers for single-component | 2-3 layers | 2-3 layers |
Primer of the base | Available | Available | Available |
Seams and joints in the coating | Not available | Not available | Available |
Adhesion to the base | 100 % | 100 % | 5-30% |
Coefficient of elasticity | 600-800% | 50-200% | 10-20% |
Resistance to mechanical stress | Available | Only premium brands | Available |
Resistance to aggressive environment | Available | Only premium brands | Only premium brands |
Installation speed m2/per 1 day | 400-600 (by spraying) 20-90 (manually) | 20-90 | 20-50 |
Warranty period for works | 7 years | 3-5 years | 3-5 years |
Recommendation: Sometimes it is worth listening to the well-known proverb – “There is no good cheap. The price of the product, and the product at the price”. When choosing the material you need, do not buy it in the markets and do not chase cheap components – as a rule, cheap materials do not work or become unusable after 1-2 years, and the alteration of the waterproofing coating can cost you much, not to mention the damage that may be in case of leaks.
Prices for work on the waterproofing of the socle
To get an accurate price for all turnkey work, you need to call our engineer to inspect your facility and draw up a detailed technical specification, where the whole range of work will be taken into account.
Below is a table with approximate prices for complex works.
Works outside, price per m2
Works description | Unit of measurement | Price in $ |
The installation of surfaced waterproofing | m2 | 6 |
PVC membrane installation | m2 | 10 |
Polyurea installation | m2 | 15 |
Mastic waterproofing installation | m2 | 4 |
Arrangement of liquid rubber by spraying | m2 | 5 |
Arrangement of liquid rubber manually | m2 | 4 |
Installation of cement-mineral double-component waterproofing | m2 | 10 |
Polyurethane waterproofing installation | m2 | 10 |
Application of primer | m2 | 2 |
Work from the inside per m2
Works description | Unit of measurement | Price in $ |
Waterproofing of cold joints: -the installation of indenting -clearing of the indenting -layer-by-layer sealing of non-shrinkable composition | running meter | 10 |
Waterproofing of interblock joints: -the installation of indenting -clearing of the indenting -layer-by-layer sealing of non-shrinkable composition | running meter | 7 |
Waterproofing of expansion joints: -the installation of indenting -clearing of the indenting -sealing of the elastic profile -sealing of non-shrinkable composition -complex of works on injection | running meter | 81 |
Injection waterproofing of seams /cut-off waterproofing / cut-off waterproofing -the installation of indenting -clearing of the indenting -layer-by-layer sealing of non-shrinkable composition -the installation of boreholes and the installation of packers -a complex of works on injection -dismantling of packers and sealing of injection holes | running meter | 20 |
Injection waterproofing in body concrete -dimensioning, installation of boreholes and assembly of packers -complex of works on injection -demounting of packers and sealing of injection holes | m2 | 32 |
Injection waterproofing into the body of brick -dimensioning, installation of boreholes and packers -complex of works on injection -demounting of packers and sealing of injection holes | m2 | 32 |
Cement-mineral waterproofing | m2 | 10 |
Penetration waterproofing | m2 | 10 |
Waterproofing of places of entry of communications: -the installation of indenting -clearing of the indenting -layer-by-layer sealing of non-shrinkable composition -installation of boreholes and packers -complex of works on injection -demounting of packers and sealing of injection holes | piece | 115 |
Basement Waterproofing Cost Calculator
Calculation of waterproofing cost
The total cost of waterproofing
Restoration waterproofing of the basement
What should be done, if you have a house or building where you found leaks or wet spots in the basement?
To avoid adverse consequences, you need to restore the waterproofing of your basement, which has fallen into disrepair. This can be done both from the inside of the socle and from the outside. If we are talking about turnkey integrated waterproofing, then there is a certain minimum list of works that should be taken into account.
Outside:
- Dismantling of the blind area;
- Development of the soil (it is necessary to dig up to the foundation slab);
- Dismantling of the insulation;
- Removal of old insulation coating from basement walls and the foundation;
- Fillet installation in the presence of insulation transition from horizontal to the vertical surface;
- Application of new waterproofing taking into account the fillets;
- Reverse installation of thermal insulation;
- Installation of a spiked membrane;
- Backfilling of the excavated pit.
From the inside:
When performing restoration work from the inside, it is recommended to use injection waterproofing and take into account the repair of the following problem areas:
- Waterproofing cracks in the floor and walls;
- Waterproofing of cold joints at the junction of the walls and the foundation base;
- Sealing of interblock joints (if available).
When installing internal waterproofing of the basement or socle, you will need to perform the following steps:
- Dismantling of plaster (to apply a protective compound on the walls);
- Dismantling of tiles;
- Dismantling of the screed (for example, to get to the cold seam and perform injection insulation);
- Performing injection waterproofing;
- Application of a waterproofing compound operating under negative water pressure;
- Restoration of rough finishing of plaster and screed.
Diagram of the injection installation from inside the house:
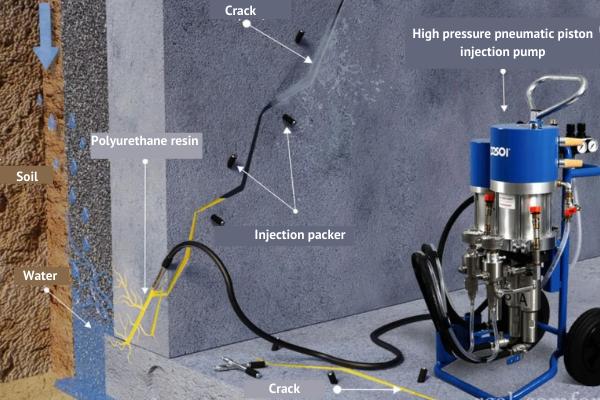