The roof of a building — is a rather complex structure, one of the purposes of which is to protect the structure from the penetration of water and moisture. For this purpose, waterproofing is performed during the construction of the roof. In the absence of proper waterproofing, rainfall, water formed as a result of melting snow and other moisture can get into the room affecting the integrity and reliability of the structure.
Why and when it is necessary to repair the roof waterproofing?
Repair of the protective layer of waterproofing may be necessary for several reasons:
- The service life of the waterproofing materials has ended – each composition has its own service life and at its end, the insulation should be replaced or restored.
- Waterproofing material has fallen into disrepair due to its poor quality – There are materials on the market that are of rather poor quality and they fail much faster than others. There are also high-quality materials that have lost their quality due to violations of storage or transportation conditions.
- Wrong choice of waterproofing coating – Sometimes builders choose the wrong insulation coatings, which leads to their deterioration and the formation of leaks. For example, when choosing the wrong composition for waterproofing a flat roof. Sometimes builders forget about the effects of ultraviolet rays of the sun on waterproofing and do not use UV-resistant insulation as a finishing coating.
- When installing waterproofing violations of the installation technology were committed – This is the most common reason why leaks are formed in roofs and waterproofing requires urgent repair or replacement.
Important: All the above reasons are somehow related to the professionalism of the one who designs the waterproofing and the one who applies it. Choosing a professional contractor with experience and recommendations, you guarantee yourself the absence of leaks and a long service life of your waterproofing coating.
When it is necessary to make repairs:
- If you find leaks in the roof of your building;
- If the period of the planned replacement of roofing has come;
- If you understand that the waterproofing was performed with violations and want to avoid leaks and damage to the finishes made in the building or house and the property located there.
Consequences of poorly made roof waterproofing:
- Cracks in the base – When water enters the concrete base through the waterproofing coating, the water is absorbed into the concrete like a sponge, after which it freezes in winter and thaws in summer, destroying the concrete and forming microcracks in it, which grow from year to year;
- Excessive moisture formation in the room;
- The formation of mold and mildew is dangerous to human health;
- Flooding of the room with damage to the completed finish and arranged furniture.
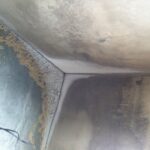
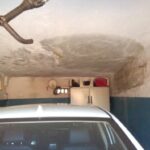
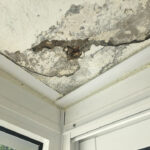
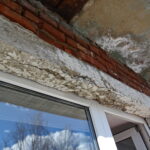
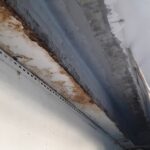
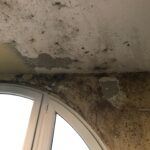
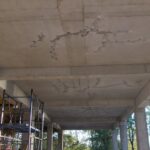
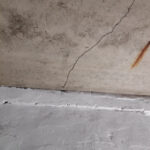
2 existing approaches to roof waterproofing repair
If you encountered leaks or improperly made waterproofing, then you have 2 options to make repairs and fix everything:
- Capital
- Local or point
Each option has its own advantages and disadvantages and requires different financial and time investments.
Important: In flat roofs where water protection was made using membrane or roll-on sheets, it is very difficult to detect leaks, since these materials do not have 100% adhesion to the surface and water can enter in one place, and exit from the inside in a completely different, weakest one. If it is possible to determine accurately the place of water entry, it is very difficult to perform local restoration with a guarantee against future leaks, respectively, if the customer needs a guarantee of a dry room, it is recommended to make major repairs of waterproofing.
Major repairs
This is when it is decided to replace the waterproofing completely and do everything according to the technology starting from the very beginning.
During a major restoration, the old waterproofing coating is dismantled and a new one is applied instead. If we are talking about a flat roof, then when dismantling the old waterproofing, it may be necessary to dismantle other layers, such as a broken screed and insulation.
Dismantling of the screed for waterproofing occurs mainly when it comes to a soft rood made of rolled sheets. If the performed insulation passed water for one or two seasons, then this water was absorbed into the concrete screed, froze, and thawed, which in the end most likely led to its destruction. Accordingly, when you dismantle the old roll waterproofing, you will find a destroyed screed, which will also have to be dismantled and then restored together with the new waterproofing.
