Table of Contents
- What is polymer waterproofing?
- Types of polymer-based waterproofing materials
- Criteria by which different polymer materials differ
- Areas of application
- Polymer waterproofing arrangement
- Prices for polymer waterproofing
- Online calculator for calculating the cost of waterproofing works
In modern construction, the use of waterproofing compounds is quite widespread, the main task of which is— to provide reliable protection of structures for various purposes from the effects of liquids. Hydrophobic compounds belong to various types, such as, for example, bitumen, polymer, cement, asphalt, sheet (made of metal or plastics), and not only. This article will focus on polymer waterproofing, the main characteristics of polymer materials, their application, and installation technologies.
What is polymer waterproofing?
Polymers have become an effective and popular waterproofing material. This is due to several factors, including adhesion to the material and durability. Scientifically speaking, polymers are hydrophobic. While this does not mean that they are literally afraid of water, it does not mean that they are literally afraid of water, it does not mean that they repel water instead of absorbing it.
Although most waterproofing polymers are available in liquid form, they are also available in the form of pebbles or powder and can be used in a wide variety of applications.
These polymers can be heated, extruded, molded, poured, or otherwise transformed into a wide range of waterproofing materials. These include waterproofing films of low to high quality and thickness, sealants, and gels designed to be liquid for a short period of time to fill cracks and crevices before they harden and become an effective water barrier. In some cases, they can be poured into special molds to create dynamic channels that are suitable in shape, which help keep the object dry by deflecting and removing standing water.
Advantages and disadvantages
The use of polymer waterproofing is becoming an increasingly common method of processing buildings. This is due to the high quality of its components, as well as a considerable number of other positive characteristics.
Advantages:
- Polymer materials have high elasticity indicators, reaching values from 400%;
- Such hydrophobic formulations are characterized by a long service life, varying in most cases from 25 to 50 years;
- Waterproofing based on polymeric substances is particularly well suited for processing monolithic structures and structures made of metal;
- Polymer materials are actively used for processing structures, including those that have a complex shape or non-standard relief;
- Polymer compositions have the following properties — a high degree of resistance to any mechanical, chemical, and physical influences, including temperature differences from -60 to +110 degrees Celsius, as well as contact with sunlight;
- Polymer bases are resistant to wear, which is explained by their excellent composition, the polymer film does not become thinner or less reliable over time. The non-susceptibility of the compositions to operating conditions perfectly explains the fact that polymer waterproofing retains the uniformity of the coating even after a long period;
- Another property — is a high degree of adhesion to various substrates, including concrete, wood, metal, brick, and numerous finishing materials;
- Modern polymer materials are absolutely safe both for the environment and for human health, and therefore they can be used both outside and indoors;
- Repair of the polymer coating is carried out very easily: it is enough to detect the defect and apply a new layer of waterproofing around the perimeter of the damaged area;
- Such property as high vapor permeability of polymer compositions is responsible for ensuring a comfortable microclimate and absolute protection of structures from the effects of liquid;
- The ability to color compositions with a huge range of colors and shades, allows them to be applied as a finishing coating.
Disadvantages:
The type of waterproofing in question also has several negative properties, which, however, are successfully compensated by their advantages. The disadvantages of such hydrophobic coatings include their rather high cost compared to other waterproofing compounds, such as roofing material and bitumen. However, the excellent quality of polymer compounds fully justifies their cost.
Important: Polymer coating is much less likely than other waterproofing options to need repair, so over time, the highest cost of such a coating becomes even less than the costs required to care for other types of waterproofing.
Types of polymer-based waterproofing materials
Polymer-based formulations differ from each other in composition, consistency, application technology, and some other indicators. The main types of polymer waterproofing, as well as tables and brief descriptions of their characteristics, will be presented below.
Polymer cement solutions
The table below shows some characteristics of polymer cement solutions — one of the most popular waterproofing materials. The composition of such solution, in addition to cement and polymer substance, includes special additives of organic origin that increase the elasticity and hydrophobic properties of waterproofing. This coating is quite strong and light, and its thickness is only a few millimeters.
Among the useful functions performed by polymer-cement solutions, it is possible to distinguish the protection of the base material from the effects of liquids, chemicals, corrosion, and other aggressive factors, as well as the protection of the structure from the pressure exerted by groundwater. At the same time, polymer-cement waterproofing allows the base material, for example, concrete, to breathe. The positive aspects include the creation of obstacles to the formation of mold and mildew.
However, a number of disadvantages are also characteristic of the solutions under consideration. For example, they have a sufficiently low bending and tensile strength, are unable to withstand strong mechanical influences, and are characterized by low wear resistance. To compensate for these negative aspects, polymer additives from 2 to 30% of the total weight are introduced into the solution.
Main characteristics of polymer cement materials
Regulated properties | Value |
Density, g/sm3 | 1,07-1,08 |
Conditional viscosity, with | 40-50 |
Plastic viscosity, sDr | 10-15 |
BCS (Booster Compressor Station), dPa | 60-100 |
Static Shear Stress 10 sec/10 min, dPa | 30-40/40-70 |
Water output, sm3/30 min | < 6 |
pH | 8-10 |
Sand content, % | < 0,5 |
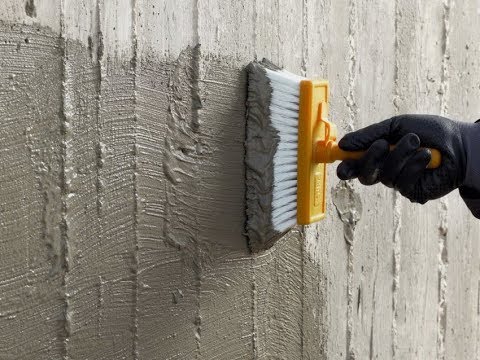
Bitumen-polymer mastics
Bitumen-polymer mastics combine the best qualities of bitumen and polymer substances. They are characterized by a homogeneous, rather viscous consistency, as well as the ability to form a seamless coating after solidification. Such mastics provide a reliable and durable coating of the base while forming a resistant membrane that protects the composition from moisture. The excellent penetrating ability characteristic of mastics ensures high-quality adhesion of the waterproofing to the base. However, at the same time, bitumen-polymer mastics are characterized by toxicity, rather a high cost, and flammability.
As for the waterproofing technology, rollers, brushes, and even spray guns are perfect for this case. At the same time, it is important to remember that only the outer surfaces of the structures are finished with bitumen-polymer mastics. The solidification period of one layer of material varies from 12 to 24 hours. Such mastics provide a reliable and durable coating of the base while forming a resistant membrane that protects the composition from moisture. The excellent penetrating ability characteristic of mastics ensures high-quality adhesion of the waterproofing to the base.
However, at the same time, bitumen-polymer mastics are characterized by toxicity, rather a high cost, and flammability. As for the waterproofing technology, rollers, brushes, and even spray guns are perfect for this case. At the same time, it is important to remember that only the outer surfaces of structures are finished with bitumen-polymer mastics. The solidification period of one layer of material varies from 12 to 24 hours.
You can read more about bitumen waterproofing in the article – “Bitumen waterproofing: types, characteristics, and technology of the installation“.
The main characteristics of bitumen-polymer mastics
Name of indicators | Bitumen-polymer roofing and waterproofing mastic |
Heat resistance for 5 hours, at least, at a temperature not lower than | +100 °С |
Water absorption within 24 hours, % by weight, no more | 0,4 |
Adhesion strength to the base (made of concrete, metal), MPa(kgs\sm²) not less | 0,3 (3,0) |
Bond strength between layers, MPa (kgs/sm), not less | 0,3 (3,0) |
Conditional strength, MPa (kgs/sm), not less | 4,0 (40,0) |
Elongation at break, % not less | 700 |
Conditional viscosity, С, not less | 10 |
Mass fraction of non-volatile substances, % not less | 55 |
Viability, h, not less | 2 |
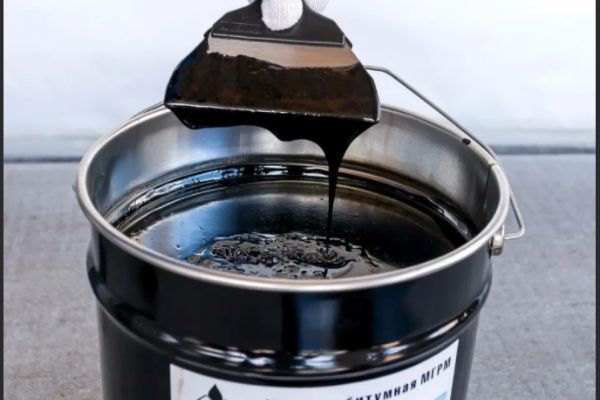
Polyurethane mastics
Below is a comparison table of polyurethane mastics with standard bitumen materials. It can also be noted that polyurethane-based mastics are characterized by high quality, reliability, long service life, excellent physical and mechanical properties, safety for human health, a rich assortment, as well as the possibility of using such hydrophobic compositions for a huge variety of surfaces, both at the construction stage and during the repair. A significant disadvantage can be considered only a sufficiently high cost.