Disadvantages:
- High cost of capital replacement of waterproofing;
- Time of work production;
Advantages:
- With the right approach to the choice of waterproofing and compliance with the technology during its installation, you can solve problems with leaks once and forever.
Local repairs
This is when it is decided to fix the waterproofing not completely, but locally by repairing a certain area or adding another layer of waterproofing to the existing one.
The methods of local repair depend directly on the type of roof and material used for insulation. You will be able to study different materials and methods of local restoration in the continuation of this article, however, do not forget that not all damage to the waterproofing layer is obvious, which makes it very difficult to guarantee the absence of leaks of the roof as a whole (for example, bitumen was burned somewhere during installation and the seam lost its hermetic properties).
If it is impossible to perform spot repairs, as a local strategy, you can add another layer of insulation along the entire plane. The optimal material for this— is liquid rubber.
Disadvantages:
- No warranty for spot repairs;
- Less durable option.
Advantages:
- Relatively low cost of work;
- Can be produced in a relatively short time.
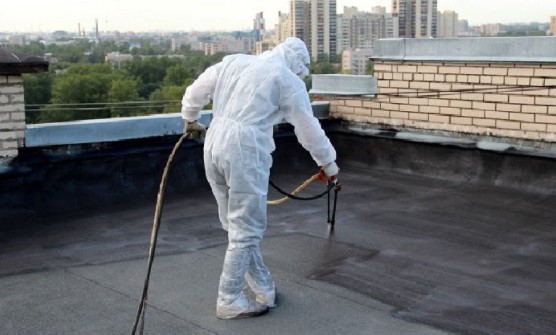
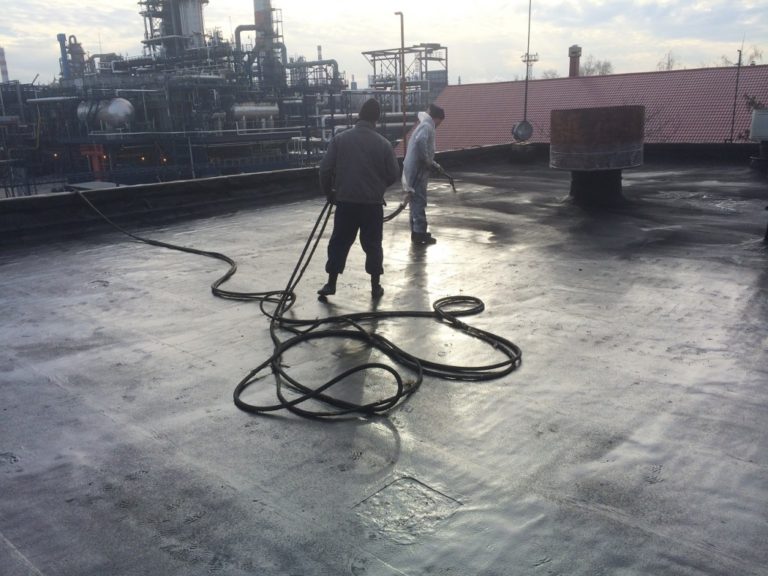
Methods and materials for the repair and restoration of waterproofing
Different materials and different waterproofing technology are suitable for each type of roof. Below are the most popular methods of waterproofing the roof. Most of these methods are suitable both for application at the initial stage, during the construction of a building, and for local restoration work.
Liquid rubber
Liquid rubber — is a bitumen-latex emulsion with the addition of various polymers. When applied, liquid rubber forms an elastic seamless coating on the surface with 100% adhesion to the base.
Characteristics of liquid rubber:
- No seams;
- 600% of elasticity;
- 100% adhesion to the surface;
- High performance when applied with spray equipment
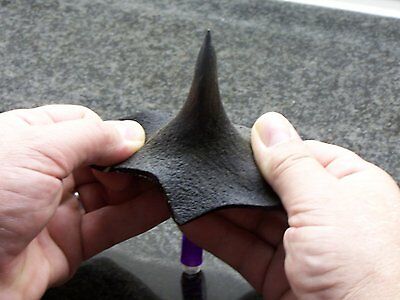
LR can be applied to the following bases:
- Concrete;
- Metal;
- Brick;
- Bitumen roll membranes.
How to perform repairs using liquid rubber?