You can read more about polyurethane in the article – “Polyurethane waterproofing“.
The main characteristics of polyurethane mastics
Indicator | Polyurethane mastics | Bitumen mastic |
Service life | 15 years | 1-2 year |
Shrinkage during drying | Not available | Available |
Behavior at temperature changes | Retains elasticity | Cracks |
Possibility of coloring | Available | Not available |
The number of layers to obtain a resistant coating | 1-2 | 2-3 |
Solid-phase content | 80-90% | 50 % |
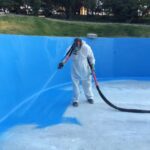
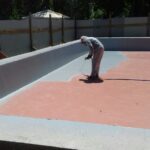
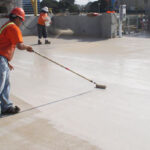
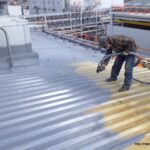
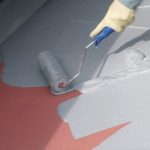
Bitumen-polymer roll waterproofing
Using the example of the well-known isoplast, bituminous polymer coatings of the roll type can be characterized as resistant to mechanical loads, temperature changes (-) as resistant to mechanical loads, temperature changes (от -20 до + to +125 degrees Celsius), and microbial activity, durable, non-toxic, universal, compatible with all types of surfaces and very easy-to-use hydrophobic membranes. The main disadvantages of this type of material are the presence of seams and joints between the rolls, as well as the lack of Celsius) and activity % adhesion to the surface.
Main characteristics of polymer-rolled materials
Isoplast brands | Isoplast K | Isoplast P |
Breaking load, Н, not less | 600 | 360 |
Water absorption, %, no more | 1,0 | 1,0 |
Flexibility on the beam, mm/°С | 10-15 | 10-15 |
Heat resistanceь, °С, not lower | 120 | 120 |
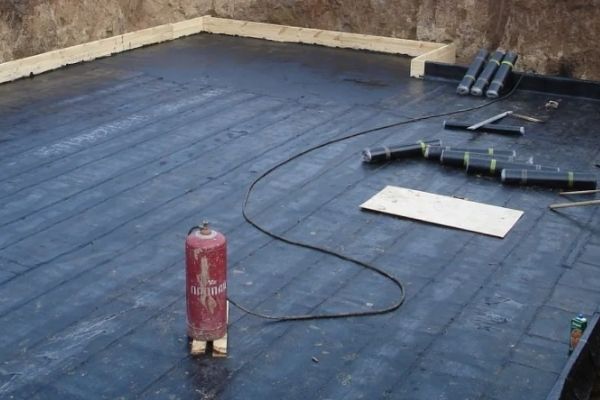
Popular polymer-based materials
Currently, a large number of polymer materials are distinguished by their reliability and durability. For example:
- HydroPaz – compositions of this German manufacturer of industrial waterproofing, differ not only in high reliability but also in the fact that they are able to withstand negative water pressure from outside to inside, which means that when repairing waterproofing they can be applied from inside the room without digging outbuildings around the perimeter.
- Ceresit — characterized by excellent adhesion to concrete, high water resistance and resistance to rain, as well as resistance to frost and hydraulic loads.
- Bolars hydroflex — is characterized by resistance to chemicals, the ability to maintain its operational properties for a long time, as well as the ability to work with this material at temperatures from +5 to +30 degrees Celsius.
- Polymer waterproofing Sonora — designed for interior work with those structures that are periodically exposed to water. Such structures include, for example, bathrooms, showers, sanitary units, kitchens, and so on. When applying the material, an elastic seamless coating is created that is resistant to various environmental factors.
- Technonicol rolled polymer membranes — have a low cost, are quite lightweight, and are characterized by ease of installation, but at the same time do not have a long service life, are toxic, and eventually lose their appearance under the influence of ultraviolet radiation. In this regard, it is recommended to use such materials for outdoor work with those parts of structures that are not exposed to aggressive sunlight.
- Polyflex — this is polyurethane waterproofing. These materials are manufactured by a German company for the production of industrial waterproofing and are very reliable and durable, due to which contractors using these materials can afford to give long warranty periods for the work performed. When applying the compositions, a seamless waterproofing coating is formed on the surface with 100% adhesion to the substrate and resistance to mechanical and UV radiation.
Criteria by which different polymer materials differ
In order to choose a suitable polymer, it is necessary to carefully study the options presented on the construction market. To cope with this task, knowledge of the criteria by which hydrophobic compositions differ and the ability to make a choice based on these criteria will help.
The first criterion is the consistency of the waterproofing material, which can be liquid or semi-liquid. Such compositions are easily applied to the surface and create a seamless coating that can reliably protect the structure from moisture. Much less often, an alternative to liquid and semi-liquid compositions is used, represented by rolled membranes.
According to the composition, polymer waterproofing materials are divided into several types, depending on the components that complement the mixture. To date, the most common are cement-polymer and bitumen-polymer materials.
If we talk about the methods of applying polymer bases to the surface, we can highlight the following points that affect the technology of working with the material:
- Experience with waterproofing compounds;
- The time, allocated for the work;
- A set of available tools.
When working with waterproofing compounds, it is important to clearly follow all the steps of the instructions compiled by the manufacturer. If a composition in need of preparation has been selected, it is necessary to carefully observe the proportions of the components at the cooking stage, as well as monitor the timing of use of the prepared composition. Otherwise, the material may harden even before it is applied to the surface.
It is equally important to pay attention to such a criterion as the expense of waterproofing. In hardware stores, it is recommended to choose not too expensive formulations, which are also characterized by economical use. If we talk about the functions of polymer waterproofing, for each element of the structure (roof, foundation, floor, and so on), you should choose a separate composition that is aimed at working with the necessary part of the building.
Important: in order to correctly select the necessary waterproofing material that is suitable for your situation and problem, it is recommended to contact a construction company specializing in waterproofing works. Only the experience and knowledge of professionals will help solve your problem with leaks once and forever.
Areas of application
Currently, polymer waterproofing is used in many construction industries. With the use of such materials, many elements of private and apartment buildings, as well as administrative ones and industrial enterprises are processed. Let’s consider some areas of application of polymer materials.
Foundation
It is the part of the building that is most vulnerable to moisture since it is the foundation that most often comes into contact with groundwater and precipitation accumulating on the earth’s surface. For waterproofing of this element of the house, polymer materials are often chosen, which are applied to the base quickly and have high elasticity, which, in turn, will not allow the material to crack or disperse at the joints when the foundation shrinks. The service life of such a coating exceeds 40 years.
You can read more about the waterproofing of the foundation in the following articles:
- Foundation waterproofing arrangement: Methods, materials, prices, and recommendations of specialists
- Waterproofing of the ribbon foundation: Technology and materials
- Waterproofing of foundation blocks and walls
- Horizontal waterproofing of the foundation: The technology of the arrangement and the materials necessary for this
- Vertical waterproofing: materials and methods of its arrangement
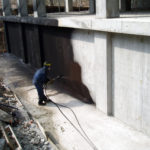
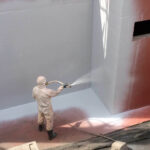
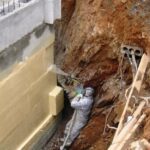
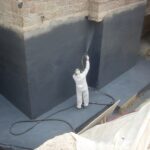
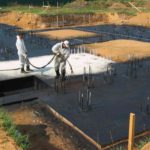
Roof
The roof also often needs reliable and durable waterproofing, which is the treatment with polymer materials. Liquid and semi-liquid polymers are used to protect the roofing, which is in regular contact with liquid, from moisture, while roll-type waterproofing is gradually being abandoned. This is due to the need to additionally process the seams and joints of rolled materials, which are absent in polymer compositions of a more liquid consistency.