Due to its unique characteristics, Liquid rubber is ideal for use as the main waterproofing of flat and other roofs during the construction of a building, capital, or local restoration.
Due to the fact that rubber has 100% adhesion to bituminous materials, it is perfect for eliminating leaks and point-directed repairs by applying over an existing layer of rolled surfaced waterproofing. After coating the rolled bitumen sheets with a layer of LR, a seamless elastic rubber coating is formed, which has 100% adhesion to the old base and which does not tear during dynamics and movement (since it has a high coefficient of elasticity).
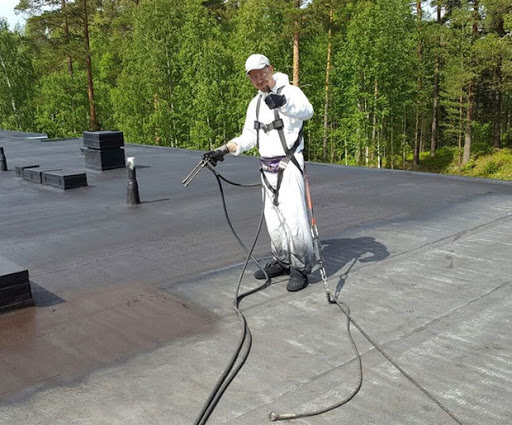
Polyurethane waterproofing
Polyurethane waterproofing when applied forms a seamless coating with 100% adhesion to most substrates. Polyurethane is elastic enough and is resistant to ultraviolet radiation, which makes it an ideal option for finishing the roof in use.
Polyurethane is perfect for waterproofing installation at the stage of construction or major repairs. At the same time, not every polyurethane waterproofing can be applied over existing membrane or surfaced bitumen insulation.
Polyurethane is applied to the following bases:
- Concrete;
- Metal;
- Brick.
There are various modified polyurethane compounds that can be applied to various coatings.
How to perform repairs using polyurethane compounds?
Polyurethane compositions are best suited for restoring insulation made of polyurethane mastics of various types, but they can also be used to apply over an existing layer of insulation made of rolled bitumen membranes.
Important: For each surface, its own type of polyurethane waterproofing is suitable, for example, double-component polyurethane bitumen-based mastics are best suited for rolled bitumen membranes. If the material is chosen incorrectly, a serious problem may arise in terms of the adhesion of polyurethane mastic to the old insulation layer, which as a result will lead to poor-quality work.
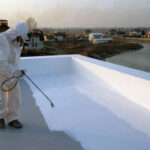
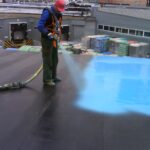
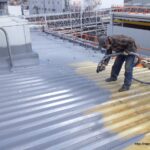
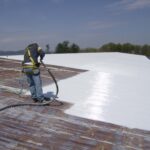
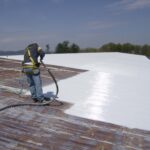
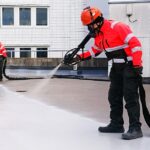
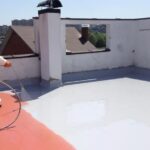
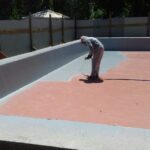
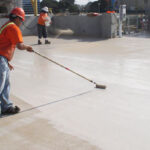
Roll-on surfaced insulation
These are bitumen membranes that are applied to the surface by melting them with a burner and fire. When the bitumen layer collides with fire, it melts and glues the roll to the surface.
Disadvantages of the material:
- The presence of seams;
- Lack of full adhesion;
- Fire mounting method.
- The presence of seams;
- Lack of full adhesion;
- Fire mounting method.
How to perform repairs using surfaced materials?
Spot repair:
If we are talking about spot repair of damaged areas of bitumen membranes, then it is performed by the following method:
- Cut the damaged membrane cross-wise;
- Apply bitumen-based waterproofing to the lower base;
- Paste the first patch from the deposited membrane;
- Press the cut corners to the patch;
- Make a new patch of rolled insulation on top.
Important: Local repairs can be carried out with rolled surfaced waterproofing exclusively on top of the same surfaced materials.
Scheme of repair of a soft rolled roof:
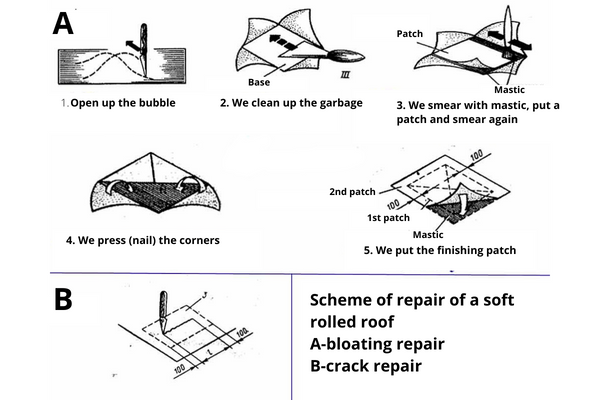
PVC membrane
These are mounted PVC membranes that are not fused but are fixed to a horizontal surface with the help of special clamping structures and slats. PVC rolls are stitched together with hot air, for which special construction dryers are used.
You can read more about membrane waterproofing in the article – “Membrane waterproofing: Types of materials and methods of their installation“.
Disadvantages of the material:
- The presence of seams between the rolls;
- There is no adhesion to the base, the membrane lies like a carpet and any water that has penetrated under it can freely walk under the coating.
How to perform repairs using PVC?
PVC coating may be damaged during operation or as a result of poor-quality work, but breakthroughs, punctures, and cuts can be repaired.
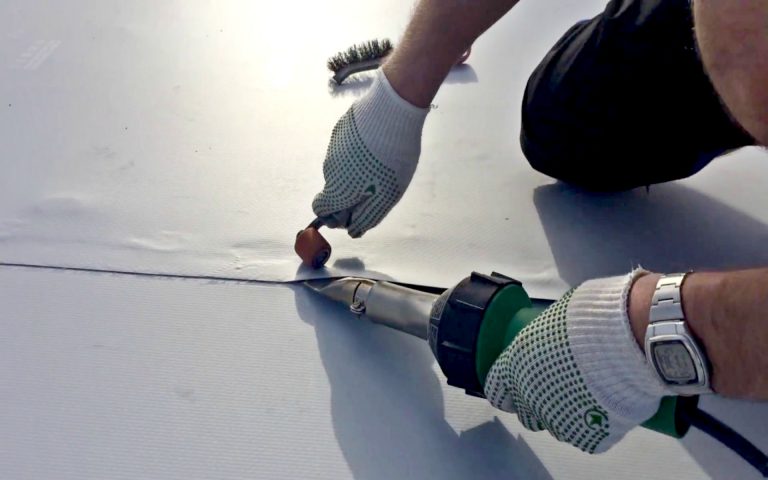
Spot repairs:
Spot restoration of the damaged area is done as follows:
- To install the patch, a PVC membrane of the same series and the same manufacturer is selected;
- Patch installation, so that it overlaps the damaged area by at least 5 cm on each side;
- Sealing the weld with a silicone roller.
Important: When installing patches on PVC membranes, it is very important to choose a membrane from the same manufacturer of at least a 100% analogue, otherwise the installed patch and the main waterproofing carpet may be incompatible, which will affect the adhesion between them and the quality of the work done.