You can read more about roof waterproofing in the following articles:
- Waterproofing of the roof: methods of its arrangement and types of materials for performing high-quality work
- Waterproofing of a flat roof. Recommended materials, methods of installation, and prices for work
- Waterproofing and repair of pitched roofs
- Roof waterproofing repair: Methods, materials, and prices
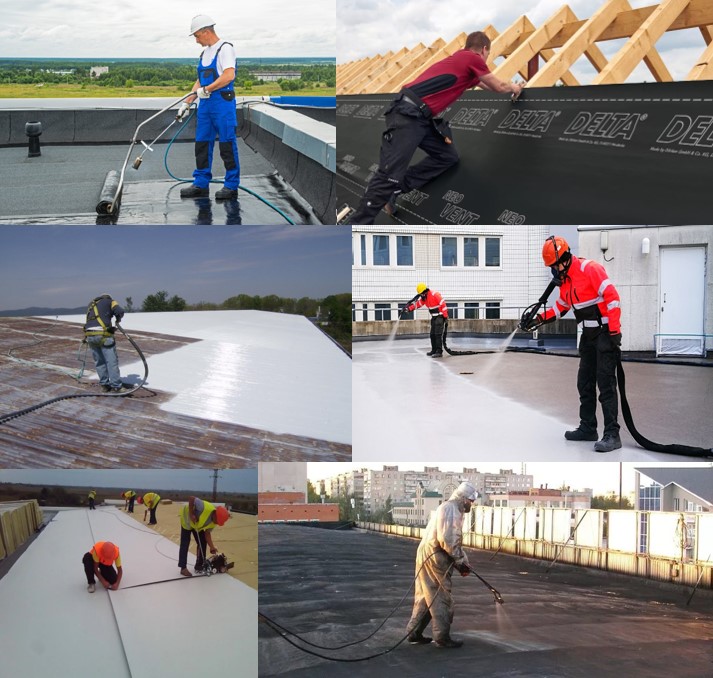
Concrete
Polymer waterproofing due to its positive properties is used almost everywhere for the treatment of both aboveground and underground structures. For example, concrete buildings are treated with strong and elastic materials. Polymer compositions have a full-fledged adhesion to concrete bases, and the seamless coating, resistant to aggressive environments and mechanical damage, makes it durable and reliable.
You can read more about concrete waterproofing methods in general in the article – “Concrete waterproofing and how to do it: Types of materials and methods of the arrangement“.
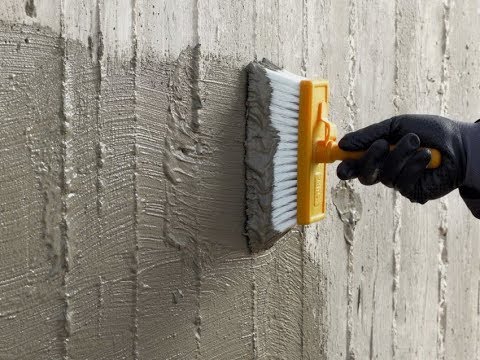
Walls
Along with the foundation and roofing, the walls of private and apartment buildings located below the level of the planning ground, as a rule, these are the walls of basement rooms, are subject to treatment with polymer compounds. The ability of polymer films to protect structures from the effects of atmospheric precipitation and aggressive salts and minerals in the ground makes it possible to protect the walls of houses from various phenomena very reliably.
You can read more about the waterproofing of the foundation and walls in the following articles:
- Waterproofing of foundation blocks and walls
- Waterproofing of basement and house walls from outside and inside – Methods, materials, prices, and technology
- Waterproofing of bricks and masonry
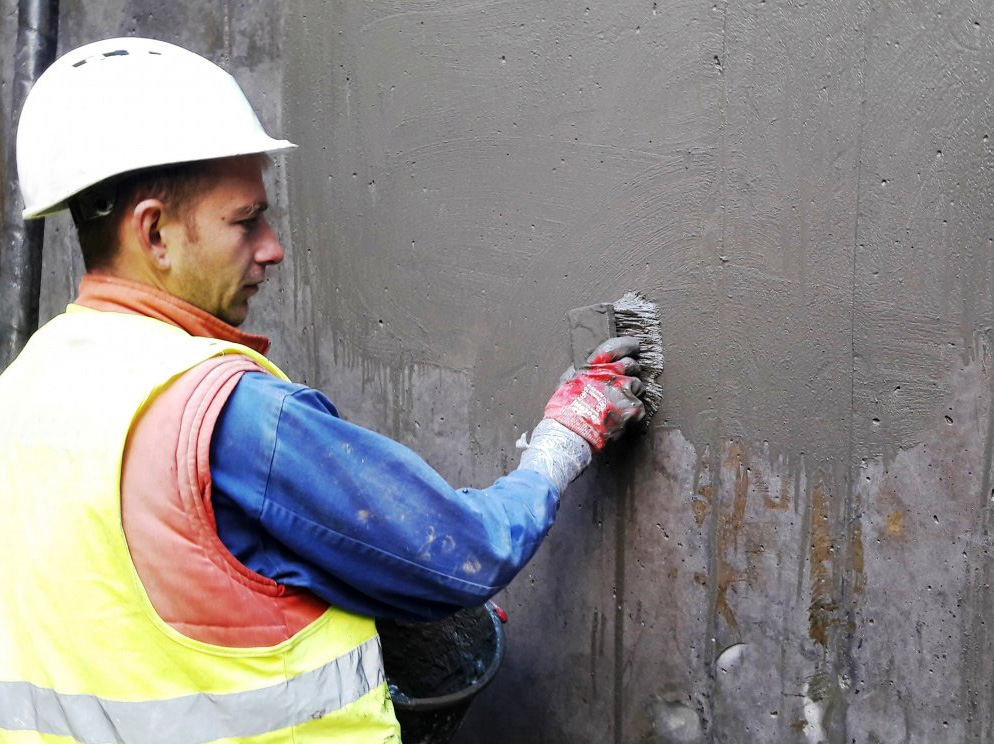
Wet areas and bathrooms
Polymer bases also cope with the protection of structures that are constantly in contact with liquid. We are talking, for example, about bathrooms, and high-quality waterproofing which is necessary for their normal use. The seamless hydrophobic coating created by polymer materials can last for several decades without creating the need to organize repair work. The main thing —is to properly apply the waterproofing material to the surface.