The scheme of repair of a membrane roof:
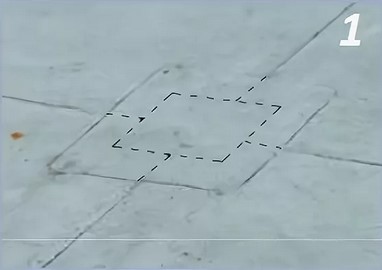
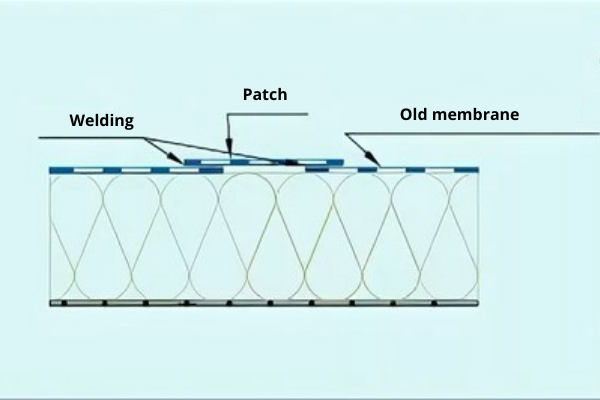
Comparison of materials
The following table compares liquid rubber with the main types of waterproofing membranes:
Liquid rubber | Surfaced rolls | PVC membrane | |
Mounting method | Non-firing | Firing with a burner | With the dryer and mechanical fixation |
Availability of seams | Not available | Available | Available |
Adhesion to the surface | 100 % | 20 % | No adhesion |
Coefficient of stretching | 600-800% | 10-20% | 10-20% |
UV resistance | Available | Only with a special dressing compound | Available |
Suitable for application on a base of: | Concrete, brick, metal, bitumen bases | Concrete, brick, metal, bitumen bases | Concrete, brick, metal |
Suitable for the local restoration of the following materials | Surfaced waterproofing | Surfaced waterproofing | Membranes of the same type |
The warranty period for works | 7years | 3-5 years | 3 years |
Professional approach to roof repair: Stages of work
If you do not want to repair your roof every year, but want to do repairs once and for a long time, then you need to understand that this is not an easy task, it requires a professional and responsible approach, deep knowledge of various waterproofing methods, and, of course, experience.
The first step is: To identify problem areas in the existing waterproofing and how to solve them – by the method of visual inspection, a specialist can understand what problems this roof has got and how they can be solved. At this stage, the specialist determines whether it is possible to solve the problem locally or whether it is necessary to cover the entire roof anew.
After examining the roof, the arrived expert should tell you about the local and more capital methods of solving problems with waterproofing and describe all the disadvantages and advantages of a particular solution and the materials proposed for it. After the decision and the estimate are agreed upon, and the contracts are signed, it will be possible to proceed directly with the work.
The restoration of the waterproofing coating consists of several main stages, these stages may differ from each other depending on the chosen coating and method:
- Dismantling of the old coating or local repair of damaged areas;
- Preparation of the base – before applying any insulation, the base should be cleaned of dust and dirt;
- Fillet at the transition from the horizon to the vertical, in the absence of a smooth transition – The transition of waterproofing from the horizon to the vertical should not be at a slope of 90 degrees, it should be smooth. For this purpose, the so-called fillet is made.
- Primer – applying a special primer to improve the adhesion of the new waterproofing coating with the base of the old one or with concrete. When installing membrane insulation, a primer is not required;
- Waterproofing – application of a new waterproofing, observing all norms, manufacturer’s recommendations, and installing the technology.
Important: If the waterproofing base remains in the form of a finish, then when choosing waterproofing, it is necessary to take into account its resistance to ultraviolet radiation from sunlight. The material should be UV resistant or with a special dressing compound that protects it from the sun.
Urgent roof repair
If your room is flooded or you have active leaks that threaten your furniture, decoration, and normal operation of the room, then you need urgent repairs.
Our team can enter the production works related to the elimination of leaks within 24 hours after receiving the application.
How it works:
- Call – You call us, voicing that you have an urgent case that requires an immediate response;
- Survey – Within 2-4 hours our design engineer comes to you and performs the necessary survey;
- Drawing up a Technical Specification – Within 1 hour after the examination, the engineer draws up a detailed Technical Specification for solving your problem and submits it to the estimating department;
- Estimate – Within 2-3 hours, the estimating department prepares an estimate by transferring the received Technical Specification into the estimated program.
- Contract – after you approve the estimate, a contract is sent to you within 1 hour, where all the conditions of cooperation are prescribed, and most importantly, our guarantee for the work performed;
- Works performance – We do not have hired teams or subcontracts, respectively, the mobilization of our employees to go to work takes no more than 8 hours.
Prices for the repair of various types of roofs
The cost of repairing a flat-rolled soft roof:
Description of work | Unit of measurement | Price in $ |
The arrangement of surfaced waterproofing on the horizon in 1 layer | m2 | starting from 8 |
The arrangement of surfaced waterproofing on the horizon in 2 layers | m2 | starting from 12 |
The arrangement of surfaced waterproofing on the vertical in 1 layer | m2 | starting from 13 |
Application of coating insulation in 2 layers | m2 | starting from 12 |
Spraying of liquid rubber | m2 | starting from 8 |
Applying liquid rubber manually | m2 | starting from 10 |
Applying the primer | m2 | starting from 5 |