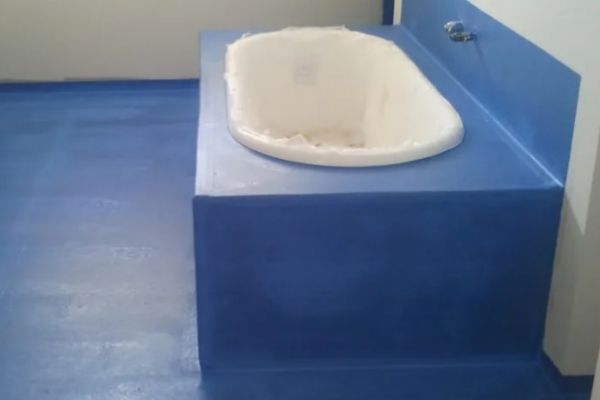
Polymer waterproofing arrangement
To work with polyurethane compounds, you need to have some experience and understanding. When installing polymer waterproofing, it is necessary to perform several important steps:
- Preparation of the base. Before using polymer hydrophobic materials, it is important to prepare the base of the structure for work in advance. To do this, areas that are more exposed to liquid are marked on the surface. In the lower part of the surface of the walls and floor, for which polymer waterproofing is used, it is important to clean from any dirt and get rid of irregularities. Also, the work surface should be dry.
- In places where the floor comes into contact with the wall, namely where the surface passes from the horizon to the vertical, for a smooth transition from the horizon to the vertical, it is necessary to make a small skirting board, the so-called fillet of cement, which is subsequently smeared with a polymer composition. This structure should also harden before the application of the following layers of the material.
- Preparation of the material – Some polymer compositions require the mixing of two or more components. When using such materials, it is strongly recommended to follow the manufacturer’s instructions when preparing.
- Priming the base. Bases, made of metal or concrete should be primed using primers, while not forgetting that each type of polyurethane material has its own primer.
- Application of waterproofing. Then the selected polymer composition is applied to the surface in compliance with all the rules and deadlines indicated on the packaging with waterproofing material. The next layers of the material are applied only after the first one has solidified.
- After applying the required number of layers of waterproofing to the surface and their hardening, you can start finishing the work.
Important: If you have little experience in applying this kind of compositions, then experts advise applying each next layer in a contrasting color: this will help to control the thickness of the material distribution.
Prices for polymer waterproofing
Prices for certain works may vary depending on the scope of work, the grades of material used and the complexity of the application.
Description of work | Unit of measurement | Price in $ |
Application of polyurea | m2 | 30 |
Application of mastic waterproofing on a polymer basis in 1 layer | m2 | 8 |
Application of liquid rubber by spraying | m2 | 8 |
Application of liquid rubber manually in 1 layer | m2 | 10 |
Application of cement-mineral double-component waterproofing | m2 | 20 |
The arrangement of Single-component polymer-cement waterproofing in 1 layer | m2 | 18 |
The arrangement of double-component polyurethane waterproofing in 1 layer | m2 | 24 |
The arrangement of single-component polyurethane waterproofing in 1 layer | m2 | 24 |
The arrangement of double-component polyurethane waterproofing in 1 layer | m2 | 24 |
Application of penetrating compounds | m2 | 20 |
Application of the primer | m2 | 8 |